4 Steps to Selecting High-Performance HVAC
High-performance HVAC really means matching the right equipment to the needs of the project. Here's how to get that done.
High-performance design starts with the premise that each project is unique and demands a personalized analysis and approach. In order to determine the attributes of a high-performance HVAC system, the program, size, location, operations, financial parameters, and other priorities or goals of the building owner must be clearly researched and defined. There is no single type of high-performance HVAC system or systems per building type. To select a high-performance HVAC system, it is necessary to gather and present data that allows the building owner to select the most optimal HVAC system for the project. A key tool in that process is an HVAC system selection matrix. The matrix can organize and easily communicate all the gathered information. 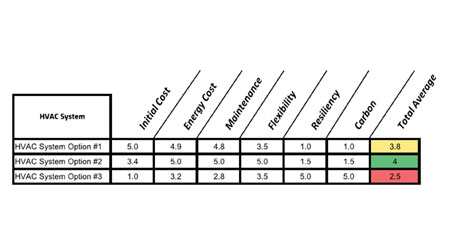
To create the HVAC system selection matrix, there are four main phases for development.
1. Gather information
The first phase of the process is to clearly define the project parameters. At this stage, the comparison factors for the matrix are defined based on priorities or determining factors. Some example comparison factors: initial cost, operating cost, maintenance cost, maintenance requirements, acoustics, redundancy, equipment space, distribution requirements, energy efficiency, occupant comfort, etc.
The HVAC selection process should always start with the project stakeholders, who should make clear the facility’s specific or desired goals. The measurable expectations for the project should be identified, and any critical success factors defined. Are there any project- or building-specific goals that might exceed current code or standard of design? Are there quantifiable sustainable and energy efficiency goals? For example, will the building owner seek any voluntary or mandatory certification programs such as LEED or Green Globes? Does the building owner have a target for an overall energy use intensity (EUI, kBtu/sf/yr) or for a percentage energy use reduction? Though all goals should be identified, they should also be categorized as “required” and “nice to have,” to understand their priority for later comparison.
Next, review and document the program requirements with the building owner and project design team. It’s essential to understand the temperature and humidity conditions for the general building and define any special space conditioning, ventilation, or filtration space needs based on critical space types. Find out whether there will be any special pressurization requirements for spaces such as isolation rooms, kitchens, laboratories, etc. The project team should discuss whether the mechanical system will be needed as part of the smoke control system. This is the time to review the specific redundancy requirements for the project and consider hazard vulnerability analysis, including uninterruptible HVAC service above and beyond code minimum for all or part of the facility. The owner should also identify the specific acoustic requirements for the various programs within the building.
Any project has constraints, and these need to be made clear at the outset. Financial and physical constraints need to be understood, as well as how they could limit available HVAC system options or prevent the project from achieving any goals that were previously identified. Prior to design, the allotted construction and mechanical costs for the project should be established. The early programming and schematic phase of design can give an indication as to the type and complexity of the budgeted HVAC system. More important, the mechanical costs may identify a disconnect between the HVAC scope and budget. Spatial limitations of the proposed or existing building also need to be understood and determined. The size of the mechanical rooms, the method of vertical distribution, the floor-to-floor heights, the desired architectural ceiling heights, and even the type of structure will all affect the HVAC design and may very well eliminate some system options.
During the information-gathering phase, the facility manager and facility staff play a critical role: explaining the wants, desires, and expectations of the personnel who will be operating and maintaining the HVAC system. Since the building owners’ priorities do not always align with the priorities of the facility staff, obvious disparities need to be identified and resolved prior to design in order to satisfy all parties. Determine what is important to the staff regarding the HVAC design. Preferred basis-of-design equipment manufacturers, requirements for equipment accessibility, scheduled maintenance, historic reliability, controllability, system complexity, ability for measurement and verification, and system equipment size — all these can influence the selection of the HVAC system.
2. Identify options
Based on the information identified during the information-gathering phase, requests from the building owner and facility manager, and the engineer’s design judgment, the HVAC system options to compare as part of the matrix can be selected.
To determine HVAC options, common program areas should be grouped into building areas with common HVAC requirements. Identify feasible HVAC systems that consider project goals, requirements, constraints, and expectations. All possible systems should be considered to determine which ones are most applicable and best suited for evaluation. Building owners or facility managers may have HVAC system types they have interest in and should request them to be considered as part of the study and selection matrix.
3. Rate the options
Analyzing and researching the comparative factors established in phase 1 can provide a concrete basis for comparing HVAC system options. Assign numerical values based on how well each option will achieve the goals for the project. Each option should be graded from best to worst (e.g., 5.0 to 1.0, with 5.0 being best). If a goal can be quantified in terms such as dollars, the graded values can be clearly assessed based on the best and worst options available. When a goal is more subjective — such as ease of control — and therefore a bit harder to decipher, the building owner, facility staff, and potential users play key roles in defining factors to grade each option.
The detailed steps below will create the analysis and research required to develop the differentiator rankings for the selected project parameters:
• Creating an energy model of the project and analyzing each HVAC system option. This provides comparative analysis for energy, energy cost, and carbon reduction savings for each option being considered.
• Preparing estimates of initial cost and annual maintenance costs for each HVAC system option, using past construction and operations and maintenance data. This can provide a comparative analysis for energy consumption, energy cost, and carbon reduction savings for each option.
• Performing a life-cycle cost analysis on the selected systems — including factors such as first cost, annual energy use, yearly maintenance, equipment lifespan, and replacement costs. This helps to evaluate and quantify the performance of each system over a desired time period (typically 30 years).
To give validity to the ratings, a narrative should be developed for each factor, defining what the grading criteria was for each, how it was developed, and how numerical grading values were assigned to each system option.
4. Evaluate data
Before a final version of the matrix is published, the owner and project design team need to review all inputs, analysis/research, and assigned grading values to verify accuracy. All process participants should be present and all parties should fully understand the results so that at the conclusion of the review, there is a clear agreement and path forward regarding the HVAC systems to be designed for the facility.
There are many challenges related to selecting a high-performance HVAC system. The process goes well beyond that typically used to select HVAC equipment. The high-performance design approach, including the system-selection matrix, considers all perspectives that will either affect or be affected by the design and operation of the HVAC system and in doing so provides for the optimal mechanical design solution.
James Newman (james.newman@rmf.com), division manager, RMF Engineering, specializes in high performance building design and operation, to achieve integrated sustainable design efforts using energy, water, and carbon analysis along with sustainable design methods to create optimal building and prime occupant experience.
Related Topics: