Building Occupants' Requirements Make Every Energy Project Different
The Virginia Department of Corrections has been using performance contracting to tackle water conservation and solar energy initiatives. Conventional toilet fixtures and lavatory valves have been upgraded to low-volume models. Since the program started in July 2007, more than half a billion gallons of potable water have been saved. Solar thermal energy is being used to displace the use of propane to heat water — one of the most effective applications of solar technology. More than 300 solar thermal collectors will be installed at St. Brides Correctional Center.
"Technically, it was important to work hand-in-hand with the customer in the development and implementation of solutions," says Richard Barrett, account executive for Johnson Controls state government energy solutions, ESCO for the project. "When working in corrections, it's essential to have the customer's total verification to make sure that all expectations are met."
In the corrections environment, communication and other aspects of project management take on a new level of importance.
"Any energy services provider that works in the correctional environment must understand the importance of stringent time lines, uncompromising safety standards, and smooth project implementation," says John Poggi, account executive, Johnson Controls.
Although few environments are as sensitive as a correctional facility, almost any group of building occupants brings special considerations of one sort or another. A case in point is a multiphased, $11.5 million energy performance contract let by the Metropolitan Development and Housing Agency of Nashville, Tenn. The project began in 1997 and was later extended in 2009. The ESCO is Siemens Industry Inc.
Projects have included use of more energy-efficient lighting technology (replacing 100- and 150-watt incandescent bulbs with 13-watt CFLs), water-saving measures (low-flow fixtures), improved HVAC systems, and renewable methods such as geothermal design and photovoltaic arrays.
The schedule was a big challenge in getting projects completed. "Time was short trying to get work done in occupied units; it was often difficult to manage logistics with the residents," says Ed Shewmaker, modernization coordinator and staff architect for the agency. "Also, based on the performance contract itself, we found ourselves with only six months to design almost $12 million worth of work, so we had to research different types of equipment, review the way they interfaced in our buildings, and bid out contractors all at the same time."
Value of Mock-ups
The agency's experience has yielded useful lessons for other facility managers. One is the value of mockups.
"During our first round of lighting upgrades in 1997, we installed lower temperature (2,000 K) CFLs in frosted-lens fixtures throughout the units, only to hear a lot of residents, particularly elderly ones, complaining that the light output wasn't sufficient," says Shewmaker. "At a cost of $3 per fixture, we ended up changing those bulbs out to higher temperature (4,100 K) CFLs in fixtures with clear glass coatings which offered a whiter light closer to daylighting."
Another important lesson is to keep building occupants in mind when selecting products. Shewmaker says that the agency removed more complex thermostats that they'd installed upon learning that they were too difficult for residents to use. "If things aren't simple, people won't use them and you're undermining the benefit," Shewmaker says.
It's not just energy data that makes projects like these a success. That's important, of course, but so is information about technology options and operations as well as occupant needs and behaviors.
"We'd advise owners to always stay involved and on top of maintenance, design, energy usage patterns and new technologies," Shewmaker says. "And make sure you keep people on staff who are willing to learn and engage in training and education."
Susan Bloom is a freelance writer with 20 years of experience in the lighting and electrical products industry. Her specialty is energy-efficient and green products.
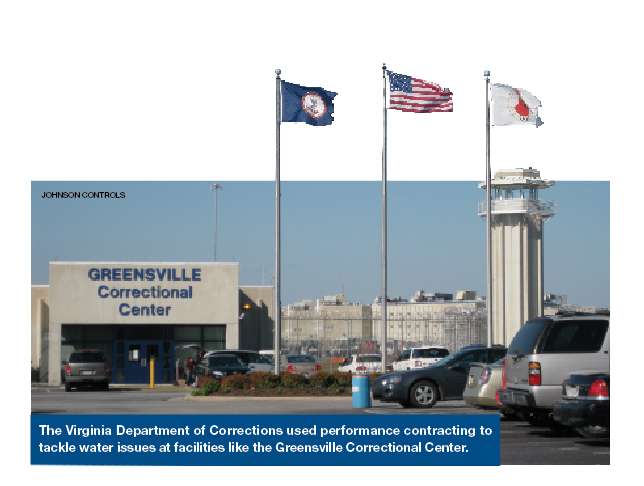
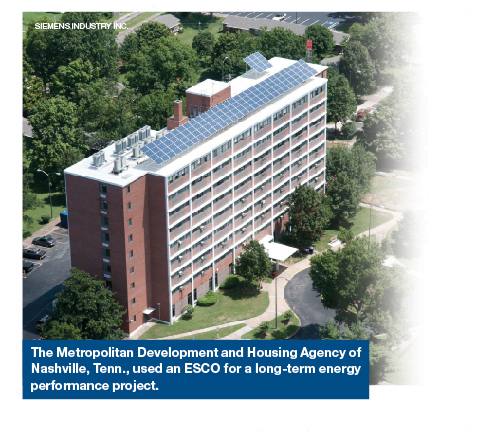
Steps to Lower Energy Bills
In most organizations, there is a range of opportunities to minimize energy costs. In fact, one challenge for facility managers can be the difficulty of deciding what to address first.
One way to tackle that problem is to divide energy reduction efforts into three phases — energy efficiency, renewable energy, and supply management, says David Anderson, executive vice president, Ameresco.
"Understand your usage and reduce your energy load first," says Anderson. "Energy efficiency measures are the most effective means of doing this." Next up is the question of renewable energy. Renewables will not only reduce the consumption of fossil fuels — reducing the facility's carbon footprint and supporting sustainability initiatives — but also provide some price certainty. The big question: Is it financially viable for an organization?
A third step is to bid your commodity energy requirements. "Good supply management will help ensure that you're purchasing whatever remaining energy you need as cost-effectively as possible, which is particularly important in the current economic climate," says Anderson.
It's important to keep the basics in mind as the process of working with an ESCO unfolds. Good communication should be a priority from the very start of the project, as the project is being developed and before the final contract is signed. The facility manager should have clear expectations and know "exactly what's being delivered in terms of costs and savings." As the project proceeds, having a schedule for update meetings helps ensure that everyone is on the same page.
The market for products and services that can reduce energy costs is expanding every day, and facility managers should keep their eyes peeled for opportunities. "Be open to innovative solutions and generate as much competition as possible when seeking out vendors, services, and technology," Anderson says. "This will help ensure that you have the greatest flexibility and the broadest spectrum of opportunities from which to choose."
— Susan Bloom
|
Related Topics: