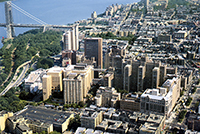
New York Presbyterian Hospital’s Columbia University Medical Center campus began a web-based energy monitoring and continuous energy oversight program in 2010. The program has saved more than $1.5 million dollars annually by improving the efficiency of the existing chiller system.
New York Presbyterian Hospital’s (NYPH) Columbia University Medical Center campus began a web-based energy monitoring and continuous energy oversight program in 2010. The program has saved more than $1.5 million dollars annually by improving the efficiency of the existing chiller system.
Cost savings were achieved through establishment of an operating matrix that selects the most efficient and cost effective chillers to run as the hospital's cooling load increases, fixing temperature sensor calibration, eliminating inefficiencies in chiller performance, eliminating excess pumping, and resetting condenser water temperatures based on the outside air temperature and relative humidity.
As part of the ongoing monitoring program, utiliVisor noted that omissions in the existing control system were forcing the hospital to run all of its cooling tower fans regardless of the load. The data analysis showed that the plant’s efficiency could be significantly improved by small additions to the existing control system. Upgrading the controls on the cooling towers was evaluated to yield the quickest payback after accounting for financial incentives from the New York State Energy Research and Development Agency (NYSERDA).
Improving the controls system allows the hospital to operate cooling towers individually (14 separate isolation valves instead of one) and gives the controls system the ability to operate the correct number of cooling tower fans (at the correct speed) based on actual plant and outside temperature conditions.
utiliVisor developed a condenser water reset schedule for the hospital and its building controls contractor that provides the control system with directions on how many cooling towers to run based on the number of chillers in operation and the outside air wet bulb temperature, with a goal of reducing cooling tower energy without sacrificing chiller efficiency.
The total cost of the controls project was $375,000, including monitoring fees, with more than $141,000 in financial incentives secured through NYSERDA’s Existing Facilities Program at a rate of 16 cents per kWh. It is expected the project will quickly pay for itself and enable the hospital to achieve significant economic benefits for many years to come.