Energy and computational fluid dynamics (CFD) modeling of the National Oceanic and Atmospheric Administration Daniel K. Inouye Regional Center in Pearl Harbor, Hawaii, showed how a passive cooling system would provide substantial operational and first-cost savings and enabled the use of other sustainable strategies.Photo: (c) Alan Karchmer / Courtesy of HOK
How GSA Goes Green: 3 Best Practices
Integrated design, energy modeling, and programming for long-term operational savings are how GSA has gone green throughout its building stock.
1. Leveraging integrated design
With integrated design, all stakeholders — building owner and operator, architect, MEP engineer, structural engineer, contractor, preconstruction services consultant, cost estimator, and other consultants — collaborate early and often to understand how building systems link to one another and then use that knowledge to uncover efficiencies and tradeoffs. While this requires more planning on the front end, it often leads to free or passive solutions that reduce system loads and building costs. Integrated design might reveal, for example, how a slight modification to a building’s orientation could reduce solar heat gain and increase natural daylighting, resulting in less expensive HVAC and lighting components.
The DC Consolidated Forensic Lab provides a real-world example of how integrated design can lead to first-cost savings. The LEED Platinum building in Washington, D.C., came in 17 percent under budget with much of the savings due to sustainable design elements. Collaboration during the integrated design process resulted in outfitting the building with an active chilled beam system, heat shift chiller, enthalpy wheels, and glycol energy recovery loops that reduced the mechanical load of the building and the number of chillers that would have been required with a traditional HVAC system. Because chilled beams are a hydronic system that does not require as much plenum space as traditional air ducts, the design team also was able to reduce the floor-to-floor height of the building, which led to construction and material savings.
The integrated design process let the team know that the building operator wanted sustainable features that would reduce long-term energy use and costs. This knowledge led to the use of a dynamic glass louver wall along the building’s south facade. The glass louvers (featuring a 50 percent ceramic frit pattern) serve as a solar shield, automatically adjusting, opening, and closing depending on sun angle, wind, and barometric pressure. Unlike a true double-skin facade, the louvers — set three feet off the curtain wall — allow the airspace between the exterior wall and sunscreen to vent without impacting air pressurization requirements in the interior lab space while mitigating solar heat gain and glare along the south of the building.
2. Energy modeling
It’s important to set specific performance targets for energy use intensity and water use intensity from the very early stages of the project. This helps the team focus on what is most valuable to the building owner.
Energy modeling helps the design team understand long-term and short-term consumption costs. Adding this crucial component of integrated design often leads to additional savings and helps justify the costs of sustainability features.
Energy and computational fluid dynamics (CFD) modeling of the National Oceanic and Atmospheric Administration Daniel K. Inouye Regional Center in Pearl Harbor, Hawaii, showed how a passive cooling system would provide substantial operational and first-cost savings compared to other HVAC options. The novel cooling system pumps cold seawater from a 1,300-foot-deep well to the building’s chillers, where heat is rejected into the seawater, eliminating the need for traditional cooling towers. The seawater then flows into a series of chilled coils. This system takes advantage of the trade winds to drop chilled air passing over the coils into the building without using mechanical fans.
Savings from the cooling system allowed the design team to equip the LEED Gold project with additional sustainable design features such as increased daylighting. Small-scale mockups were used to test the size and spacing of daylight openings to provide even daylight levels across office work areas. As construction proceeded, full-scale mockups fine-tuned the initial daylight studies, ensuring that interior workplaces took advantage of the maximum amount of natural light while blocking direct sun exposure. Once in operation, the NOAA Inouye Regional Center achieved 33 percent annual energy savings compared to ASHRAE 90.1 standards, in addition to its first-cost neutral sustainable design.
Energy modeling isn’t just for building owners who care about sustainability or LEED certification. Energy modeling can often discover savings that far exceed the costs of setting up and running the energy simulation software.
3. Programming for efficiencies
High-performance buildings need to be efficient and durable with an eye toward long-term operational savings. It’s important to think about how people will use facilities and adapt them over time. Taking a detailed look at this projected usage can help teams design for efficiencies.
Procurement processes play a role in this. Performance outcomes, i.e. measured energy performance, often are included in contracts for design-build and public-private partnership projects. If the RFP requests a 30 percent energy savings, the bid might include a section showing what net zero energy use looks like as an alternative — without making the proposal any less cost competitive.
The design of the NASA Johnson Space Center Building 20 in Houston shows how using this planning strategy can both reduce costs and improve a building’s performance. In the RFP for the project, NASA specified it wanted a LEED Silver building of approximately 93,000 square feet. A review of how the building’s 520 employees would use the space made it possible to reduce the overall building size by 11 percent while still meeting the requirements of the agency’s occupants.
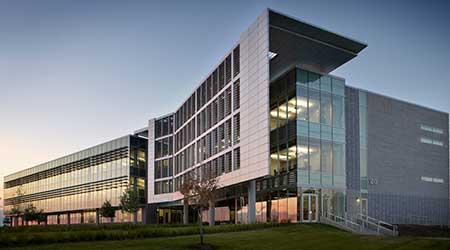
(NASA's Johnson Space Center Building. Photo: (c) Alan Karchmer / Courtesy of HOK)
Savings from the compact design made more of the project budget available for sustainability features — including exterior sunshading devices, advanced lighting controls, a building section optimized for daylighting and an underfloor air distribution system — that ultimately resulted in a building that used 57 percent less energy compared to ASHRAE 90.1 standards than a conventionally designed facility and that achieved LEED Platinum status within the budget.
Related Topics: