« Return to FMDAA entries

Unity Health Toronto, St. Michael's Hospital - Entry #1
Overview
The Engineering and Plant Services department is responsible for a variety of complex projects related to annual budgeting and capital planning processes for clinical engineering, maintenance and plant services, project engineering and the overall management of the operations facilities for Unity Health Toronto St. Michael’s Hospital (SMH), St. Joseph’s Healthcare, and Providence Healthcare. The team provides expertise in areas of quality improvement, creating a safe, functional, and sustainable environment for patients, staff, and visitors of the hospital.
One of the projects recently completed by the engineering and plant services department was to upgrade the existing pneumatic controls within 20 air-handling units (AHU) to electronic DDC controls in SMH. The AHU controls were beyond their usual service life and obsolete, resulting in expensive maintenance or difficulty in repairing and servicing the controls. As a result, the systems were not operating efficiently, threatening program delivery, and negatively impacting patient care. The new electronic controls will optimize efficiencies of operations and contribute to enhanced patient comfort.
For each fan system, all pneumatic actuators were replaced including mixed air damper, isolation damper, face and bypass damper, inlet vane actuator, preheat valve heating valve, cooling valve, humidifier valve, and reheat valve as required. The new actuators that were supplied for the AHU systems also have the capability to provide feedback signals for control status. By converting over to the electrical controls, the usage of air compressors are reduced, which in turn reduces the electricity usage.
In addition to the replacement of the pneumatic controls, the controllers were replaced with new BACnet controllers to align with the facility standard. The replacement of these controllers than enabled the upgrade of the ventilation control to variable frequency drive (VFD) controls on five of the AHUs. This allowed for better air flow control and significant energy savings. The existing vanes were locked at 100 percent in order to prevent any airflow interference. More accurate fan control resulted in electrical savings for the fan motors, as well as steam and chiller savings.
One of the most common challenges faced while working in an operational facility is maintaining operations while retrofitting or updating existing systems. The engineering team had to coordinate after-hours shutdowns for critical areas to ensure minimal impact and interruption to operations.
Funding is another major challenge. However, the team was able to utilize and secure the health infrastructure renewal fund (HIRF) to complete this project, resulting in both renewed Infrastructure and improved operational efficiency and quality. The retrofit was completed by migrating from the old, obsolete system to the upgraded system without rewiring or recommissioning the existing panel, providing an economical solution with less downtime. With the VFD installation, SMH qualified for the Save on Energy program, receiving an ongoing energy savings year after year post-installation. See the image below for an overview of the savings to-date post-retrofit. Air compressor savings post-retrofit was approximately 25 percent.
The engineering and plant services department continues to enable care and discovery within the organization, by being responsible for the operation and maintenance of the hospital’s physical facility, central plant, equipment, grounds, and life-safety system and by working hand in hand with key stakeholders, continuously improving and upgrading existing system and work flow process to improve our patient and healthcare system.
In-House Participants:
Katelyn Marie Poyntz P.Eng Manager, Project Engineering Engineering and Plant Services
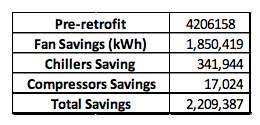
↑ Back to top