Portable Cooling: Tips for Renting Equipment
Rental-equipment options cover the spectrum, from portable coolers to trailer-mounted units that replace the entire primary cooling system during a renovation project or act as supplemental or standby emergency cooling. Renting is an excellent way for managers to check if a particular unit is sized properly and includes the right accessories before committing to a purchase.
The planning process begins by answering the question, "What is the cooling objective?" The next step is to determine the cooling load and alternatives for cooling. Managers want to get a unit that will do a satisfactory job of cooling efficiently. This requires careful, accurate calculation of the cooling load, and the proper selection of efficient cooling equipment.
Once a manager has determined the proper size for the unit, they can move on to other specifications, including:
- temporary ducting for supply and exhaust air
- power cord, plug configuration, and matching receptacle configuration
- breaker amps sufficient to carry the load
- dehumidification water drain
- on/off timer for automatically switching loads in unstaffed areas
- the unit's weight
- its space requirements
- generator requirements to provide emergency power.
In addition to these specifications, managers also should compare the seasonal energy efficiency rating (SEER) for each equipment option. SEER is the ratio of the Btu output to the watt-hours input, or Btu/watt-hour. The higher the rating, the lower the cost.
With this rating, energy use and electricity rate, managers can estimate the unit's annual energy cost. To do this, divide the cooling-unit capacity in Btu by the SEER. Multiply that total by the cooling-load duration in thousands of hours per year, and multiply that result by the electricity cost in dollars per kilowatt-hour.
For example, if the Btu capacity of a server cooler is 36,000 and its SEER is 10, and if the cooling load in thousands of hours per year is 8 and the electric cost is $0.08, the annual cost is 36,000 divided by 10, multiplied by 6, multiplied by $.08, or $2,304. If the SEER is 12, annual cost is $1,920, which means a savings of $384 per year by selecting the more energy-efficient unit.
The best planning will not be good enough if the equipment does not arrive in a timely manner with all necessary accessories. In weighing rental options, managers need to ask about time-sensitive delivery guarantees to ensure the unit will arrive when the facility needs it the most.
Thomas A. Westerkamp is a maintenance and engineering management consultant and president of the work management division of Westerkamp Group LLC.
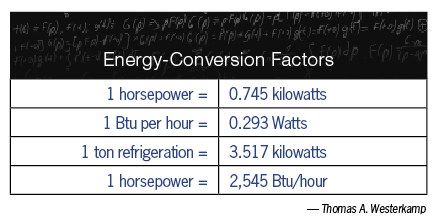
Related Topics: