How To Calculate Life-Cycle Costs and Justify Energy Efficient HVAC Upgrades
First of a three-part article on how determining long-term costs can make energy efficiency more attractive to upper managers.
When top management wants to postpone replacement of HVAC equipment, the facility department may be asked to get “one more year” out of the existing equipment. Worse, this request may be repeated the next year, and again in years after that.
While maximizing the useful life of existing equipment is typically the most financially prudent option, serious issues can arise when the equipment ultimately fails. A run to failure approach is not necessarily a problem. Any piece of equipment, even critical equipment such as computer room air conditioning, can be run to failure as long as adequate backups systems are in place to mitigate the risk to operations, but this typically means completely redundant systems. In comfort cooling systems, there typically are no such back-ups in place. In this situation, running to fail is only a problem if the failure of the equipment will cause a monetary loss. This loss could be of revenue, loss of time, loss of production, or increased cost associated with emergency replacement, repairs, etc.
You may have heard of the project management triangle, which can be succinctly put as “fast, good, and cheap: pick any two.” When planning for replacement of HVAC equipment that is still operating, a facility manager has the luxury of obtaining competitive bids from multiple contractors without the pressing need to immediately replace failed equipment. But when there is an immediate need for equipment replacement, all consideration for energy efficiency is typically abandoned in favor of whatever can be installed most expediently. Any item that may have a longer lead time to procure, as high efficiency HVAC equipment typically does, would understandably be disregarded in favor of what is available right now. This is quite often not in the best interest of the organization in terms of ongoing operating costs over the service life of the equipment.
Determining life-cycle costs
Plenty of buildings have aging HVAC equipment that is near or past the end of its estimated useful life. In many of these cases, the facility manager might want to replace the equipment with something more energy efficient. High-efficiency equipment usually comes with a higher initial price tag than standard efficiency equipment. It may also come with additional levels of complexity to adequately maintain its higher efficiency. What analysis can a facility manager use to properly evaluate higher efficiency equipment? There are several ways to evaluate equipment replacement options.
Probably the most used and widely known type of analysis for equipment replacement or upgrade is the simple payback period. The simple payback period is the amount of time required in operation before the project has paid for itself via energy savings, and is typically provided in years. For example, a $10,000 project with an estimated annual savings of $1,000 per year has a simple payback period of 10 years.
The difficulty with simple payback (as with any financial analysis) is obtaining an accurate estimate for the projected annual savings. Project costs are typically known from the bids to perform the work, but projected savings require an understanding of how the current system is operating, its efficiency, and utility costs. What’s more, simple payback fails to account for other costs that may occur, especially maintenance and repair costs, and also fails to account for estimated life span and potential finance costs.
A simple payback analysis typically works for smaller equipment. For projects with sizable capital costs, a facility manager should perform an estimated life-cycle cost analysis in order to truly speak the language of finance. A life-cycle cost analysis will include upfront costs, operating costs, maintenance costs, special costs, and end of life disposal costs. (See worksheet at the bottom of this page.)
Upfront costs include the initial equipment purchase and all design and installation costs. Chart the operating costs over the equipment’s expected life span (which should include the annual utility and maintenance costs times the number of years the equipment is planned to be in operation). Special attention should be paid to maintenance costs. Some years may require major maintenance and some years only minor scheduled maintenance.
Sometimes facility managers will try to predict future utility, labor, and finance costs. As Yogi Berra famously said, “It’s tough to make predictions, especially about the future.” Costs will fluctuate, and there’s no way to know by how much or in what direction. Therefore, for simplicity, the best route is to use known current costs of utility, labor, material, money, etc. for the estimated life-cycle cost.
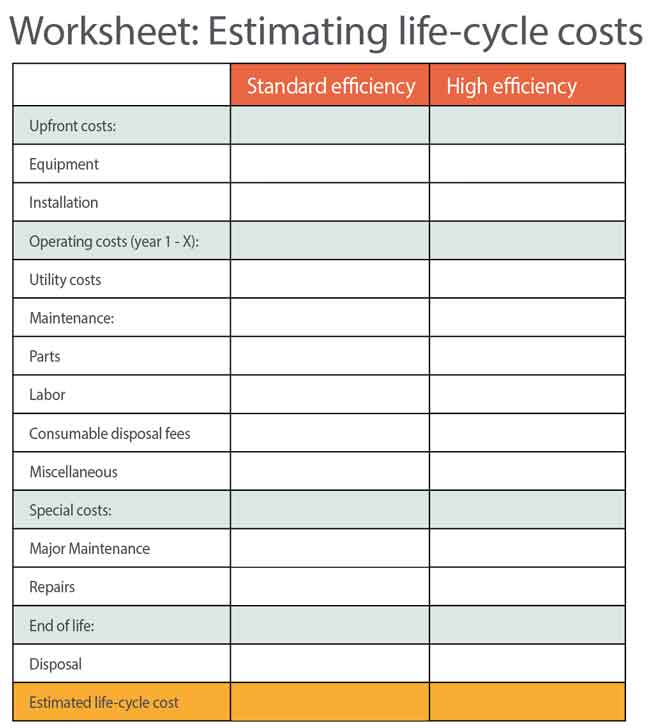
Related Topics: