Buro Happold
Tips for Facility Managers on How to Address a Boiler Project
Boiler projects cost millions of dollars. Here are steps to help managers make the best decision
By Amy Wunderlin, Contributing Writer
Boiler systems are a critical component to operating commercial and institutional facilities. They ensure warm buildings, hot water, and provide the energy to operate equipment for dozens of industries. They can also be among the costliest capital projects a facility has to undertake.
Large-scale capital projects involving replacement of boilers and related infrastructure can cost millions of dollars. Repairs can be expensive too, but they are often a more cost-effective solution to keep things running. When deciding whether it’s time to replace or upgrade boiler systems or continue maintaining with repairs, there are many factors facility managers and building owners need to consider.
Planning ahead
When it comes to any large capital project or asset replacement, advanced preparation can make all the difference.
From a financial perspective, before even getting to the question of repair or replace, facility owners and managers should already have a plan in place, says Larry Mayotte, senior operations manager at McKinstry.
“What are you doing to kind of prepare and plan for asset replacement?” he asks.
Part of that planning is looking at the assets to assess the age of equipment and its criticality to the environment. To really gauge the financial impact and timeline of asset replacement, building owners and facility managers must understand what would happen and what the risks are if an asset should fail. Based on that, managers can create a budget that aligns to either repairing or replacing the assets.
Unfortunately, not everyone takes the time to go through these exercises, forcing managers to make a choice after a failure has already occurred. When that happens, managers must evaluate the cost of replacement in an emergency versus the cost of repairs. This can lead to lost production, no longer having hot water for tenants, or leaving employees in the cold.
“You've lost the ability to control the situation, and you're almost forced into a repair or providing a temporary solution that costs an arm and a leg to put in place as you make that choice,” says Mayotte.
To avoid this costly mistake, it is essential to start planning for a future failure now. No equipment lasts forever, but with the right plan in place, managers can prolong a boiler’s life and ensure the capital is available for any bumps in the road. Here are five factors to consider when assessing assets.
1. Age of equipment
Replacing or repairing an asset comes down to a handful of decisions, depending on the application. According to Mayotte, two of the big ones are efficiency and reliability.
By knowing the age of the equipment, managers are better able to understand not only when a failure may occur, but when investing in repairs no longer makes sense or if equipment should be replaced prematurely.
“If we know what asset is aging and is getting near the end of its useful life, we know that the risk of failure increases; we know that the general cost to maintain increases,” says Mayotte. “If we can get ahead of that and avoid and plan for a specific downtime period when it can be replaced, that is going to save money in the long run, as opposed to going through the headache and hassle of downtime, temporary solutions, and then potentially getting stuck in a position where it has to be replaced. Doing it prematurely avoids all of those potential costs.”
2. History and complexity of project
When a client comes to George Reilly, principal and regional discipline leader, West Coast MEP, Buro Happold, asking whether they should repair or replace, he advises they look at it from a lifecycle cost analysis perspective, evaluating the total cost of owning and operating a facility over a period of time.
“First thing is we do the assessment, look at what the factors are, look at the infrastructure, and then start thinking about where can we take us to be not dependent on natural gas?” says Reilly. “Some of the factors there can be the age of the equipment, the lifespan. What's the maintenance history been? How compressed is the existing infrastructure? What's the efficiency of the system? We do take all these things under consideration to give our clients informed feedback.”
Peter Georgiev of RMF Engineering recommends a similar tactic, also suggesting a lifecycle cost analysis to help managers consider each scenario. And while he is clear that “boilers are meant to be repaired,” repairs can also get extremely complex and costly. Having a sound lifecycle cost analysis helps managers work through those issues.
“To repair a boiler, we usually see smaller initial capital investment,” says Georgiev. “To replace a boiler, that's a very large capital investment, but over the lifecycle of it, we might see a lot more maintenance on existing equipment. We look at those past records, and then those will be an indication of what to expect going forward.”
For example, Georgiev says that if a steam drum and mud drum are really compromised, it is a very easy decision to say, “OK, it's not worth that based on our experience and what it takes to repair that type of key component of the boiler, and it would be better to just upgrade.”
On the flipside, while just simply replacing equipment sounds like the easiest solution, there are times when it doesn’t make sense.
For example, consider a boiler that when it was installed 50 years ago was built in place. Bringing in a package system to replace it could require retrofitting the building — an extremely costly and complicated process.
“The complexity of the project and the feasibility of the construction aspect should be considered in very initial stages,” says Georgiev.
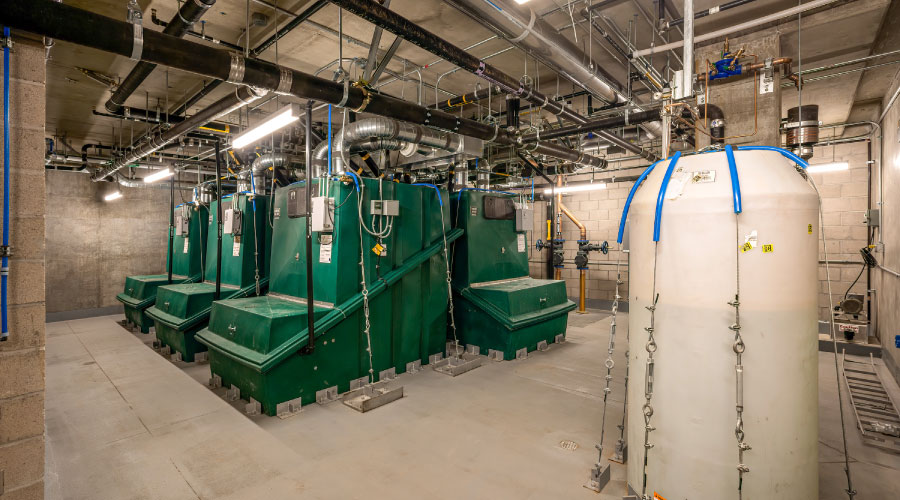
3. Criticality to operations
Understanding the importance of the boiler system to operations is a key factor in considering repair versus replace. In a 24/7 operation with steam production, having any downtime at all could be disastrous.
“We need to understand where this boiler falls within their redundancy scenario,” says Georgiev. “Is this a backup boiler? Is that a summer boiler? Maybe it's their main boiler that they use, and they cannot shut it down. We need to see how it is being operated.”
Ultimately these factors alone could be the decision between a repair or replacement.
Lead times for new equipment also come into play as it can take more than a year to receive a boiler, plus another two years to be installed. Mayotte says managers need to ask themselves if operations can lose a boiler for that long, and ask what backup plans are in place?
“Sometimes we have temporary connections or different means of providing steam, maybe they're willing to rent a boiler,” he says. “It’s not just the package equipment that is going to be the major driving force, but also phasing the boiler in would be something to consider. And if it's cost prohibitive, at that point, you might just repair it. That decision has to be made from a construction standpoint, not just from maintenance operation.”
4. Parts availability
Another thing to consider is parts availability. Since the pandemic, lead times on components, parts, and equipment has expanded exponentially. Where historically, managers may have had access to a local inventory of equipment and parts. Today, that no longer exists.
This has increased the risk for building owners and managers, Mayotte says, because they're forced into situations where replacement is no longer something that is typically available to them in an emergency situation.
“They can't just go down to the local mechanical shop and have them work with their vendor base to find a boiler that's locally available to install tomorrow,” he says.
Georgiev adds that beyond parts availability is the risk that a boiler manufacturer is no longer in business.
“Can we source tubes and some of the components on that boiler?” asks Georgiev. “If we can’t, obviously, we will recommend to maybe go to a brand-new boiler, because you're going to have that more maintainable equipment 20-plus years down the line. You can repair a boiler now, but we might have to do another repair five years down the road, and you're not going to be able to find the parts for it.”
5. Meeting your sustainability goals
At McKinstry, considerations around sustainability goals have become a big question when evaluating asset replacement.
“One of the questions that we ask is how do your own goals align with what you have in place? If your corporation or business has these large-scale sustainability plans, how does that also then affect your decision making as you plan for asset replacement and refurbishment?” says Mayotte.
He adds that while he didn’t ask that question five years ago, today it is top of mind in every one of his capital planning exercises.
“It's becoming probably one of the larger decision-making processes that folks go through as they're deciding whether it makes sense to make those investments,” says Mayotte, adding that he is seeing more clients choose to spend more money and change their assets from gas consuming appliances to electrical appliances before the end of their useful life.
If electrification is not on your mind already, now is the time Mayotte recommends to “future proof your system.” As the marketplace continues to shift from natural gas-powered boilers to heat pumps, it will be critical to look at what the capital plan will look like 5-10 years down the road.
“The number one thing that financial buyers should be thinking about and cognizant of is how do their own goals around being carbon neutral or around environmental impact or risk influence the decisions that they make,” says Mayotte.
Funding a boiler replacement
No matter where facilities are in their lifecycle, planning financially for the future is essential. Fortunately, there are many incentives and government-sponsored programs available, depending on the type of facility and the equipment.
Much of this funding is based around energy consumption and savings. For example, Georgiev handles a lot of projects in New York, which he says have benefited from the Clean Energy Fund, a fund established by the New York State Energy Research and Development Authority (NYSERDA) as a commitment to clean energy and efficiency measures. The fund, which benefits customers of many of the state’s utility companies, offers different programs that can help offset the cost of a major boiler replacement if it helps to meet the state’s clean energy goals.
Another program, the Inflation Reduction Act, expands existing tax deductions for institutional and commercial facilities for energy and efficiency measures in their buildings.
The act, which Reilly considers a “game changer,” is promoting a new wave of green building and decarbonization. Projects that once seemed illogical in terms of return on investment are now able to move forward.
“They have to qualify, and they have to follow the standards laid out by the pre-existing bills that were in place, but if they can prove that it yields double the tax deductions that existed from before,” Mayotte says. “Now, it doesn't help on a dollar-for-dollar basis. It doesn't offset the cost of the project; you still have to pay for the cost of the project, but you are able to deduct that from the tax burden that the owner would have.”
In addition to government-backed funding and incentives, there are several new options coming to the marketplace outside of traditional financing. Instead of securing financing through a lender or bank for these large-scale capital investments, some contractors are now offering energy-as-a-service. Instead of owning and operating their own boiler system, facility owners and operators can pay a monthly fee to consume energy off a plant a service provider owns and is liable for.
There are also leasing options, where managers can lease the assets and all upfront costs are paid by the leasing company. In this scenario, the leasing company is responsible for the maintenance and everything that goes into the project, while managers just pay the monthly lease amount.
Amy Wunderlin is a freelance writer based in Fort Atkinson, Wisconsin.
Related Topics: