Five Minutes With Audio & Video Home
fiveminuteswith
adidas HVAC Replacement Program
A midsummer rooftop unit failure at a high-traffic New York City store forced adidas to take a closer look at its approach to how the maintenance and engineering department replaces HVAC units at stores across the country.
Kirk Beaudoin, the facilities manager for adidas based in Portland, Oregon, discussed the HVAC replacement program with FMD Associate Editor Dave Lubach. During their discussion, Beaudoin talked about the process the company is making during at their stores, and some of the challenges his department faces with the program.
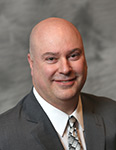
Kirk Beaudoin
Facilities Manager
adidas
1. Describe briefly the circumstances that led to adidas instituting the HVAC replacement?
* Failures happen - Equipment has a lifespan.
* Retail FM goal - provide a premium environment to maximize the consumer experience.
* New York story.
* Proactive HVAC replacement program was submitted and approved.
2. What were the program's main topics of emphasis that you focused on when implementing the program?
* Business disruption due to lost sales.
* Avoid poor consumer experiences due to uncomfortable temperatures, which results in disappointed customers and fans.
3. What kind of progress has adidas made replacing systems inside the stores?
We're slowly but surely working our way through the list. Many factors weigh into deciding to replace, such as remaining lease length and long-term plans, fiscally sound location, pending remodels, as well as the market, and weather, utility costs, and prior reliability. Plus every passing year more units hit the 15-year mark so there is no finish line.
4. What are some of the toughest challenges you've encountered during the process?
Internally, I would say just navigating through the process to identify the approved locations, and then the financial process to seek finding approvals can take time. Externally, at some locations the mall will dictate their equipment specifications versus our standards. There are hurdles with equipment changes, curb adapters, structural engineering studies and reinforcement.
We also have to watch timing twice a year, working during the spring and fall and avoiding summer and winter, while trying to hit those windows.
5. What kind of energy and financial savings has the company realized from the program?
The old equipment compared to our new standard means much more energy efficiency of 20-30 percent. With old equipment replaced, there are also cost savings realized through reduced breakdowns.
It's always important to measure what you manage. We use third party company reviews to check utility invoices for errors and accuracy. Also the stores are recording consumption data for easy remote access. It’s a work in progress, but having the data is the first step.
6.What lessons have you learned as a manager while going through the process?
Over my career worked under multiple FM processes, and prefer the proactive concept over the run-it-until-it-dies method. It's easier to sell a program if the decision-makers have lived through an example of what you are trying to avoid. You can avoid the pay me now or pay me (more) later scenario.
Find more on this topic:
retail, HVAC, maintenance
posted: 4/11/2016