Advocate Good Shephard in Barrington, Ill., is one facility included in the $1.5 billion budget for construction and major renovations since 2009. Advocate Health Care
Standardization of FM Operations Brings Efficiencies
Second part of a three-part cover story profiling Advocate Health Care's Albert Manshum.
When Manshum was first tasked with evaluating the facilities organization at Advocate, variance was one of the biggest things that jumped out at him. “I was seeing all the disparities across the system in all areas,” he says. “It wasn’t just facilities. We had a pretty large variation.” Standardizing operations held a potential for significant savings.
“We standardized our approach across the system and some good things happened,” Manshum says. For example, before 2010 there were 87 different job descriptions within facilities, because they had been written around individual capabilities at each of the different sites. “It became impossible for us to train people, to get things done in a standardized way and create an onboarding training program, because every one was unique,” says Manshum. The job descriptions have been honed down to 17.
Another standardization effort has been doing away with overrides. All of the sites were retrocommissioned and now have a yearly facility operational checklist of 200 items to ensure systems are operating as they should. “It became a rallying cry in the culture,” Manshum says. “We’re going to go back in and make sure everything is working correctly. And once we get it working, the culture now is that I’m not going to enter an override.” The new philosophy: “When something goes wrong, figure out what it is.” He cites a situation at one facility, which had been designed to be particularly energy efficient. However, a forgotten override to accommodate an off-hours holiday party in the outpatient building wasn’t caught until a year later, to the tune of $145,000. Goodbye overrides.
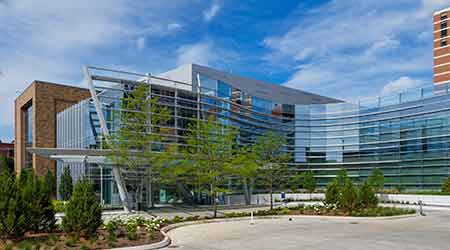
(Illinois Masonic Medical for Advanced Care in Chicago. Credit: Advocate Health Care.)
Successful standardization requires a lot of data. Starting with comparing and contrasting energy use throughout the system, other metrics have been developed for other areas, such as security and environmental services. By tracking and analyzing things like how many security-related calls are made at a site or how many of what kinds of incidents occur, Manshum plans to be able to better understand exactly how many public safety officers are needed. Increasing safety while at the same time increasing efficiency is the goal.
In facilities, perhaps particularly in healthcare facilities, there is a feeling that each is unique, with unique needs and constraints. In consolidating the operation at Advocate, Manshum freely admits that he didn’t have much interest in focusing on the idiosyncrasies. “I’ll be honest, and say I was a bit dismissive of that,” Manshum says. “We can normalize and compare our data and contrast the sites fairly.” That’s not to say that all of the facilities are the same. “Everybody has something that benefits them or hurts them a little bit, but it all washes out, if you will. We don’t tend to focus on those (differences.) We focus on the opportunities to standardize.”
Building the team
It’s not about whittling processes, systems, and services down to the bare bones in the name of efficiency and cost savings. In healthcare, patient satisfaction is directly tied to revenue. In addition, the critical role healthcare facilities play in positively impacting how patients heal is very close to Manshum’s heart. “In general, facilities people are not thought of in hospitals as major contributors, but they are,” he says.
Increasing employee recognition has been a big part of his strategy in creating positive change. “To really get the culture going, whenever somebody is doing well, we really promote it and celebrate it within the facilities department, to let them know that somebody is doing something,” says Manshum. “And that motivates everybody to do the same.”
That simple recognition of good work has spurred an attitude in the facilities team where they want to spot the problems before they’re even noticed. “Our facilities associates are out actively trying to find everything that’s wrong, so if they see a burned out light bulb or a leaky faucet, they’re trying to find it themselves and fix it before we ever get the call,” Manshum says. “We’ve seen a massive reduction in the number of service calls.”
Manshum has already achieved a lot at Advocate, but he’s not done pushing the needle. For example, after beating the 20 percent energy consumption savings goal in 2015, the new goal is another 20 percent by 2020. He has delivered $1 billion in capital projects to the system that are LEED certified, or are seeking certification, including the first LEED Gold Certified hospital in the Midwest. Chan says his marching orders are to continue to embark on providing facilities operations at a lower cost without compromising safety or quality. “That’s our task, that’s the charge we’ve been given from him,” Chan says.
Manshum thinks his team is equal to the challenge. “I have a very good team,” he says. “That’s the key to any larger organization. I’m only one person. All I can do in this role is help set overall strategy and assistance to our leaders to get the job done. Setting the culture, setting the strategy, and then working with a good team to implement it. We’re able to manage it. It’s not perfect. There’s room for improvement. I wouldn’t be here if there weren’t areas for improvement.”
Email comments and questions to naomi.millan@tradepress.com.
Related Topics: