The Real Cost of Deferred Maintenance
December 22, 2016
When it comes to budgets, practically every facility owner and manager has the same dilemma: doing more with less. When faced with shrinking budgets, it’s tempting to delay general maintenance, system upgrades or building repairs to a future budget cycle—or even postponing them indefinitely until funding becomes available.
This trend in deferred maintenance is concerning. According the
US Energy Information Administration’s 2012 Commercial Building Energy Consumption Survey, roughly half of all commercial buildings were constructed before 1980. With a median age of 32 years, commercial building stock in the United States is fairly old. U.S. schools are even older, averaging over 40 years in age. But while deferring maintenance may seem like a viable cost saving measure, the reality for many of these buildings is often years of neglect that can result in significantly greater expenses in the long run.
Repairs Quickly Become Replacements
Stanford University recently published a report titled
"Guidelines for Life Cycle Cost Analysis” which explains how as a building or campus ages, the cumulative cost of operating and maintaining facilities significantly impacts the overall budget — not just the maintenance budget. Even when funds are set aside to construct new buildings, they rarely extend to the ongoing operational costs vital to maintaining the facility and slowing the decline of building utility and performance.
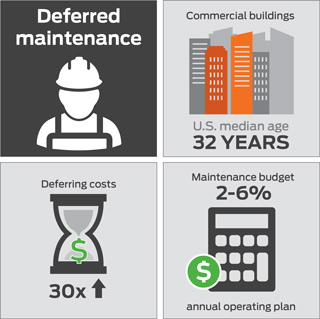
The greater issue with deferred maintenance is that it only grows in scope — and cost — the longer it is prolonged. When a repair is delayed, it is still subject to the daily use and abuse of building occupants. In fact, it’s not uncommon for a “repair” to turn into a “replacement” because, in the process of being deferred, it becomes completely broken. Replacing a door, lock, window, etc., is much more costly than simply repairing it in a timely manner. But not only is the hard expense higher, there is also a frequently overlooked cost in staff productivity as replacements typically take much longer to complete than repairs.
According to the
Handbook of Facility Assessment by James Piper, this phenomenon is particularly evident when repairs to mechanical and electrical systems are deferred. Deferring maintenance, especially in mechanical and electrical systems, frequently turns minor problems into major system failures. As the number of system failures increases, the need to replace those systems becomes self-evident.
However, facilities that have implemented comprehensive preventive maintenance programs have found that the operation of their systems is more reliable, and those systems also last longer.
Preventative Maintenance Measures
Projects that are put on hold, repair that is neglected, or maintenance that is ignored adds up to a costly and complex problem. The cost of deferred maintenance could potentially be 30 times that of the early intervention cost.
The importance of preventative maintenance cannot be overstated. Experts estimate that between two and six percent of an annual operating budget should be spent on preventative maintenance in order to effectively minimize a facility’s rate of decay. Prevention not only saves money, but it helps facilities avoid replacement — which requires capital assets and often an extensive process from evaluation and design to funding and implementation. By nature, preventative maintenance is the least disruptive, singular in resolution, planned for in advance
and often includes training for future maintenance. Most of all, it helps reduce building failure and poor conditions that can negatively impact mission critical building operations, a company’s image, tenant retention, energy efficiency and employee morale.
Periodic Facility Assessments
Facility managers should periodically conduct assessments to identify, evaluate and report on the condition of their building. Facility assessments evaluate existing conditions and identify any deficiencies. This information can be used to identify existing problems, develop budgets for future maintenance and capital renewal projects, and track deferred maintenance backlogs.
All building components and infrastructures should be evaluated during an assessment. This includes mechanical and electrical equipment, building shell, interior structures and finishes, transportation systems, and building site.
Making the Case
As the primary reason for deferred maintenance is budget cuts, you’ll need to make a convincing case in order to keep the necessary funding for repairs available. Here are a few points to bolster your case:
• Increased liability risk: Demonstrate clearly how the decision to defer maintenance can significantly increase liability and safety hazards, while at the same time decreasing productivity levels and negatively impacting mission critical building operations.
• Do the math: It’s easy to focus on the immediate cost savings of not performing maintenance and repairs. Calculate the potential replacement costs resulting from postponed maintenance and point out the sizable differences in price.
• Show examples: Dig up key examples from the past that show how significant the long-term costs can be when maintenance is deferred.
Bottom line, the faster you conduct a repair, the better. Being proactive in maintaining a facility can dramatically increase the productivity of staff, the longevity of the building and the management of valuable resources. The likelihood of incurring greater costs only increases with each instance of deferred maintenance. By making the business case for funding and proactively managing maintenance every day, you’re less likely to develop a deferred maintenance backlog that seems too overwhelming to overcome. Forsaking preventative and routine maintenance will only lead to buildings failing prematurely — and that’s the most expensive outcome of all.
This Quick Read was written by Ann Geissler Timme, end user marketing manager for Allegion. For more information about deferred maintenance and assessments, visit us.allegion.com/industries or email Ann at ann.timme@allegion.com.
This Quick Read was submitted by Naomi Millán, senior editor of Building Operating Management magazine, naomi.millan@tradepress.com.
Next
Read next on FacilitiesNet