view all Case Studies
Fuel Cells Energize a University
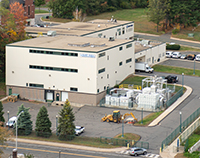
Central Connecticut State University sought a continuous on-site power solution that reduced its carbon footprint and helped it achieve aggressive Climate Action Plan goals. An RFP process revealed a stationary fuel cell power plant would be a good option for the university.
May 4, 2015 -
Power & Communication
As a college committed to environmental sustainability, Central Connecticut State University (CCSU) sought a continuous on-site power solution that reduced its carbon footprint and helped it achieve aggressive Climate Action Plan goals.
An RFP process revealed a stationary fuel cell power plant would be a good option for the university, and a 1.4 megawatt DFC1500 fuel cell power plant manufactured by FuelCell Energy was installed on CCSU’s New Britain campus over the course of four months. Greenwood Energy, a renewable energy investment firm, owns the plant and sells the electricity and heat to CCSU under a ten-year Power Purchase Agreement (PPA). FuelCell Energy operates and maintains the plant.
CCSU’s 165-acre campus, comprised of approximately 40 buildings, generally consumes from 3,500 to 4,000 kilowatts (kW) of electric power, up to a peak of about 5,000 kW. In addition to the fuel cell power plant, which generates 1,400 kW (1.4 MW) of power, the university operates two gas-powered generators which can produce about 2,500 kW of power combined. Integrated completely into the university’s electric power system, the fuel cell power plant feeds into the campus’ primary 4160 Volt bus via a step-up transformer, which then distributes power through step-down transformers to the entire campus.
The fuel cell plant integrates directly into CCSU’s existing energy infrastructure in a Combined Heat and Power (CHP) configuration, where the high quality heat is used to produce steam for campus heating and absorption cooling. The university directs the power plant’s heat energy into a Heat Recovery Steam Generator to supplement its primary steam system for hot water and heating needs and for steam absorption chilling. In addition to two electric chillers, the university operates a single 1,500-ton steam absorption chiller. When steam is not being used for heating purposes, as in the summer months, use of this chiller helps reduce electric power consumption.
CCSU operates three 65,000 pound-per-hour boilers in its main plant, and the heat from the fuel cell power plant produces 1,600 to 2,000 pounds-per-hour of steam. While a modest percentage of CCSU’s total requirements, engineers estimate the value of the steam at about $1,600 a month, or more than $19,000 annually in addition to the estimated $100,000 savings for electric power.
Next
Read next on FacilitiesNet