view all Case Studies
Roofing Retrofit: Self-Adhering Solution Streamlines Hospital Project
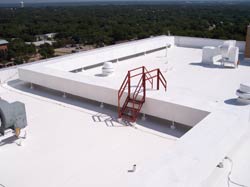
Early in 2007, it became clear replacement was the only cure for several ailing roofs on the campus of Hillcrest Baptist Medical Center in Waco, Texas. It also was obvious site conditions would make replacing the roofs a challenge
July 13, 2009 -
Roofing
Early in 2007, it became clear replacement was the only cure for several ailing roofs on the campus of Hillcrest Baptist Medical Center in Waco, Texas. It also was obvious site conditions would make replacing the roofs a challenge.
First, all products and processes had to be odor free due to the location of the roofs.
“The jobs required roofers to work above our cancer treatment center, our MRI center, and Kidsville, our children’s unit,” says Mike Dorsey, Hillcrest’s construction manager. “Air conditioning units could easily bring fumes into these areas, and that absolutely was not an option.”
The second problem was lack of access. The roofs being replaced totaled 39,000 square feet and covered multi-story facilities the hospital built around the medical center’s 1920 core building. These additions represent Hillcrest’s expansion from a 100-bed hospital to a 393-bed, acute-care facility, but the additions have compromised access to the roofs.
The contractor needed a 450-ton, 11-story crane to load materials onto roofs of varying heights. But the only staging area for the crane was the street, which the hospital needed to close to traffic – a very costly proposition.
“We had to have a roofing system that we could load onto all of the roofs in a single day,” says Kevin Carlson, the roofing contractor for the project.
Fortunately, Hillcrest discovered Garland’s StressPly® SA FR Mineral membrane, a fire-retardant, mineral-coated, SBS-modified membrane with improved self-adhesion properties. This self-contained, environmentally responsible system eliminates the need for open-flame torches, hot kettles, or cold-applied solvents. Installers position the StressPly SA membranes, remove the release film backing, and press into place.
The StressPly SA membranes eliminated concerns about fumes. Just as important, the membranes’ structure helped the hospital lower installation costs. Because the system is self-contained, crews could load the materials onto the medical center’s roofs in less than 10 hours. And because the system required no additional adhesives, the contractor could complete the project with smaller-than-average crews.
“With the self-adhering membrane, a four-man crew can do what it would normally take seven men to accomplish,” Carlson says. “That’s where the savings are realized.”
Carlson’s crews first had to remove the old single-ply roofing, install one-half-inch insulation board, and then apply the StressPly SA membrane.
“The membrane is high quality, very flexible, and easy to work with,” Carlson says. “And because the release backing is split down the middle of each roll, it’s no problem to keep the rolls nice and straight as they are applied.”
Once crews installed the roofs, they topped the membrane and membrane base flashings with Pyramic® highly reflective, white acrylic elastomeric coating, an Energy Star-qualified product that can reduce energy requirements by up to 60 percent.
Crews sided raised parapet walls with R-Mer™ Lite metal, through-fastened wall panels. They also treated vents with Rust-Go® VOC-compliant coatings for metal surfaces. Garland’s 30-year Partnership Pledge warranty applies to the entire roof assembly.
Throughout the project, which crews completed in just over a month, the hospital experienced no downtime or disruption.
“In spite of our challenging situation, our needs were met beyond our expectations,” Dorsey says.
Next
Read next on FacilitiesNet