Five Minutes With Audio & Video Home
fiveminuteswith
Personnel Management and Cost-Saving Strategies with Bruce Canter
Bruce Canter, director of operations with the Delaware Art Museum in Wilmington, Del., discusses strategies that have saved his organization money, including outsourcing, energy-efficieny initiatives, and utility partnerships.
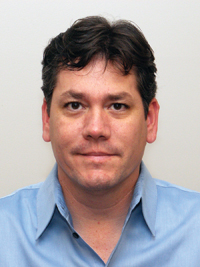
Bruce Canter
Director of Operations
Delaware Art Museum
Wilmington, Del.
How have you used outsourcing as a way to save money while ensuring maintenance and operations are not negatively affected? How much money did outsourcing / staff reorganization save?
Our largest outsourcing initiative was actually in our security department, saving more than 30 percent annually. Interestingly enough, the savings were really the result of reduced staffing hours, not necessarily because of the hourly wage difference. We were able to reduce our overall staffing hours because we didn't have to worry about coverage for holidays, sick time, and vacations. Also, we're now able to schedule hours without worrying about part-time and full-time employees getting enough hours in a given week.
On the maintenance and operations side, we were able to go without filling positions lost through attrition and instead supplemented in-house staff with outsourcing some maintenance tasks, such as painting, minor plumbing, electrical, and light HVAC work that our in-house staff had been performing. Outsourcing some of the routine tasks left us the ability to be flexible and react to normal business needs, unexpected maintenance issues and emergency situations with our remaining staff.
How do you facilitate a positive work environment among in-house staff and contracted service providers?
Communication. Honest, timely, personal communication. Throughout my career, the No. 1 complaint or feedback I have heard from employees is the lack of communication from senior management. I'm lucky that our staff is small enough that I can see and talk to most everyone routinely. Our communication is open enough that they feel comfortable to ask me any question on their minds.
They know the struggles we have in relation to funding our institution, and they understand the pressures that managers are under to be as efficient as we can with our expenses and manpower. By engaging them in open communication, they have the ability to see the bigger picture of planning for the continued success of the museum, and they essentially see where they fit into that plan. The contract personnel see this communication and open dialog, and it makes them feel a part of something as well, instead of them just performing a task.
What activities have you undertaken to reduce utility costs, including gas, electricity, sewer and water?
There are a few things we have done recently to reduce expenses. The most impactful initiatives were nightly setbacks of the HVAC temperature settings, and we locked in to a multi-year contract with our electric and gas suppliers.
With temperature setbacks in non-critical areas of the museum during off-hours, we have been able to reduce our energy consumption by over 2 percent annually. That may not sound like much, but over the course of the year, that's actually quite a lot in terms of real expense savings.
It takes some time and attention to keep track of events where we need to adjust the settings in places the public uses, like our auditorium. The HVAC system is essentially off most of the time, so when the room is scheduled to be used, we need to make sure the settings are scheduled, as well.
Our museum is relatively small, but our energy consumption is above average for our size, due to the precise conditions we need to maintain for our collections. Temperatures must be 70 degrees at 50 percent humidity, with plus or minus 5 percent all day, every day. So, unfortunately, both our chillers and boilers run year round.
We worked closely with an energy-management consultant to bid on both gas and electric suppliers and signed a multi-year contract with the lowest rates. The energy manager had the ability to leverage a lower supply rate by combining all of his other clients under the same management firm.
Other savings come from the addition of solar film on all windows, separate meters for cooling-tower make-up water to reduce sewer-water expenses, and the use of compact fluorescent lamps (CFLs) wherever we can.
How do you continue to motivate maintenance and operations staff amidst tough economic times?
Without the ability to provide them with the monetary compensation they look for and deserve, the only thing I can help them understand is that we are all in the same situation. I like to think that the majority of the employees at the museum are here because they choose to be.
The working environment is great, and I think they all realize, as a not-for-profit museum, we are serving the community and not ourselves. That attitude goes from the director through to the entire staff. They all see the difference we make with our offerings and community service, and it gives them the satisfaction of knowing they are part of something bigger - and that it's not just a job.
Looking ahead, how will the museum's financial situation impact maintenance and operations activities?
I don't think we can do any less than we currently do to maintain the facility in the standard that we need for our collections and visitors. Until the museum's financial situation is where we are intending it to be, we are kind of in a holding pattern. We continue to be able to concentrate on our critical infrastructure, while also making sure our visitors have a first-class experience. The museum is gearing up to celebrate our centennial starting later this year, so I know we are not going anywhere. We just need to be positioned to take advantage of the better times to come.
Find more on this topic:
utilities, utility costs, energy efficiency, energy conservation, outsourcing, temperature monitoring, hvac maintenance, security
posted: 5/6/2011