Five Minutes With Audio & Video Home
fiveminuteswith
How General Motors maintenance manager identifies, prioritizes hundreds of projects
Darrell Rounds, the manager of maintenance and industrial cleaning for GM Global Facilities, discusses the challenges of identifying needs and setting maintenance priorities for a company with sites located all over the world.
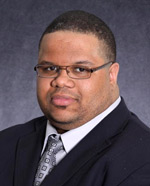
Darrell Rounds
Manager - Maintenance and Industrial Cleaning
GM Global Facilities
1. Describe the kinds of projects your department handles.
Our department handles the scope development and the prioritization of asset renewal and refurbishment projects for all infrastructure and building systems such as roofing, paving, HVAC, chillers, air compressors, wastewater treatment, power distribution, security systems, and fire protection, just to name a few.
2. Describe the process you go through to determine which projects get priority and, eventually, funding.
Some of the main factors in determining whether or not projects receive priority are health and safety, regulatory compliance, and impact to production. When you have such a variety of projects spread across many locations with so many variables, we thought it necessary to make the decision process objective. We developed a decision support system that assigns a numerical value to each project that's being considered for funding. This numerical value is comprised of factors such as safety, regulatory compliance, and impact to production which are weighted more heavily than other factors such as how the project ranks among other projects within that respective category (for example, ABC's roof vs. XYZ's roof), or how the facility manager ranked the projects among other projects at that particular site (for example, ABC's fire alarm system vs. ABC's parking lot paving project). Once each project is assigned a value, discussion takes place to see if the valuation was legitimate and the projects are ranked from 1 to N where N is the lowest priority project.
3. How many projects receive consideration for funding, and how many are ultimately selected during a budget period?
Globally, many asset categories. GM designs, manufactures and tests automotive vehicles, so you can imagine that there are multiple asset types besides facilities that require us to prioritize and balance funds as a company. For 2014, in North America, we had approximately 465 facilities projects submitted for consideration of which the top 100 priority projects will receive funding for execution.
4. What is the makeup of your team that determines projects that are selected?
Within Facilities, we have a site operations team that develops their initial project list based on site-specific health and safety issues, regulatory inputs, and asset condition. The lists from all the sites are compiled centrally by a coordinator, and reviewed by my core team of building systems subject-matter-experts. These experts review the projects and provide a higher-level site-to-site prioritization. They are some of the more experienced facilities professionals in our company, and they develop our project engineering packages as well as provide assistance with resolving some of our toughest technical problems.
5. What are your biggest challenges in the prioritizing process, with so many sites to consider?
The most obvious challenge is ensuring we have the right priorities and have transparent communications with the individual sites. We are all driven to do what is best for the company, so sometimes a site will have their project deferred to a following year in order take care of the priorities in the company portfolio. Our decision support system has been an important tool for us in the prioritization and communication process. Another challenge is our aging portfolio. Globally, we have buildings that were constructed as long ago as 1899. Here in North America we have buildings that are older than 90 years old. Aging infrastructure and integrating systems into these can be very challenging.
6. Upon a project's approval, what is the next step your department takes in the process?
Once a project is approved, we develop a formalized scope for the project, which is used to purchase design and construction services. Projects are executed locally by site Facilities personnel for small projects or centrally by our facilities project management team for larger projects.
Find more on this topic:
Maintenance & Operations, Facilities Management
posted: 11/4/2013