view all Case Studies
Boiler Upgrade Produces Bottom-Line Savings
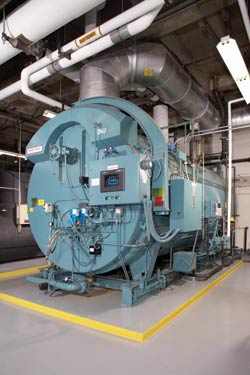
The 500 physicians of Crittenton Hospital Medical Center in Rochester, Mich., work with cutting-edge technology every day. For a long time, the same could not be said for maintenance and engineering managers inside the medical center. But a recent upgrade to the facility’s HVAC system has improved the medical center’s energy efficiency and its bottom line.
March 24, 2009 -
HVAC
The 500 physicians of Crittenton Hospital Medical Center in Rochester, Mich., work with cutting-edge technology every day. For a long time, the same could not be said for maintenance and engineering managers inside the medical center.
But a recent upgrade to the facility’s HVAC system has improved the medical center’s energy efficiency and its bottom line. The four boilers used for heating, humidification, and sterilization at the 290-bed facility were installed in 1967. The old gas-fired, watertube boilers were wasting energy and money, achieving only 75 percent efficiency at the highest firing rate.
Recognizing the need to invest in more efficient equipment, facility managers at Crittenton replaced its four older boilers with three gas-fired, firetube boilers from Cleaver-Brooks. Firetube boilers are efficient, compact, easier to clean and well suited for space heating in commercial and institutional applications.
Among the biggest improvements is that the new boilers use a high-efficiency, low nitrogen-oxide (NOx) burner. The burner’s fuel-gas-delivery design ensures optimal use with the combustion-chamber configuration. By combining the burner with other advanced technology, technicians have reduced Crittenton’s NOx emissions to less than 60 parts per million.
Another significant advancement was a new de-aerator. Facilities use a de-aerator to extend a boiler’s life by removing excess oxygen and carbon dioxide from a boiler’s water supply, thereby preventing system corrosion. Meanwhile, technicians also upgraded boiler controls to a fully integrated, programmable-logic-controller (PLC)-based boiler/burner management system with logic-based ancillary devices and functions.
The new controls include parallel-position actuators for fuel and air, which also help improve energy efficiency. By incorporating parallel positioning, boilers can operate at lower oxygen levels and, by doing so, use less energy. This component will save $10,000-$50,000 in fuel annually for Crittenton.
The PLC-based control’s variable-speed drive is another energy-saving element. This drive allows the boiler’s motor to operate only at its required speed, rather than a constant 3,600 revolutions per minute, which is the rate at which a typical boiler motor runs. This speed variance eliminates unnecessary energy use, saving the hospital about $3,300 a year.
With the new boilers and accessories, Crittenton increased its efficiency rate to 85 percent across all firing ranges. Crittenton’s managers are enjoying the high-performance equipment and closely monitoring the energy savings. Overall, they project a 20 percent reduction in gas consumption.
Next
Read next on FacilitiesNet