Sustainable HVAC: Plan Early and Often
The keys to the greenest HVAC? Planning and budgeting in advance, and understanding higher first cost means lower long-term cost.
Buildings can do better. Global knowledge about how to condition enclosed spaces has advanced to a science in many respects, and today’s project teams can significantly improve performance, cut operating costs, and reduce energy use and carbon emissions. All it takes — for the most part — is better front-end planning.
The challenge that facility managers all confront today is that buildings consume roughly half of all energy used in the United States, according to the American Council for an Energy-Efficient Economy. Translating that to carbon load, about 40 percent of carbon dioxide emissions are due to operations — including heating and cooling — and about 8 percent from manufacturing, transport and construction, says the Environmental and Energy Study Institute. Embodied carbon adds to the total.
HVAC systems are an ideal place to start reducing carbon emissions and moving toward net-zero-energy operations. Writing in the Whole Building Design Guide, engineer Carl Ian Graham notes that, “The use of high performance HVAC equipment can result in considerable energy, emissions, and cost savings,” of up to 40 percent or more. Yet Graham ups the ante: “Whole building design,” he says, “can produce much greater savings” — up to 70 percent.
So what is the “whole-building design” idea that can unlock such superior performance? With that question in mind, here’s an approach that facility managers can follow to assure truly sustainable HVAC decisions.
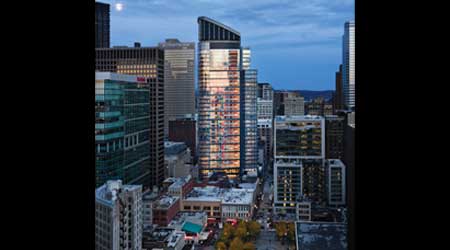
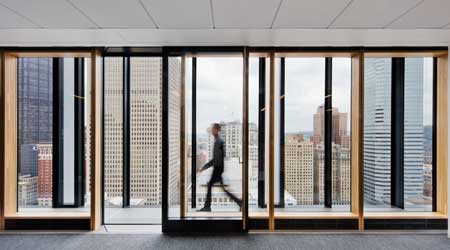
(At The Tower at PNC Plaza, the solar chimney in the core of the building pulls air across the office floors; the sloped, dark roof absorbs sunlight to drive the stack effect. The cavity between the double-skin facade insulates the building, facilitates natural ventilation, and removes excess heat. Occupants can open sliding doors to access the cavity or further enhance ventilation. Photo credits: Connie Zhou Photography, courtesy of Gensler)
Develop a case for smarter HVAC investment
Step one in achieving sustainable HVAC design is organizational buy-in. While facility managers can easily sell lower first costs and operating costs to upper management, sustainable HVAC design requires an integrated approach and a new look at many assumptions held by an organization’s leaders. For example, the building’s orientation and window locations have a powerful influence on HVAC needs. Will it be possible to diverge from a long-held aesthetic to make new buildings more sustainable?
Facility managers can help answer the question. Sustainable HVAC designs provide more people-centered designs that ensure happier, more productive, and more comfortable occupants, according to the U.S. General Services Administration. HVAC designs that target specific user types and specific facility operations tend to be more effective, too. Plus, sustainable HVAC design gives institutions and corporations a chance to eliminate unwanted fuels and energy sources and to reduce their overall carbon footprint.
Kill the cost myth
Most facility managers recall at least one time when a building design was handed over, and an HVAC system had to be fitted to that design. Instead of design analytics, many have witnessed design guesstimating. And without good front-end planning and effective modeling, making the HVAC system highly sustainable would probably cost a lot. It would take premium systems and possibly add-ons such as solar water heating or geothermal wells to achieve high efficiencies and low carbon emissions.
Yet with proper pre-planning, comprehensive modeling, and a commitment to an integrated process, there doesn’t have to be a cost premium for sustainable HVAC. In fact, the facility manager should save money. Integrated design means lower costs for early shared decisions that are made. However, it does require a disciplined commitment to a more effective front-end. And the payoff is predictably big, including:
• Capital costs are reduced with better massing and orientation, and need for fewer active systems.
• Reduced oversizing of systems cuts costs for design, materials, and operations.
• Increased opportunities to design to shave peak loads also bring first costs down by rightsizing systems and components.
It only stands to reason: The greenest HVAC solution will have the lowest sizes and loads possible and the fewest moving parts. Doesn’t that also sound like the most cost-effective HVAC solution, too?
Related Topics: