« Back to Facilities Management Lighting Category Home
Warehouse Renovation Taps LEDs for 89 Percent Reduction in Energy Used
December 17, 2015
- Lighting
A facility that started out as a cotton mill in 1880 went on to become a manufacturing facility for awning, marine, military, and other fabrics with customers around the world. Then Glen Raven Inc. reinvented itself again as Glen Raven Logistics and needed to renovate the former plant, located in Altamahaw, N.C. President Dan Cox envisioned a full-service logistical partnership for his customers utilizing the space, and both lighting and layout were selected as areas for improvement.
Specifically, the 400 watt metal halide HID fixtures in the plant—once positioned to illuminate the large machinery at the center of the facility—had to go. These lights stayed on most of the day, even when there wasn’t any activity in the warehouse or freight docks.
“We were spending a lot of money on virtually wasted energy for lighting when there wasn’t any activity in the warehouse,” stated Cox. “We really needed a lighting system that was smart enough to know when to come on fully when needed, and either dim down or turn off when there wasn’t activity in the warehouse.”
The relighting of the warehouse centered on using Cree LED lighting with embedded “smarts” — intelligent lighting that could illuminate the space more efficiently and effectively.
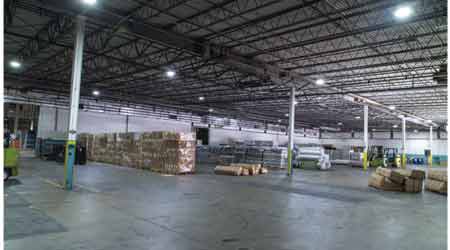
After: Glen Raven Logistics warehouse with Cree CXB Series High-Bay LED Lighting. Source: CREE
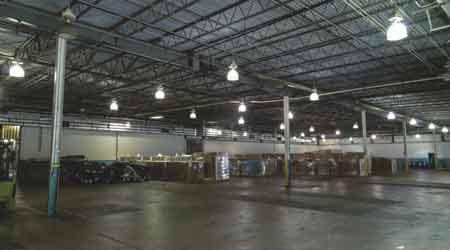
Before: Glen Raven Logistics warehouse with metal halide HID fixtures. Source: CREE
Cree CXB Series High Bay fixtures, incorporating zero re-strike time, allow integrated motion sensors to turn on quickly with any movement in the warehouse. They also turn off via a timing sensor that can be adjusted by personal and operational preference. In the Glen Raven facility, the off time is set at four minutes after sensing no motion in the warehouse. This feature is assisting in delivering a large impact on the energy savings.
The warehouse loading dock area has much lower ceilings, so not as much light was required as in the high-bay areas of the warehouse. There, Cree CPY250 canopy lighting, with programmed motion sensors and dimming, was used. The flat lenses in the CPY250 fixtures eliminated any problems with glare that had been an issue with the lower areas of the warehouse. The CPY250 LED fixtures drop to 20 percent energy while dimmed, and turn off totally when no motion is sensed.
“We are watching our monthly energy costs in anticipation of surpassing our anticipated savings,” states Mike Harrington, Glen Raven Project Manager. “The entire organization is excited to receive the almost immediate financial impact on the energy conservation in our warehouse. Not only did we cut the number of high energy fixtures by 50 percent, but we are now able to use the lights only during occupancy, greatly reducing the amount of time that we are burning energy. This goes along perfectly with our corporate sustainability values, as we are landfill-free in all of our US facilities”
In addition to saving energy and improving lighting levels and light uniformity, the number of fixtures needed in the facility dropped from 274 to 122 — a 56 percent reduction. Cree also assisted in identifying and obtaining utility incentives for the project, which contributed to reaching a positive payback in less than two years.
“I am extremely proud of Glen Raven for making the investment in this LED lighting project. It is proof that we, as a company, are taking the necessary steps to create the safest and most environmentally sustainable work place in our industry,” commented Steven Losiewicz, Glen Raven Logistics vice president of operations.
For more information on CREE lighting solutions, visit http://lighting.cree.com
Visit www.FacilitiesNet.com/lighting for other LED lighting news and information, including How to Recommission and Revitalize Lighting Control Systems.