10 Keys to Monitoring-Based Commissioning Success
To cut out energy waste and keep a building optimized, follow these 10 best practices to continuously monitor and commission your building.
By Chris Wilson and Jim Vallort
Building owners and facility manager face myriad decisions when it comes to optimizing building efficiency. Grand, capital projects loom large, but it’s the low-hanging fruit that often results in the greatest payback over time. With all the technologies available to building owners and facility managers, improving energy efficiency should be a simple task.
All evidence is to the contrary, however. In fact, the Lawrence Berkeley National Laboratory (LBNL) estimates that anywhere between 5 and 30 percent of a building’s energy use is wasted due to faults and errors in operations. These are not difficult to fix when facilities personnel can detect them in real time. That’s where monitoring-based commissioning comes in.
Monitoring-based commissioning is a service and proactive, preventive maintenance tool that continuously improves building operations over time. Leveraging automated fault detection and diagnostics software, which provides actionable information on building faults and opportunities for continued systems optimization in real-time, monitoring-based commissioning has been proven to:
• Reduce building energy consumption and cost, including operations and maintenance. Operational costs are typically reduced by three to five percent annually when the facilities/operations team is able to focus on more pressing issues.
• Improve occupant comfort. HVAC-related occupancy complaints can be reduced by as much as 40 percent.
• Prolong mechanical equipment life by implementing low-cost operational improvements.
A building automation system isn’t enough. The BAS controls the building’s equipment to satisfy given parameters. These may or may not take into consideration an equipment’s optimized state. Automated fault detection and diagnostics software integrates into the BAS and identifies anomalies in the operation of building equipment that aren’t detected by the BAS. A “smart” alarming tool, fault detection and diagnostics software will pinpoint faults and provide suggested resolutions the moment they occur.
Getting started with monitoring-based commissioning requires three things: an engaged building operations team, a look into the local utility program to help offset first costs, and an understanding of the building’s annual energy spend. Here are 10 best practices to implementing monitoring-based commissioning, including considerations for choosing the right automated fault detection and diagnostics software for any facility.
1. Engage the building operations team early. The facility manager, asset manager, owner, and operations team are the ultimate stakeholders of monitoring-based commissioning adoption. Because the end goal is to train the operations team to facilitate monitoring-based commissioning long-term, they must be committed to taking action on identified issues.
2. Look into incentive programs. Federal funds, state grants, and utility incentives may be available to offset the first costs of monitoring-based commissioning. Where formal programs don’t exist, municipalities and utilities are usually willing to entertain a pilot program when you work with an approved service provider.
3. Understand the facility’s annual energy spend. The monitoring-based commissioning service provider will need the last 36 months of utility data to create an accurate baseline of building energy consumption. They’ll look at both consumption and demand costs as well as total energy spend.
4. Choose automated FDD software that is capable of integrating with your BAS. A vast number of automated FDD providers offer both open protocol and platform-specific products. BAS systems speak dozens of proprietary protocols and languages and have their own way of communicating. Extracting the data can be difficult for older, legacy systems. Understand the protocol your BAS uses and determine how to accomplish fault detection and diagnostics integration successfully. Get pricing from multiple vendors.
5. Solutions that feature automated data mapping can reduce first costs significantly. With thousands of data points across a facility, manually integrating each point into a new software system can be cumbersome and inflate first costs. It’s important to gain an understanding of how the data sets are named within the BAS and if they’ll translate well when integrating. Although automatic data mapping significantly reduces time with integration, it can still be cumbersome if the data sets aren’t properly labeled by the BAS provider.
6. Customized automated fault detection and diagnostics software has greater benefits. Some automated fault detection and diagnostics software solutions have standard black box rule sets. Yet the biggest benefit comes from the ability to customize the rule definitions. With customizable software, engineers will review the building’s designed sequence of operations and create associated rules. When something changes and equipment is operating out of the rule parameters, a fault will be generated. When the sequence of operations changes, the rule needs to change as well. For example, if lease negotiations change operating set points — for example, the lease says the building operates at 71 degrees F to 73 degrees F year-round, and the lease agreement changes those set points to 73 degrees F to 75 degrees F — the fault rules must change accordingly.
7. Consider reporting functionality needs. Some automated fault detection and diagnostics software will provide the ability to customize reports, while others will only offer standard reports. Consider who within the organization needs to see the data collected and faults generated when creating key performance indicators. The asset manager will more than likely want to see financial impact whereas the operations manager may want to see comfortability reports. Ask: How often do they need to see it? How is the information delivered to the end user? What level of customization is desired? The answer to these questions will inform how customized the reporting features of the software needs to be.
8. Prioritize the most important operations and energy efficiency items. Building staff needs to see actionable data and manage it accordingly. What is available will depend on the flexibility of the automated fault detection and diagnostics tool. If you care most about comfort, for example, then that can be set as a critical rule. Some software options will allow prioritization, while others will feature automated prioritization without taking user input into consideration.
9. Keep IT systems security a top priority. Make sure to partner with software vendors that will work closely within your IT systems parameters and keep security a top priority. The automated fault detection and diagnostics software will be tied to the BAS network. Some BAS networks are tied to the company’s network, while others are separate. Companies in tune with current cyber risks will have a separate network for their BAS but still have stringent requirements for remotely accessing these systems.
10. Consider limiting access to your building’s data. Typically, both the software provider and the building owner/operator maintain access to the automated fault detection and diagnostics data. The building owner needs to understand this.
Real world example
The Shirley Ryan Ability Lab, a 1.2 million-square-foot rehabilitation research hospital in Chicago, is one of the first in the country to demonstrate success when MBCx is applied to new construction. Just six months after the facility was built, Shirley Ryan began an 18-month project to achieve the following: increased efficiency of MEP operations; enhanced occupant comfort; reduced operations and maintenance costs; and reduced energy demand and cost.
(Photo credit: Design: HDR|Gensler; photography: copyright 2017 Michael Moran)
Being a newly construed building made this project a challenge. Automated fault detection and diagnostics software was customized to identify potential energy and operational improvements, implementation oversight, and measurement and verification required.
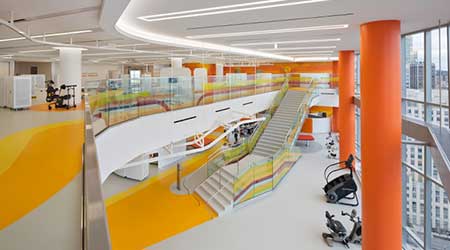
(Photo credit: Design: HDR|Gensler; photography: copyright 2017 Michael Moran)
The result was a 6 percent annual energy savings, including: 1,253,621 kWh of electricity, 101,830 therms of natural gas, and $116,573 in energy costs. The project paid for itself in about six months. Shirley Ryan’s MBCx for new construction pilot program was a first for the local ComEd Energy Efficiency Program. The resulting efficiencies demonstrated that there is potential to improve operations in a new building.
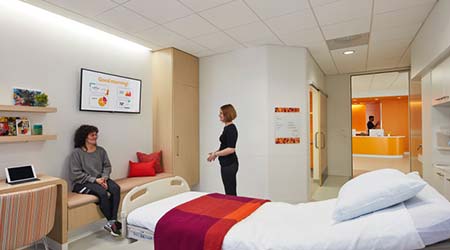
(Photo credit: Design: HDR|Gensler; photography: copyright 2017 Tom Harris)
Next step in progress
With its ability to leverage automated fault detection and diagnostics software and smart analytics, monitoring-based commissioning is key to getting ahead of operational errors and faults through detection, a function that ultimately leads to a reduction in building energy consumption and cost, an improvement in occupant comfort, and prolonged mechanical equipment life.
As the natural next step in a building’s progress toward ‘intelligence,’ monitoring-based commissioning can pick the low hanging fruit continually that will keep your building in an optimal state for as long as possible.
Chris Wilson, PE, is operations director, Energy + Eco, Environmental Systems Design, Inc., Chicago.
Jim Vallort (jvallort@esdglobal.com), CEM, LEED AP, and ASHRAE Fellow, is managing director of the firm.
Related Topics: