view all Case Studies
An EMS Solution for Pneumatic HVAC Systems
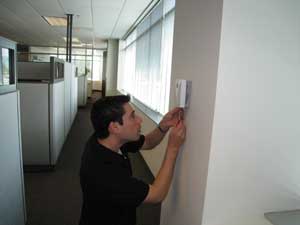
PG&E’s new offering for its customers combines with smart grid technologies to send Internet-demand response signals to the control systems in customers’ facilities and reduce energy usage during peak demands.
March 10, 2010 -
HVAC
If you manage a facility built before the year 2000, you deserve a great deal of sympathy. And you probably know why. It’s all of those pesky pneumatic thermostats that have to be set manually one-by-one and that the tenants reset to suit their preferences. These antiques keep you from instituting an energy management system that would enable you to cut energy costs and make you eligible for power company incentives.
Unfortunately, the cure can be nearly as bad as the disease. Replacing pneumatics with a direct digital control (DDC) system that would integrate with an energy management system (EMS), involves massive rewiring, months of disruptive installation and a huge expense that drives ROI far down the road. Unfortunately, DDCs have been the only viable solution for several years.
An incentive from the utility
Until recently, that is. Recently, the facility management team at Santa Clara County in California found a better solution. Santa Clara is home to Stanford University and Silicon Valley, which houses such cutting edge giants as Google, Cisco and Apple. In the company of such creativity, the county facility maintenance team likes to see themselves as forward thinking innovators as well. That’s why they were eager to get on board when Pacific Gas & Electric offered them a chance to participate in a program that would help them reduce energy use and involve an incentive.
“The county has about 11 million square feet of buildings with an annual electricity bill of around $15 million,” says Lin Ortega, utilities engineering program manager for Santa Clara. “Naturally, we are always eager to find and employ new technology that can help us reduce that burden.”
PG&E’s new offering for its customers is called the Automated Demand Response Program, or AutoDR for short. It uses a program developed by the Lawrence Berkeley National Lab (LBNL) and technologies from the California Energy Commission that combine with smart grid technologies to send Internet-demand response signals to the control systems in their customers’ facilities and reduce energy usage during peak demands. Not only does AutoDR save the clients’ money by reducing energy usage when electricity is most expensive, PG&E also offers incentive payments to customers who participate in the program.
“The auto response technology specifications were developed by LBNL in 2002,” says Albert Chiu, senior program manager for PG&E. He oversees his company‘s emerging technology and automation portfolio. “In 2007 the California Public Utility Commission asked the three Investor Owned Utilities (IOUs) in the state to commercialize and provide enabling technology incentives to our commercial customers. We developed the enabling technology so our customers can participate in the DR program with minimum investment and effort.”
Problem – two buildings with pneumatics
“It looked like a great way to reduce energy usage and we enlisted 16 of our facilities into the program,” says Ortega. “But there was a problem with two of the buildings. They were older and used more than 300 pneumatic thermostats instead of the digital direct control (DDC) thermostats used in the more modern buildings that feature computer-controlled energy management systems. The program had a deadline and we didn’t have the time to convert to DDCs. Even if we had the time, we were looking at a months-long project. I know because we’ve converted a couple of our pneumatically controlled buildings to DDC in the past. A project like that would be very disruptive to our tenants, take months to implement, and cost close to $1 million.”
A pneumatic retrofit solution
All was not lost, however. Call it coincidence or serendipity, but events came together to help the county find a way to qualify the two buildings.
“I was attending a conference at Stanford University on sustainability and was seated next to Harry Sim all three days,” says Caroline Judy, manager of intergovernmental support services for Santa Clara County. “It turned out that Harry is the CEO of Cypress Envirosystems, a company that specializes in low-cost retrofit technology. During the course of things, I mentioned our problems with pneumatic thermostats and how they were costing us a lot of money. He said he might have a solution for us. It seems Cypress had just developed a wireless thermostat that retrofits onto old pneumatic thermostats and can physically change set points from a remote location. It sounded perfect and I got his card and passed it on to Lin Ortega to see what he thought.”
At the same time, Ortega was in contact with Lawrence Berkeley Labs.
“We not only developed the specifications for the open AutoDR program, we also work as technical advisors for PG&E,” says Sila Kiliccote, senior scientific engineering associate for LBNL. “Our account manager for Santa Clara identified them as an excellent candidate for AutoDr. We passed the suggestion on to Global Energy Partners who manage the AutoDr program for PG&E and we arranged a meeting with Lin Ortega and others at Santa Clara. That’s when we realized the two buildings with pneumatics couldn’t qualify for the program as they were.
“As it happened, I had recently been approached by Harry Sim and was introduced to his wireless pneumatic thermostat technology. So here I had a customer with a need for a wireless solution and Cypress with a possible solution. It only made sense for me to introduce them.”
Cypress arranged a demo for Santa Clara and the partnership looked like it could work.
“We met with Cypress several times and had our maintenance staff join in,” says Ortega. “And we asked Global Energy Partners to do an engineering assessment and a validation and everything came up looking good.”
By that time, they were very close to PG&E’s deadline and had to move fast.
“From the first meeting we confirmed we could do the job,” says Sim. “We worked with the contractor, RSD-Total Control, to perform the site survey, installation and commissioning. We had to do it fast because the county had to spend the money by a certain date or PG&E would not give them the incentive payment. They asked if we could do it in eight days and we said we could. We worked weekends and nights so it wouldn’t be intrusive to the tenants. We did open areas during regular hours, but the offices we did when they were empty. We had several 18-hour days, but the installation is easy because the wireless thermostats retrofit directly onto the pneumatics. It takes about 15 minutes per thermostat.
“The thermostats themselves are a combination of technologies. The pneumatic thermostats have a simple thumb wheel to control the temperature. Our thermostat has a motor that turns the wheel. It’s connected to a radio so we can command and control each wheel separately from a remote location. Both the radio and the motor run off a battery. The pneumatics have their own power. A sensor inside monitors the temperature of the room. And there is a pressure sensor so our system knows the pressure in the pneumatic line.”
Instant ROI
“We now have a true wireless EMS system in both buildings,” says Ortega. “We can go online and see every zone and control each one remotely. They give us very powerful diagnostic tools and troubleshooting tools. We already discovered that several pneumatics weren’t working and have started repairing those.”
And what about savings?
“The whole project, including installation, cost about $175,000 for retrofitting 350 thermostats,” says Ortega. “We made the deadline and received the PG&E incentive of $200,000. Talk about instant ROI. Plus, we figure that we are saving $42,000 per year on electric cost for just those two buildings. And then there’s maintenance. We used to be out there all the time tinkering with the system. Now we monitor it online. We figure our maintenance expense has been cut in half from $25,000 annually to $12,500.”
For Santa Clara County, this has just been the beginning.
“This is just the start for our county,” says Caroline Judy. “Most of the buildings in our portfolio were built prior to 2000 and use pneumatics. We’re now working with Joint Venture Silicon Valley, San Mateo County, and some major commercial real property management firms and we have applied for grants from the American Recovery and Reinvestment Act to roll over this technology into the PG&E program.
For more information on Cypress Envirosystems pneumatic thermostat retrofit, contact Joe Tallant, itj@cypress.com (408) 943-2800.
www.CypressEnvirosystems.com
Next
Read next on FacilitiesNet