« Return to FMDAA entries

Johnson and Wales University, Providence, R.I.
CATEGORY: Personnel Management
Overview
Johnson and Wales University in Providence, R.I., recently underwent a leadership change in our Facilities Management Department which triggered major restructuring efforts aimed at fundamental improvements in how personnel performed daily tasks. Although we compare favorably to other university facilities maintenance organizations in terms of staffing and funding, with a footprint of almost 3 million square feet and more than 60 buildings, efficient labor management is crucial for success.
A new leadership structure was introduced resulting in many operational changes. A full analysis was conducted in order to identify current practices before an improvement path was plotted. The catalyst for our new course of action was the overall lack of direction within the maintenance program — decentralized practices, meager tracking mechanisms, rigid schedules, poor communication and a spotty preventive maintenance (PM) program — the five main areas we targeted for improvement.
Our scheduled work force operated within a typical 8-5 environment which limited accessibility, increased overtime and delayed response time for critical calls. A redistribution of labor resulted in prompt responses, less disruptive PM performance and a reduction of overtime by 20%. The department now has 24/7 coverage with the addition of a second shift and rotating on-call staff.
Services were performed by discipline rather than demand, therefore the work order distribution was unbalanced, creating overload for certain technicians and downtime for others. Cross training of employees was necessary to increase response times and improve efficiencies in a balanced approach.
- An active construction site doubled as a classroom for technical cross training. As a new academic center was being constructed on campus, regular training was held with technicians to examine the inner workings of mechanical, electrical and plumbing systems.
- International Facility Management Association (IFMA) courses were offered to operations managers and staff to improve their FM program knowledge.
- Regular meeting schedules were introduced in order to reinforce direction and empower employees.
The inability to track and analyze accurate data in order to develop key performance indicators (KPIs) presented the biggest challenge. Recognizing that data drives decisions the most dynamic cultural shift manifested as a disciplined program for data management was established. A computerized maintenance management system (CMMS) upgrade accommodated the necessity for documentation and expedited additional change management.
- Our robust CMMS facilitates data collection, tracking and analysis provides KPI intelligence which is now woven into every decision. In order to control and optimize a master data platform within an enterprise system an information director was hired and empowered to implement and monitor change.
- Control measures are now enabled requiring technicians to track time required for tasks.
- Production reports are generated daily.
- The work order system is the backbone of our PM execution.
- A customer service mechanism was implemented which allows the technician to communicate directly with the requester (via CMMS) and explain actions or relay overall status.
- Employees are embracing the new culture and have pride in their documented accomplishments.
Our staff was spending unnecessary time at the end of each day logging daily activities. An alternative which allowed them to instantly input completion data was implemented with the purchase of smart phones for each technician. They now receive and complete work orders efficiently. Travel time is reduced and work orders are closed in living time.
80% of purchases were processed through P-Cards with no oversight mechanism. With new direction and oversight that percentage dropped to 5 within the first year of the initiative. A central warehouse controls parts inventory and connects them to specified work orders.
Measured Success
Although it was messy at times, and there were moments of confusion during the transition resulting in lost productivity as we worked through new processes; the overall success of a structured centralized program has been notable. We now operate with a proactive methodology emphasizing preventive and predictive maintenance. Our work management process has yielded proven gains in productivity. Creating cross-functional skilled technicians has improved employee morale. By positioning resources closer to the work for logistical efficiencies we have reduced travel time and vehicle usage. Standard operating procedures and process flow charts have been utilized for training and maintaining purposes.0
We are currently staffed at a low APPA 3 level; however our performance is a solid mid-level APPA 2 which is our greatest measurement of success as we have proved we can truly do more with less in a structured environment. JWU has campuses in three other states and these same practices are being embraced in order to enhance their working environments, save money and improve efficiency.
Additional Information
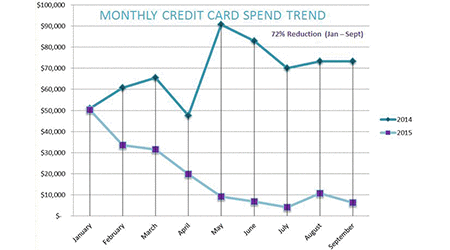
» View Material Purchasing - Cross Functional Process (PDF)
↑ Back to top