view all Case Studies
Walking the Walk: Dansko Headquarters Goes Green on Top
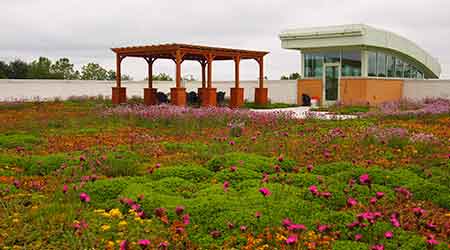
When it comes to sustainability, Dansko founders Peter Kjellerup and his wife, Mandy Cabot, truly walk the walk.
September 23, 2016 -
Roofing
When it comes to sustainability, Dansko founders Peter Kjellerup and his wife, Mandy Cabot, truly walk the walk. They have a passion for the environment and believe we should leave the Earth in better shape than we found it.
One step at a time, they are working to make their goal a reality.
Dansko is a 100 percent employee-owned company based in southeastern Chester County, Penn., that offers a complete line of footwear, including heels, boots, sandals, wedges, flats, sneakers and many types of clogs. The 90,000-square-foot corporate headquarters and retail store is a great example of sustainable design.
The building was awarded LEED Gold certification from the U.S. Green Building Council for its incorporation of numerous features — both interior and exterior — designed to reduce the building’s carbon footprint while promoting sustainability.
When it came to the exterior of the building, Kjellerup was interested in vegetated roofs. While attending an architectural trade show in Delaware, Kjellerup and Daria Payne, who is now Dansko’s director of facility management, met local Garland representative, Bill Pancoast. That meeting led to a long partnership between Garland and Dansko.
“If you can call a roofing manufacturer a partner, Garland was a great partner in the construction of this building,” says Payne. “Bill stayed unbelievably involved throughout the entire project, even after its completion.”
About a third of the building’s roofs are vegetated. The plants and shrubs on the green roof at the Dansko store can be seen through the clerestory windows. A second roof has a patio with a pergola and is accessible to employees. The last, and largest of the three, is neither accessible nor visible, but it covers the entire east wing of the building. Each roof contributes to three sustainable functions, including increased insulation to reduce the building’s cooling costs, rainwater management, and material conservation by extending the life of the roof.
Due to the complex nature of vegetated roofs, it took a team of people to determine the best approach to the design and installation. The team included Pancoast, Paul Andrew Sgroi, AIA, LEED AP, principal at Bernardon Haber Holloway Architects, and Michael Furbish, president and founder of Furbish, a Baltimore, Md.-based company specializing in green roofs, green walls and living systems.
“Our vegetated roofs were a success right from the start. More often than not, you’ll hear about an installation that just can’t get going and struggles for several years before it’s established. Some even fail and have to be replanted. We didn’t have any of that and I attribute the success of our roofs to the team,” Payne says.
Garland’s high-performance modified bitumen roofs were installed beneath the planting medium on the vegetated roofs as well as on other flat roof areas. The membranes selected are certified by UL Environment for their incorporation of pre- and post-consumer recycled content.
Steeper sloped areas of the roof, including a large, 7,000-square-foot curved roof, feature Garland’s premier metal roof and wall systems, which are 100 percent recyclable at the end of their life cycle and boast the industry’s highest performance in windstorm and water penetration resistance.
In addition to sustainable benefits of the various roof systems, the fact that they are all manufactured by Garland provides tremendous benefits to Dansko.
“We felt that having all the different types of roofing provided by a single manufacturer was important for the overall maintenance and long-term performance of the roof,” said Sgroi, project director, principal in charge of the Dansko project.
Next
Read next on FacilitiesNet