GAF
Cool Roof Coating Project Aids in Energy Savings
Roof coating application at Orland Park’s Sportsplex extends roof life, improves energy efficiency.
By Dave Lubach, Executive Editor
The pressure on institutional and commercial facilities to meet sustainability goals, improve energy efficiency and achieve net-zero carbon emissions continues to ramp up for maintenance and engineering managers.
One of those important but potentially overlooked areas to achieve those goals is a building's roof contents. Applying a cool roof coating to help with the energy-saving efforts is becoming an increasingly popular option for facilities.
Acumen Research and Consulting reported a surge in popularity for using cool roof coatings in North America. The market was valued at $1.5 billion in 2022 and is projected to grow at a compound annual growth rate of 7.5 percent through 2032.
“There is a growing inclination towards eco-friendly and sustainable roof coatings formulations,” the Acumen report reads. “With sustainability becoming a key priority for consumers and regulatory bodies alike, there is a surging demand for coatings that minimize environmental impact while delivering optimal performance.”
Using a roof coating also serves as a cost-efficient option for facilities, especially those in a municipality, where funds are not always plentiful or immediately available.
The community of Orland Park, Illinois, a Chicago suburb, was presented with these challenges when a roof at one of its sports facilities needed attention.
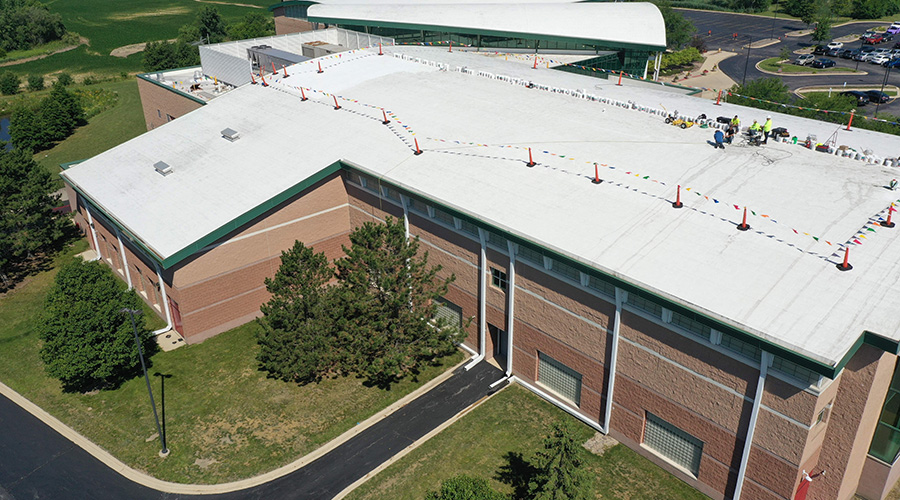
Weighing options
The Orland Park Sportsplex opened 22 years ago as a public facility in the village of 60,000 people. The facility’s activities include rock climbing, basketball, volleyball and pickleball courts, group fitness and a weight room.
Since the building is so vital to the village’s residents, keeping the facility running efficiently is essential for the community. But the time had come for village leaders to address the aging roof.
“The original roof system was composed of a polyvinyl chloride (PVC) over a polyisocyanurate insulation over steel roof decking,” says Mike Mazza, the village’s operations manager, natural resources and facilities. “The PVC roof was severely weathered and at the end of its service life. In order to keep the community safe, it was decided to invest in a new roof for the facility.”
After assessing their options, village officials opted for a roof coating instead of a re-cover or replacement project.
“Prior to recoating, the roof system was original to the structure and was approaching the end of its anticipated service life,” Mazza says.
Mazza and his staff held discussions with the village’s building inspectors and roofing consultants before deciding on a 100 percent Unisil High Solids roof coating from GAF for the project.
One of the factors Mazza had to consider with the recoating was the construction of the roof.
“The roof is made up of noise-deflecting acoustical metal, so it was necessary to avoid the use of fasteners, which ruled out most of our recovery options,” he says. “Additionally, infrared moisture surveys were performed prior to each project phase.”
Completing the project
The Sportsplex roof is broken up into 10 different independent roof areas. The three largest roof areas are barrel designs with drainage to gutters and account for 80 percent of the total roof area.
The project required recoating more than 70,000 square feet. The first phase of the project was completed in 2022 and consisted of the complex’s barrel roofs, which represented 56,025 square feet. The second recoating phase for the flat roofs took place in 2023 and consisted of 15,175 square feet.
Mazza says the $783,000 coatings project will protect the roof against leaks for 20 years.
“The contractor used two coats of the coating over a base of primer,” Mazza says. “This self-flashing, liquid-applied system meant no fasteners would puncture the acoustical roof deck and created a completely seamless silicone roof.”
When deciding on using a coating instead of other options, Mazza says the need to avoid fasteners on the roof ruled out a recovering job or replacement roof. Recent roof repairs in the village also influenced their decision.
“We had recoated the roofs of other village facilities and believed this to be a solid approach to extending roof life expectancy,” Mazza says.
Coatings also helped the village with maintenance concerns going forward.
“We also addressed gutter issues and had three roof ladders installed to assist our maintenance staff as they assess the roofs,” Mazza says. “And we need a light pressure wash to be done once a year during an annual maintenance inspection.”
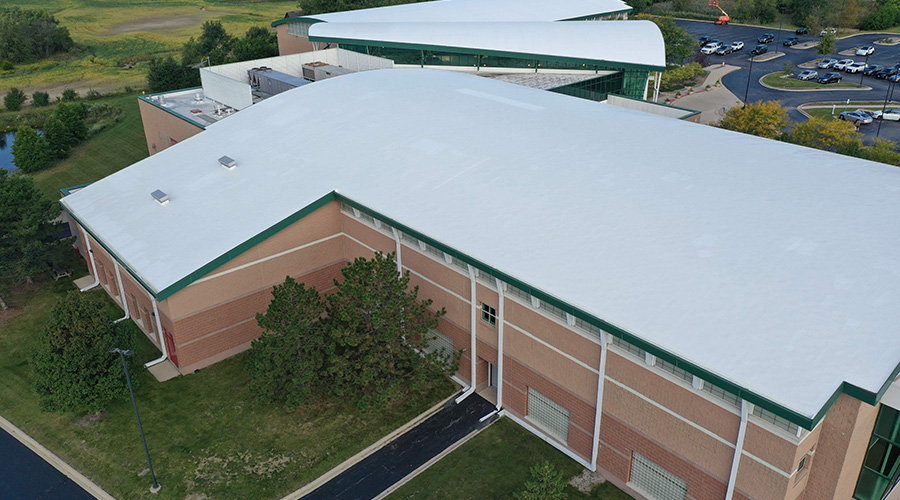
Cool roof benefits
The reflective silicone coating applied helps the building achieve energy saving goals while keeping occupants safe and dry from the elements.
Managers should choose a coating that will decrease the surface temperature of the roof, which decreases the amount of heat that is transferred into the facility, according to the Energy Star website.
“In general, traditional roofs absorb sunlight during the day, heating the building and surrounding air,” the website reads. “Roofs that are lighter in color or are reflective stay cooler than roofs that absorb sunlight.”
Energy Star listed the benefits of managers selecting cool roof coatings for their facilities.
- Keeps buildings cooler on hot days to improve indoor comfort
- Reduces air conditioning costs and strain on electrical grid
- Reduces pollution and greenhouse gas emissions
- Decreasing roof temperature and thus potentially extending roof life
- Contributes to lower temperatures in the surrounding areas and reduce the urban heat island effect
The Lawrence Berkeley National Lab Heat Island Group says a cool-colored roof can reflect up to 35 percent of sunlight and stay about 22 degrees Fahrenheit cooler than a traditional roof that looks the same but reflects only 10 percent of the sunlight.
Dave Lubach is executive editor for the facilities market. He has nine years of experience writing about facility management and maintenance issues.
Related Topics: