view all Case Studies
Medical Center Automates Maintenance Department
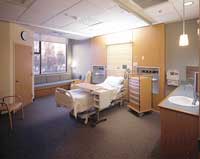
To ensure compassionate care occurs throughout a patient’s experience, St. Charles Medical Center must keep everything in order at all times, and this mandate applies to both of the medical center’s locations, in Bend and Redmond, Ore.
January 11, 2008 -
Software
To ensure compassionate care occurs throughout a patient’s experience, St. Charles Medical Center must keep everything in order at all times, and this mandate applies to both of the medical center’s locations, in Bend and Redmond, Ore.
The Bend location boasts more than 800,000 square feet and serves as the main hospital with 200 patient beds and 11 buildings. Redmond, located 25 miles away, has 150,000 square feet, seven buildings and 48 patient beds.
Ron Neet, director of facilities services, oversees the facilities operations and maintenance team that handles operation and maintenance issues on both campuses. He understands their critical role is delivering the best possible patient care for residents within the 32,000-square-mile area surrounding Bend and Redmond.
Keeping both campuses in compliance with the Joint Commission is no easy task, and it became more difficult for the medical center because of outdated processes. Staff manually tracked maintenance activities, primarily on paper. Equipment maintenance and work-order tracking was not automated, and record keeping was a chore.
To add to the compliance challenge, St. Charles embarked on a process to improve the quality of organizational and patient care. In late 1999, the hospital became one of only a few ISO 9000-compliant health care organizations in the nation.
To properly adhere to compliance issues, Neet and his department had to document preventive maintenance measures and actual work performed. Regulatory-compliance mandates drove the medical center to move from a manual maintenance process to one that is fully computerized. Neet already was familiar with the Benchmate maintenance software system – manufactured by Benchmate Systems, Inc. – so he procured the system and led the implementation effort. Neet and his staff converted equipment records, past maintenance work information and all other data on paper to the Benchmate system.
Staff determined preventive maintenance frequency and intervals during the transfer so they could be incorporated in the new system. By having this information assigned to specific equipment records, Benchmate now automatically produces preventive maintenance work orders for the medical center’s maintenance team.
“Taking care of patient-related needs is our primary focus,” Neet says. “Whether it’s a request to repair a broken shelf, unplug a toilet in a patient room, or to check on a problem with lighting or beds, we respond to those requests right away. The Benchmate system captures all data from initial request to work-order completion, which provides us excellent historical records on any piece of equipment or specific area of the facilities.”
Benchmate is the hub for all facility operations, testing and maintenance at both medical campuses. A centralized help desk serving both locations handles all work requests for repairs or service needs. Supervisors then review work requests, determine priorities and create work schedules within Benchmate. They also make technician assignments within the system.
More than 28 users access Benchmate routinely to respond to maintenance needs, perform scheduled work and close out work orders on completed jobs. The system issues 1,200-1,400 work orders each month. About 25 percent of those are considered emergency or urgent work orders and given the highest priority. Any work order directly related to patient care is always a top priority, with a standard response time of under 30 minutes.
“Benchmate is a very user-friendly system and has become the essential tool for our maintenance operations,” Neet says. “We rely heavily on the system for reporting and documentation used for regulatory compliance. It’s easy to pull information from the system to demonstrate compliance as required.”
Next
Read next on FacilitiesNet