Roundtable: Managers In Health Care And Education Discuss CMMS Challenges
By Dave Lubach, Associate Editor
OTHER PARTS OF THIS ARTICLEPt. 1: This Page
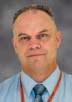
David Adcock,
Director of Facilities,
Riddle Memorial Hospital,
Media, Penn.
|
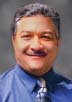
Frank Lucas,
Assistant Director of Work Management,
University of Nevada,
Las Vegas
|
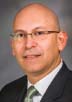
Oscar Rangel,
Property Manager,
MD Anderson Cancer Center,
University of Texas at Austin
|
Computerized maintenance management systems (CMMS) are the backbone of many maintenance and engineering departments. The role of CMMS will increase as managers embrace the need for more accurate, comprehensive data related to their facilities. In this roundtable, three managers discuss their strategies and challenges maximizing their departments' CMMS.
How long has your department had the CMMS you are using, and how satisfied are you with it?
ADCOCK: We've had our current version since about 2003, and we're very happy with it. We had a different version of a CMMS prior to this, and it wasn't as user-friendly as the current product we have. What I basically did was search out some new technology. The first thing I did before I purchased it was test drive it. It came with a sample database, and I fooled around with it for a couple of weeks to make sure it fit our needs. Once I did that and saw how easy it was to utilize, I purchased it, and implemented it for our facility.
LUCAS: We implemented it on March 21, 2002. The system has done everything we needed it to and then some. We've made extensive use of its features and functions and done some interfacing with other systems, like homegrown applications and custom electronic routines designed to share information. We manipulate financials with the CMMS, and it helps us do more with less while increasing data entry accuracy, so it's really played an integral role in our operation.
RANGEL: Our organization purchased a CMMS in 1998. The initial rollout of the software was not very good, which led to low satisfaction ratings and little or no use. Changes in management in 2006 led to a renewed effort to again roll out the software with much greater success and clearer standards to follow. Refinement of the standards has continued in earnest, leading to a more effective use of the CMMS.
What benefits has the department realized from using the CMMS?
ADCOCK: Probably one of the bigger things is it gives us improved control over of our assets throughout the building. We have better control over those assets. We also have an improved equipment management system, so we can set up tasking and issuing work orders and work tasks, (and) we can do (it) either as a scheduled work order or like a critical repair that is a priority-level work order we have to do right away. That was one of the improvements. One of the other benefits is, it gives us the ability to bundle together like assets. (For example), if you are going to work on pumps, you can put pumps in their own asset category. You can put all that stuff together. We do some bundling here in terms of our assets legs. Instead of sending a guy out to do every single water cooler and then start again and do every single ice machine, we bundle mechanical room equipment together, so he goes into that mechanical room one time. He goes in there and services everything and cuts down travel time walking basically in circles. There's much more productivity out of the technicians.
RANGEL: A component of the 2006 rollout was the development of specific support roles that would be responsible for work schedule creation. One of the new positions created was that of planner schedulers. The planners were responsible for developing work scopes, identifying materials and creating weekly work schedules for every technician in their craft group. Planners scheduled work using the following set of rules: preventive maintenance is scheduled by due date; client requests are to be scheduled based on first-in and first-out; and self-generated work is scheduled based on material availability. The result was an increase in equipment reliability, improved customer satisfaction and lower backlog. Yet another benefit was that technicians now had a set schedule against which their productivity could be measured.
LUCAS: We are a state institution whose funding is based on a square-foot formula. The formula for administrative employees would normally allow us to hire two more full-time equivalent workers than we currently have, but due to the recession and all the other cuts we were forced to cut back. But due to our strong use of the web request portion of our CMMS, it's helped reduce phone calls and helped us to overcome these losses. Overall, it's resulted in a labor savings of approximately $125,000 a year. We've actually been able to process more requests with fewer employees. Another example is, our old method of billing was to wait until the job was done before processing the charges. Many of these jobs were long in duration, going on for months at a time, and wouldn't be completed until close to the fiscal year end, and by that time a customer has exhausted their funds to pay for the job. This resulted in an average of $250,000 a year in savings from work that normally we would be forced to absorb because the customer ran out of money. Because the CMMS allows us to electronically link to other systems, it's become economically feasible to post charges on a weekly basis, what we call progress billing, and upload them to our financial system instead. Now we're getting our money on a routine basis every week. That $250,000 is now money that gets to be spent in other areas to benefit the maintenance department. Another example is administrative employees who can do more thanks to having a CMMS. Most of their work used to involve answering phones, performing data entry and handling billing complaints. Because we're now able to use the CMMS and electronic data manipulation routines to manage a large transactional workload by exception, staff members are now focused on accuracy through data reviews, customer service and follow-up issues. We've been able to increase our customer service presence much more in the organization. We have 21 administrative employees, and they manage work control, time and attendance, information technology, business operations, project management, and other miscellaneous duties. Our staffing levels as a result of budget cuts tend to trend below national averages, but we're able to keep up and do more because of the CMMS. Back in 2010, we took on an additional 450,000 square feet of new space and didn't have to hire new employees. We were able to handle it all. A strong use of the preventive maintenance (PM) module has not only cut repair costs and frequencies but has extended uptime and useful life of assets in many cases. This has also allowed us to slow the rate of deferred maintenance backlog increases and allows us to address project backlogs with existing funds. Now a reduced technician staff can focus more time on timely capital improvements and replacements, rather than chasing down repairs.
How has the CMMS changed the way the department collects, analyzes, and uses data related to facility maintenance?
RANGEL: Having our CMMS has allowed our organization to establish uniform methods of how data is collected and extracted. Our organization created a central call center that receives all service requests via e-mail, phone or fax. The use of a central call center helps ensure that data in our system was entered uniformly, which later facilitates data extraction. Our organization established some basic performance metrics that would be used to measure how both individual business groups and the division are doing. Two example metrics are on-time PM completion and employee productivity. These metrics measure if PM work orders are completed on time and how many productive hours and employees work per week, respectively. These reports have led to the standardization of maintenance, which eventually led us to more critically examine staffing levels. Through careful examination of data and attrition, our organization improved employee productivity by 20 percent. Other customized reports have been created to help the division improve customer performance through such things as backlog management, as well as average work order completion time.
LUCAS: The wealth of historical information has helped us make some great decisions. Every time we consider spending funds on a project or campus improvement initiative, we always calculate a payback to determine if such a course of action makes good economic sense. This historical data we've collected and stored in the CMMS assists us in making these determinations. We also use the data in the form of a variety of reports and performance metrics to compare ourselves to similar organizations and, most importantly, to our own past performance to see where we excelled or where more attention is needed. As new requirements arise, we can begin to collect related data to determine how well we're meeting them. If industry changes come along or we need to collect something for a research project, we can certainly accommodate that. We can then generate historical queries on equipment and assets to see trends, make better-informed repair or replacement decisions. Something that is important is the need to disprove negligence when unfortunate things happen, to support compliance, and to support a case for supplemental funding when it's needed. We can also justify staffing levels and how well they align with goals, objectives, expectations and the mission of the department. This information becomes part of a much larger annual report generated each year that shows who we are, where we are presently, where we've been, where we're going, and where the public dollars are being spent to maintain the assets that have been entrusted to us. This type of information helps our organization be as transparent as possible and provides valuable information for limiting our portion of the cuts during the last round of budget reductions.
ADCOCK: This product has a report function, so we can go in there and track if we're getting excessive callbacks. By linking a specific asset to a space or a particular piece of equipment, you can track how much work we're doing in there. If we're getting excessive heating calls in a particular area, we can look back and say we have had multiple calls in the last couple of weeks, (so) something in addition to a normal failure going on. It allows us to do a lot of trending for various types of calls, so we'll know not only callbacks but also how many callbacks we're getting in a specific timeframe. In health care, you're being measured by HCAHPS (Hospital Consumer Assessment of Healthcare Providers and Systems), and one of the HCAHPS is hospital environment. So we can look at if we're getting a lot of heating calls or cooling calls over the course of a year. It gives us a direction of where we need to go to see if we need to work on something particular. Trending those calls, we can measure staff productivity. So you can pull up and see how long does it take a particular task to get completed. Say it's changing a light bulb that generally takes 15-20 minutes. Is somebody taking more like an hour? Measuring productivity gives us an avenue to oversee our regulatory management like Joint Commission and Department of Health work orders so we can issue life-safety work orders and issue the work on specific dates and show we completed the work and everything we were supposed to do as planned. And customer satisfaction surveys, we send out random work orders with surveys from time to time just to make sure we're doing a good job, (that) our customers are happy, and we're giving good service.
What challenges has the department faced in maximizing the data collected in the CMMS?
LUCAS: As so often happens with us, we seem to be victims of our own success. In the cases of information collecting, our information is often so good that others want it. With these demands comes having to make time and expand the availability of our custom reports and queries and create custom interfaces to other systems that require a steady flow of information. A great example of this is grant applications, where the cost of maintaining a specific space is often part of an overall request for research funds. Campus-wide emergency response plan solutions also create situations where common data elements must be decided upon in advance and a data custodian assigned to ensure consistency data across multiple databases. The coding decided upon often can be at odds with what a facility-maintenance (FM) department's needs are to adequately document their work. This can result in crosswalks and other conversion tactics to ensure that data is populated in the right place. Finally, a certain piece of data that an FM department may need to collect doesn't always have a pre-determined field or table in the CMMS in which to reside. So often we're forced to use user-defined fields and ancillary tables to make this happen. These require thoughtful considerations and training to ensure everyone understands their use and where the data is stored and the ability to write custom reports so the data can be extracted.
ADCOCK: Initially, it was starting with a good asset program. There are multiple parts to that computerized maintenance software. It's not only having good software. It's having a good management system. Some of our challenges were getting all the space assets and all the equipment assets loaded into the systems, first and foremost. Probably one of the other challenges as time goes on is adding new assets and deleting old ones. You have to be on that system every single day, making sure you are managing it. It's easy to get a buildup of a lot of assets that are not currently in service or not been managed, so managing it from that aspect is probably our biggest challenge.
RANGEL: Data collection and retrieval is a key indicator of whether a CMMS is going to be useful in helping an organization identify opportunities for improvement. Our organization's CMMS was not set up with any type of data collection system, so we rely on technicians to manually document how long and what they did on each job they complete on a daily basis. This information is entered daily into our CMMS, which while effective, still relies on a data entry person. A more ideal solution would be to have a system that is designed to support devices that allow technicians to make updates, which then allows for the CMMS to be updated in real time. Having quicker, more accurate data would allow our organization to have a more dynamic backlog management process that could more accurately measure our response rate to work orders.
What impact has mobile technology had on technicians and the department?
ADCOCK: One of the things we've done is added a tablet-type personal computer (PC). We've integrated that into the system and had it for about two years now. I have a life-safety technician who is able to go around and handle all the different life-safety and joint commission inspections with this PC. He's able to get his work orders uploaded onto the PC, but also he's got a host of different tasking log sheets that he can pull up, so he can integrate those two items as well. That's helped us moving forward. We're (also) looking at the iPad. Our maintenance software allows for us to utilize an iPad, so in 2014, it's something that I will start to change us over to and start emailing more work orders as opposed to a dispatcher issue a work-order and send technicians to a particular call. Especially the things you're going to schedule, we'll be able to do that with this software. We're starting to get into that asset now, but the PC was our first step into being more automated out in the field.
RANGEL: Our organization is currently investigating which mobile technology will best support our needs to collect data, make information such as prints available to technicians, and facilitate PM rounds. Devices such as iPads, handheld scanners, and tablet PCs are under consideration.
LUCAS: We were kind of late getting into the mobile market, and the reasons were pretty simple. Mobile devices were evolving and changing at a very rapid pace the last 10-15 years. A device that became lost or defective could seldom be replaced with the same exact device, and often the newer version wasn't compatible with the CMMS or the current operating system in use or worked with limited functionality. A lot of my colleagues ran out and bought PDAs, and I would defy anyone to go out and find a PDA today. That's an example of how technology has changed. We've calculated the return on investment on initiatives like this before, and for many years it was difficult to calculate a reasonable return when technology was changing faster than we could recoup our investment. So we held off on implementing mobile technology solutions until recently. Now that smartphones and tablet technology have somewhat stabilized, we're starting to deploy mobile devices on a limited basis where it makes sense to do so. Tablets have been recently integrated into our warehouse operation that will assist with day-to-day duties, as well as year-end inventory. Tablets are also being deployed to our controls technicians that enable them to electronically manipulate HVAC systems during PM activities. They are being considered for our night crew so they can access the CMMS from the field, which will increase their productivity and save on trips to the shop. Finally, we're starting to make use of smartphones to be used for requesting leave and overtime approval, as well to check their accruals and balances. These become self-service tools that allow employees to have useful data wherever they are and satisfy their immediate needs and overall save time.
If you were to replace your current CMMS, what new or upgraded features and functions would be the highest priority?
RANGEL: Two key factors that would influence the selection of a replacement CMMS would be how well could the CMMS interface with existing personnel and accounting software being used by our organization, and what mobile devices can the CMMS support.
ADCOCK: I think our current program probably has everything we need now and probably moving into the foreseeable future. If I was going to change, I'd probably want a product that was geared towards health care, with some program written in it that can handle regulatory items like Joint Commission work orders, Department of Health, and supporting PDA iPad automation. One of the other things is making sure it's competitively priced and user-friendly. User-friendly is probably a big point because anyone has to be able to go out there and utilize the program with minimal experience.
LUCAS: We're happy with our CMMS, but we're always looking ahead to the day when we might need to replace it. The biggest thing, of course, is the web-based technology. It's attractive and I like it, but I also know of some systems and some clients where the reliability of the network and their ability to access to stored data isn't where they'd like it to be. Slow or unreliable networks and restricted access to stored data can interrupt operations and reduce productivity and of course hinder the ability to share data, which we make extensive use of. A favorable architecture can increase information sharing, reduce IT needs, reduce maintenance costs, improve data access, and create a more seamless interface to mobile devices. Something else to be wary of are version updates and maintenance releases on web-based systems. However, this can easily become a hindrance when a new release contains flaws and errors that can adversely affect business operations. Often in web-based systems, you cannot revert back to older releases, so it's incumbent upon the CMMS vendor to rectify this as soon as possible and not wait until the next scheduled release. As much as we try to standardize everything we do, there will always be exceptions. Exceptions to established rules and processes account for most of the Scotch-taped sticky notes around workstations and PC screens. So one of the things I'd be looking for is a feature that allows for the customization of pop-up messages and reminders that are triggered by keystrokes and drop-down-menu selections. For example, you may have deactivated a piece of equipment to renovate a facility or have a restriction on certain tasks being performed in research spaces. While trying to create work orders to these assets, a message could pop up explaining the situation and offering instructions and alternatives. Messages may trigger for an indefinite period of time or stop triggering on a specified date. It also assists with training, because when you're training a new employee, you can't always cover everything that might happen over the course of a business day. This would be a great for new employees. I also would like the ability to customize how the CMMS searches for duplicate work orders and have more viable options when one is spotted. Often the duplicate detections feature of a CMMS is very general in nature and hard-coded into the programming language so it can't be changed. For example, it may trigger a pop-up message anytime a work order for the same task is created against the same space within a couple of days of one another. However, a single roof leak could affect many spaces in the same building, or a different but similar task code could be used for the same space on two different work orders. This would also go undetected as a duplicate. But with the ability to customize how the system looks for duplicate requests, it could be tailored to better fit the needs of the organization and be more inclusive. I would also like three options anytime a potential duplicate is identified. The first to create another work order, the second to reject making an additional work order, and the third to document the call details on the existing work order. This last one is one I'm most interested in, because effectively it would result in one work order containing all the information details from all the other customers that called about the issue. Such a situation would help me avoid creating multiple duplicate work orders for the same issue, while still having the names and comments of everyone that reported the issue, and have their contact information so I can update them as the issue is addressed. Overall, gaining more efficiency using web and mobile technology is what I'd be looking for, expanding the role of a CMMS to alert the user to rules and process exceptions, and customization of pop-up messaging and duplicate detection.
Related Topics: