Technology Gains Boost Boiler Energy Efficiency
Boiler technology has advanced greatly over the last 20 years, offering FMs much more efficient options.
Designing new buildings to minimize energy consumption is now the norm, and has even become mandatory in some jurisdictions. Future tenants and building owners now often consider low energy consumption design as a way to reduce operating costs and also green up their image. Recent innovations in boiler and domestic hot water heater design offer more sophisticated appliances to use in the quest to squeeze more energy from existing resources, but it is critical to understand how to best utilize this new equipment. The design of new buildings presents the opportunity to evaluate the structure holistically, integrating space heating and domestic hot water heating in a way that can take full advantage of advanced heating technology.
Lowest operating costs
The combustion technology used in fossil-fuel-burning boilers and water heaters has advanced about as far as it can practically go. Lowered water temperatures in hydronic space heating systems can also result in broader choices for heating equipment. At the most basic level, boilers and domestic hot water appliances are simply machines designed to convert energy into hot water; the rest of the system delivers the heat. The current choices for lowest operating costs are natural gas boilers and domestic hot water heaters that operate at temperatures cool enough to promote condensation of their waste flue gases. System water temperatures that promote condensation are generally considered to be a maximum of 140 F supply to the building and 120 F return to the boiler. Weather-responsive controls using an outdoor reset function can continually adjust water temperatures even lower during most of a heating season. Recovering the latent heat from condensation increases combustion efficiency above the non-condensing maximum of 89 percent. Condensing equipment with ratings of 92 percent and higher are now common in boiler sizes ranging from small residential to large commercial.
Condensing boilers
Condensing boilers have improved rapidly over the last 20 years and the technology is now considered mature. The most common pressure-vessel material is stainless steel of various alloys, solving some of the durability issues that plagued earlier designs. Acceptance and adoption of condensing boilers has been most rapid in the residential and light commercial hydronic heating market, utilizing boilers up to 400,000 Btuh. Many domestic manufacturers are producing outstanding products in this category.
The large commercial condensing boiler market has been slower to evolve, probably due to the misperception by many that there is little advantage to using condensing equipment to retrofit existing high temperature hydronic systems.
Developments in electronic controls have been the biggest contributor to the success of condensing boilers. Purpose-built embedded microprocessor controls pre-loaded with sophisticated software monitor a boiler’s functions and operate its key components in a coherent manner to enhance efficiency and reliability. The best of these controls can also interface with users and building management systems through dedicated on-board graphical user interfaces, BACnet, LonWorks, and other protocols to provide diagnostic information, fault alarms, operating information, and remote adjustment capabilities. Most of these boilers use premix, modulating burners, which provide very precise gas/air mixing throughout a wide turn-down range and require very little maintenance once they have been set up. The controls provide very accurate and stable water temperatures adjusted constantly through outdoor reset, based on multiple electronic temperature sensors. Many boiler controls now ship with multi-boiler staging software, pump output relays, alarm output relays, occupied/unoccupied scheduling software — truly plug and play and walk away.
Heating boilers of any fuel type operate more efficiently by being “right sized” for the heating load. Burner modulation to more closely match actual heating load has become quite sophisticated and 3:1 or 4:1 turn-down ratios are almost standard on today’s condensing boilers. Controls that modulate and stage multiple boilers complete the picture, providing boiler plant load matching for just about any load condition. Multiple boiler racking and manifold systems are offered by many boiler manufacturers to easily combine their standard off-the-shelf boilers in pre-engineered arrays. A popular option combines 400,000 Btuh light commercial modules in groups of up to 12 units, providing redundancy, ease of maintenance, easily sourced components, and an astonishing modulation range from as low as 80,000 Btuh up to 4.8 million.
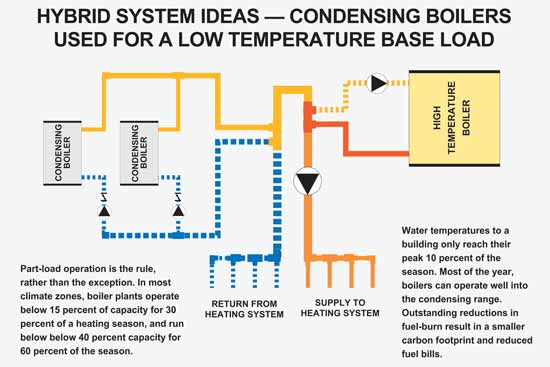
Related Topics: