view all Case Studies
Providing HVAC for Massive Structure is Pure Efficiency
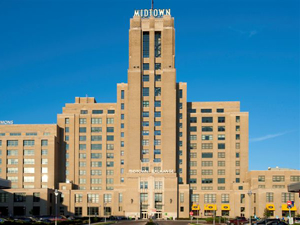
One of the key challenges in retrofitting Midtown Exchange into a diversity of modernized, smaller spaces was the desire to install state-of-the-art mechanical systems.
March 23, 2010 -
HVAC
In the mid-1920s, Chicago-based Sears Roebuck & Co. made a strategic choice to move many of their stores away from downtown areas. Perhaps they knew they were planting seeds that would eventually grow into the 21st century retail mall industry.
One of the most remarkable of these facilities opened in 1927 on the outskirts of Minneapolis. It featured a 17-story, 230-foot-tall central tower and acres of pavement for people who made the store a destination, a getaway. It served Sears’ retail and wholesale operations for 57 years.
Gradually, the city grew around the building, now in use no longer. But a new vision for the abandoned building was to repurpose it, shaping it into the swank, inner-city “Midtown Exchange” living and retail environment. It now offers one million-plus square feet and 329 living units, of which 80 are considered high-end condominiums.
There are also townhouses and luxury apartments and large office and retail segments. In addition, a nine-story, 400,000 square foot wing of the restored building is occupied by the world headquarters of Allina Health Systems.
In square footage, Midtown Exchange – at just more than one million square feet in size – is the second-largest building in Minnesota, second only to the celebrated Mall of America.
One of the key challenges in retrofitting the massive, old structure into a diversity of modernized, smaller spaces was the desire to install state-of-the-art mechanical systems.
“We chose super-efficient, water-to-air heat pumps by ClimateMaster because – compared to traditional HVAC equipment – they can be installed for less money,” says Bill McKoskey, a registered professional engineer and president of Horwitz-NSI in Minneapolis. Horwitz NSI was responsible for the Midtown Exchange renovation-project HVAC design – essentially, a huge hydronic system – and engineering and installation.
“The heat pumps also offer the flexibility of being easy to zone,” says McKoskey. “And you can add heat pumps to the overall design as needed – so they give you an advantage in scalability. There’s little question that water-source heat pumps are one of the highest efficiency systems on the market due to their ability to transfer heat through the building's piping system.”
A key consideration for the large mechanical system – with hundreds of heat pump components to connect – was the circulator pump stations chosen to move fluids from place to place, distributing precious thermal energy and BTUs.
“We installed three large Taco pumping stations,” says McKoskey. “One is a variable flow heating water loop which matches flow to the building’s loads through the use of variable speed drives. The other loops serve the heat pump core water loop and the cooling tower loop.”
“Because energy efficiency was the driving force behind the building’s mechanical system retrofit, they installed the ultimate combination of high efficiency pumps and motors coupled with the variable speed drive,” says Tom McCormick, product manager of commercial pumps, Taco, Inc. who – after seeing the system design – was impressed with the approach taken to retrofit the giant structure. “When the speed of the pump motor is varied to meet changing climate conditions – both inside and outside the building – the motor uses the least amount of energy.
“The pumping stations they chose provide the maximum wire-to-water efficiency, taking into account the combined efficiency of the pump and motor together,” says McCormick.
“We have quite an assortment of water-to-air equipment scattered throughout the building, depending on what the space requirement calls for,” says Scott Rollings, CEO of Minneapolis-based Energy Efficient Resources, a manufacturer’s rep firm. “This was a superb project to be involved in; it helped immensely that mechanical system design was handled so well from the beginning.”
Chief among the environmental considerations, especially for an older, retrofitted building with many diverse uses, was the need for the chosen mechanical systems to operate quietly.
“Several professionals involved in the project raised concerns about this,” says McKoskey. “So – for the architects and the development people from Ryan Cos. and several others – we built a mockup vertical heat pump at an older building here in town. And when it was operational, we led a group there to see and hear the system in operation; everyone was favorably impressed.”
As an added precaution, the developer chose to install insulated G-panels on all heat-pump enclosures in the residential units, further dampening any operational noise that might be generated.
As a registered historic structure, it was mandated that Midtown Exchange be left very much intact following any renovations.
“One of the things about historical buildings is the need not to see anything new,” says McKoskey. “We were able to satisfy that requirement because all of the individual water-source heat pump units integrated with the boiler and cooling tower for the exchange of heat – and the only thing visible on the exterior is the cooling tower itself, which in this case is in a level-13 penthouse. That worked out to everyone’s satisfaction.”
“In contrast, one of the essentials for a conventional VAV system would be louvers, and they’re an immediate deal-breaker with the folks who guard against visible, exterior signs of modern systems – they’re not permitted on historical buildings, or at least to be apparent,” says McKoskey.
“But when you’re using heat pumps, the only air we’re moving is the ‘makeup’ air,” he says. “So that means you’re using a much smaller duct – which, in this case, is a definite advantage for the heat pumps in maintaining the integrity of the historical appearance throughout the building.”
An exception to the exclusive use of water-to-air heat pumps was made at the Allina headquarters. There, Horwitz NSI professionals installed a traditional VAV heating-and-cooling system. “But even there we also installed some ClimateMaster heat pumps because Allina has a critical 24/7 temperature requirement for their data facility,” says McKoskey. “So we just tied that to a dry-cooler loop, which is a totally separate system from the rest of the building.”
Further challenges grew out of the building’s quaint 1920s configuration – as well as what some of the professionals referred to as “Sears bunker construction.” After all, the building sits atop a six-foot-thick, 150,000 square-foot slab. “Like they say, ‘they don’t build ‘em like they used to,’” says Rollings. “It was as though – during construction – the rule of thumb was: ‘When in doubt, add more concrete.’”
Walls were almost as sturdy as the floors, and certainly complicated the task of modernizing the building systems.
“As a design/build contractor, I’m always working closely with architects,” says McKoskey. “At this jobsite, this was important in determining favorable HVAC routes through ceilings, walls and floors. And on this project, there were a number of architects involved – separate architects for the condos and apartments, for Allina and for retail. Of course, because of the old construction techniques, there were aesthetic treatments and designs that became extremely challenging to bring about.”
For the residential areas of the building, Horwitz technicians installed one-ton to three-ton vertical heat pumps with integral risers or piping – stacking as many as they could in similar locations, one above the other, floor-to-floor, all linked together as part of the closed water loop.
“Unfortunately, the building didn’t ‘stack’ perfectly, so we used a lot of offsets, which solved many problems, but were a key challenge in making it all come together,” says McKoskey.
According to Rollings, a lot of horizontal water-to-air heat pumps were used elsewhere throughout the project, including 10-, 15- and 20-ton units.
“Up at the top of the tower – all the way up 17 floors – is where they used to store fire-protection water,” McKoskey says. “And within that tower, today, from floors 13 through 17, there are now many elegant condominiums.”
According to McKoskey, the building also has a high-rise smoke control system that includes fire-floor exhaust, stairway pressurization and elevator shaft relief. So there was an advantage for what they termed the “point-of-use” characteristic of the heat pumps, permitting them not to cross a lot of fire barriers with large ducts. If this were done, as with a VAV system, the installation process would have been more involved, and would also have required the use of very large and costly smoke-control dampers.
“No doubt, we were dealing with a very tough building,” says McKoskey. “It’s unusually shaped and it’s extremely well-built. And that made it a difficult project.”
“So the mechanical solution we settled on was ideally suited to the challenge, and also to the developer’s stated need for high efficiency operation,” he says.
The tenants, residents, visitors and shoppers at Midtown Exchange are modern beneficiaries of a forward-looking, efficient heating and cooling design that could help prolong the building’s life another century or more.
Scott Rollings is CEO of Energy Efficient Resources in the Twin Cities.
Bill McKoskey, P.E., is president of Horwitz NSI. in the Minneapolis suburb of New Hope, Minn.
Next
Read next on FacilitiesNet