Pay Attention to Water, Energy Issues When Designing Restrooms
Low flow, 0.5-gallon-per-minute (gpm) aerators are common and required at most public lavatories these days and are generally not problematic. However, when used with some of the new energy saving equipment available today, there can be issues. A couple of examples of products that may not pair well with low-flow aerators are on-demand water heaters and battery saving hydro-generators available for installation at lavatories.
Not all on-demand or instantaneous water heaters will activate if a lavatory has a low-flow aerator, even if the unit is designed to operate at 0.5 gpm flow. Because a faucet is a mixing valve, the flow drops closer to 0.25 gpm. Also, there may be a filter on the inlet of the water heater that, if clogged with debris, may cause the flow to drop below 0.5 gpm, which may not be enough for a user to wash his or her hands. The solution may be to install a higher flow, 1.0 gpm aerator.
But a higher flow aerator has its own considerations. One is LEED points — a 0.5 gpm aerator uses less water so it is a larger contributor to LEED. Also, some hydro-generators may require a minimum 1.0 gpm aerator to activate, resulting in a similar problem as the 0.5 gpm aerator.
Some locations just aren't good fits for low-flow in the first place. At a kitchen sink, a 1.5 gpm aerator is fine if it's in a break room, where people are mainly using it for hand washing or rinsing out a cup. But a low-flow aerator at a janitor sink, where cleaners fill a bucket on a regular basis, could become a regular annoyance.
What's Next?
With the world population and water shortages increasing, more dramatic water efficiency strategies will be required. Composting toilets are still seen as a solution just for campgrounds or remote locations without a connection to a city sewer system. But the interest in green design and net-zero buildings is increasing their presence in urban locations. Not only do they save water, but they also make usable fertilizer.
Composting toilets require space on a floor below the fixture for the collection tank, as well as weekly maintenance. This includes spraying liquid, adding bulk material and mixing the pile. The space required for collection at each fixture is not small and the chutes below the fixtures are larger than your average sewer pipe. They also require electricity for a fan. The costs may outweigh the long-term benefits for many organizations at this time. But with the growing emphasis on water conservation, we're likely to see wider acceptance of composting toilets.
Victoria Haynes, LEED AP BD+C, joined Interface Engineering in 2003 after 11 years as a journeyman plumber. Haynes can be reached at victoriah@interfaceeng.com.
TIPS AND TRICKS
Rainwater-Supplied Fixtures
Awater-saving practice gaining momentum is to flush toilets with collected rainwater. These systems require careful consideration. First, water quality might be an issue. Roofing material or lack of proper filtration can cause water in the bowl to take on a hue that indicates to the user that the fixture is either not clean or was not flushed by the previous user. This problem may be solved though by simply managing occupant expectations. For instance, one facility manager posted signs suggesting that the user regard any water discoloration as a harmless by-product of the organization's commitment to sustainability.
Facility managers also have to be sure they designate space in the building to locate the collection and pumping systems. The rainwater harvest system itself doesn't have to be elaborate to be effective — a below-grade storage tank with a pump and basic filtration system consisting of a first flush diverter and bag filters will yield flushing-quality water. When combined with low-flow fixtures this can help get several points in the water efficiency section of LEED. If the pump is located outside the building in the storage tank, all that is needed inside the building is a place for a pressure tank and the valves and other appurtenances.
If the owner prefers to have the storage tank above grade — perhaps to advertise to the public a commitment to saving water — space for a smaller day tank can usually be found inside the building. Because
an above-grade system is more susceptible to bacterial growth, a UV filtration system with a circulation pump should be added to improve water quality and the day tank should be of an opaque material. There are also UV immersion filters available to install inside the tank itself, eliminating a circulation pump. A back-up water supply to the tank allows for refill if the water level gets too low, and also provides a fresh water supply for tank maintenance. Water piping to the storage tank from the roof should be plastic or polyethylene, to reduce the possibility of discoloration from rust.
— Victoria Haynes
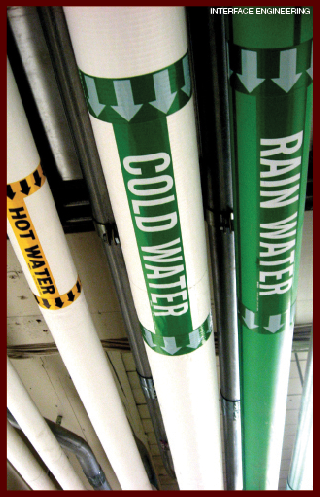
|
Related Topics: