High-Performance HVAC Achieves Optimal Efficiency
Part 2 of a 2-part article on the high-performance attributes of 350 Mission in San Francisco.
The following design parameters were used in selecting the 350 Mission UFAD components for optimal efficiency.
A low-pressure, low-velocity UFAD system. At 350 Mission, the floor-by-floor units were selected for 0.3 inches water guage (in-wg) external static pressure, compared to 0.75 to 1.0 in-wg in a typical floor-by-floor unit, decreasing fan motor horsepower requirements. (Inches water gauge is a measure of static pressure.)
The floor-by-floor units were selected in a down-flow configuration with the mechanical room at each floor acting as a return air plenum, thereby saving on both space and ductwork. Units were selected without heating coils to reduce pressure drop (all heat is provided at the terminal fan-powered boxes).
Variable flow air-handling units. Variable frequency drives were provided for all of the floor-by-floor air-handling units to conserve energy by reducing the speed of the fan motor when the floor requires less than full cooling.
This strategy also allows the pressure of the underfloor to be maintained at a constant value (approximately 0.05 to 0.07 in-wg) as floor diffusers are opened or closed and as the perimeter fan-powered boxes turn on and off.
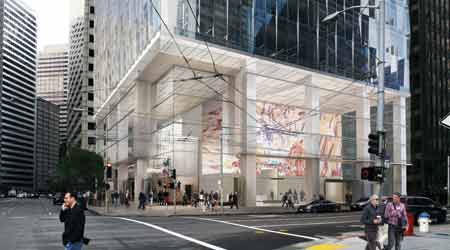
Caption: In the lobby of 350 Mission, located in San Francisco’s South of Market district, a real-time digital video canvas displays changing artwork. Photo credit: © Skidmore, Owings & Merrill LLP | AJSNY, 2016. All rights reserved.
Air-side economizer for the floor-by-floor units. Thanks to San Francisco’s mild climate, air-side economizers normally can be used much of the year. This reduces energy consumption for cooling, while the increased ventilation rate improves IAQ. All units were selected to provide up to 100 percent outside air to the floor.
Demand-control ventilation. Demand-control ventilation is a two-fold strategy to conserve energy and improve IAQ. A carbon dioxide sensor mounted in the breathing zone of the space continuously monitors the carbon dioxide level. If the concentration is low (indicating an unoccupied or lightly occupied room), airflow to the room is lowered to conserve energy. If the concentration is high (indicating a densely occupied room), the airflow is increased to maintain IAQ. The design provides carbon dioxide sensors for all densely occupied spaces at the space level and for the air-handling units at the system level.
High-efficiency chillers. Compared with a minimally code-compliant chiller, which has a full-load efficiency of approximately 0.57 kW/ton, the high-efficiency chillers selected for 350 Mission have an efficiency of 0.47 kW/ton. At full-load condition, the 350 Mission chillers are around 18 percent more efficient than the baseline chillers required by Title 24.
Variable-primary chilled water pumping versus primary-secondary pumping. At 350 Mission, variable primary pumping uses variable frequency drives on the main chilled water pumps to maintain minimum flow on the chillers and adjust the supply to the building demand, rather than providing a separate set of pumps and additional piping to maintain the minimum flow. This saves on both energy and material cost.
High-efficiency condensing boilers. The boilers provide a 92 percent annual fuel utilization efficiency (AFUE), compared with the 82 percent AFUE of standard boilers, as a result of the lower operating temperatures of condenser boilers. This building operates at water temperatures of 130 F supply and 100 F return, whereas standard-efficiency boilers operate at water temperatures on the order of 180 F supply and 140 F return.
A side-core fan room tower maximizes leasable space. Given the large volume of outside air used to cool and ventilate 350 Mission, the engineering team weighed the alternatives of moving air vertically from the top or bottom versus floor by floor. Given the relatively small building footprint and the owner’s requirement for an open floor plan and maximum leasable space, a central air shaft was undesirable.
Because one side of the building is about 25 feet from its neighbor, the team developed a side-core fan room adjacent to the facade, enabling fresh air intake and exhaust through louvers on a floor-by-floor basis. The team worked with the architects to develop a design solution that is not only mechanically functional, but elegant.
The HVAC system affected other building components as well. In particular, as building glazing has a significant impact on the operation of the mechanical system, the design team specified a glazing system that optimizes the aesthetics of the building exterior, natural light penetration into interior spaces, occupant comfort, and energy performance. The high-performance curtain wall comprises insulated glass units, which reduce solar gain.
While the mechanical design added to the capital cost of the building, it is a significant contributor to achieving the owner’s overall goals for efficiency, sustainability, and quality of tenant spaces — in particular, LEED Platinum certification, which was awarded in January 2016. Indeed, from its inception, 350 Mission has been a building with a singular goal: to achieve the highest level of environmental, social, cultural, and economic sustainability.
Saied A. Nazeri, PE, CPD, LEED AP BD+C, is senior vice president of the WSP | Parsons Brinckerhoff San Francisco office. Nazeri has over 25 years of experience in the design of HVAC systems for mixed-use, corporate, commercial, hospitality, government, retail, and data center projects.
Lindsay Marion is an associate with WSP | Parsons Brinckerhoff in San Francisco.
Skidmore, Owings & Merrill was the design architect and structural engineer on 350 Mission. WSP | Parsons Brinckerhoff provided professional mechanical, electrical, plumbing, fire protection, telecommunications, and security design services for the base building on the project, as well as the tenant fit-out of the office floors and lobby, and sustainable design services.
Email comments to edward.sullivan@tradepress.com.
Related Topics: