Mobile Technology: Managers Offer Insights and Strategies
Managers discuss the benefits of technicians using mobile technology while out in the field
By Dan Hounsell, Editor-in-Chief
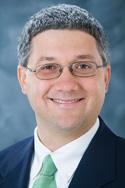
J.D. Hardy,
Associate Director for Engineering Services,
Mississippi State University, Starkville, Miss.,
|
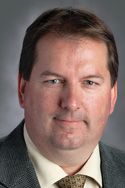
Darin Hargraves,
Senior Director of Maintenance and Operations,,
Anchorage (Alaska)
School District
|
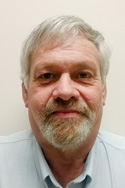
Curtis Orndorff,
Manager of Building Maintenance,
Frederick County (Md.) Public Schools
|
Smartphones, tablets and laptops are making their way into the hands of a growing number of front-line technicians in institutional and commercial facilities. These mobile devices are putting more technology and power than ever in the hands of the workers who can benefit the most. But getting these devices to technicians, while beneficial for departments and organizations, is not an easy task. Managers need determination, vision and, often, a little help in the right places to achieve their mobile technology goals.
What has been your organization’s attitude toward mobile technology use among technicians?
ORNDORFF: Our organization has been very pro-technology. We went through a phase where we were installing Wi-Fi in classrooms for students. I had asked to be a part of that to see if there was some way that we could use it to our benefit in maintenance and operations. Our chief operations officer at the time got on board with that pretty quickly. In 2013, she actually pushed so we were able to get tablets into the hands of every technician. So we did a pilot program. We put 12 tablets out in different areas so that we knew the Wi-Fi was going to work and so that we were seeing things we wanted to see happen.
HARGRAVES: There was hesitancy at first because it was different, but we found that the younger crowd had much less hesitancy. The ones who had been with us for long periods of time and had operated under the old system just weren’t used to it, but they got over it.
HARDY: When it was first implemented, there might have been some apprehension and nervousness about the technology. Folks wanted to do things the way they had always done them. We crossed that threshold several years back, and now it’s integrated into how we work.
Which mobile devices do your technicians use?
HARDY: A large part of our maintenance staff, whether it be a technical trade like electrical or general HVAC, use tablets or iPad-like devices to issue work. Our work management system is built around issuing tickets and jobs electronically. They can utilize their smartphones, but what’s provided is a Wi-Fi-enabled tablet-like device.
HARGRAVES: Some of them are doing their work on their smartphones, but we’ve given all of them iPads to call up their work orders. In our electronics, safety and automation groups, they use laptops. We have more than 43,000 points in our automation system, and for years, they’ve used laptops out in the field in order to look at the system and adjust the temperatures and settings of boilers and other pieces of equipment. The other crafts had not had the opportunity to evolve to the point where they were using such technology. Within the last couple of years, that has changed.
ORNDORFF: Every technician has a fairly large tablet, and each one has a cell phone. Neither one of them have data plans. We rely strictly on the Wi-Fi to provide our data communications. Some technicians have laptops. Our fire alarm and building automation system people and our supervisors and foremen have access to laptops so they can plug into the building automation system and equipment they need to have direct access to.
What challenges did you face in generating buy-in for mobile technology?
HARGRAVES: To progress to the point of using technology, we had to look at our software. Originally, there was some hesitancy about how that would affect some of the principals and other people who had to interact with that software. When we made the change, the administration and everybody else saw the benefits in it, and principals, because they are more technology oriented, they accepted it very quickly. Our IT department also had to evaluate the decision to bring in new software, and that took four or five months. The wanted to evaluate whether we could get it to hook up with various systems — our time card system for example — on the back end.
HARDY: Fairly high-level administrative folks in our division saw the opportunity for our work-management system. They saw some efficiencies there. The knew that mobile technology was going to be part of this transition. They saw the trend as to where maintenance and work management systems were heading. The technicians before that were using a computer-based system without mobile technology, Technicians were printing out individual paper tickets. That was part of the transition going with these devices. The font was small, and it was hard to read. How do you use it? There was a lot of training, and there was a lot of effort to make it so that they didn’t have to make 15 different selection to get to what you needed.
ORNDORFF: When the chief operations is supportive of it, there isn’t a whole lot more I had to do at that point. She was very good at making sure funding was available so we could buy all of them at one time and put them in the hands of technicians. Handing something out to 114 people involves setting up individual sessions and going over the basic way the device works, and that’s an ongoing process. There was some hesitation and uncertainty, but given our location — it’s a highly technical area of Maryland — people are used to a smartphone that does the same thing a tablet.
What challenges/drawbacks have you faced in implementing and using mobile technology?
HARDY: We used a Wi-Fi-based system, and we had good coverage on (the 300-building) campus, but there are some gaps. For technicians working inside, as well as outside, a building, there are times where they hit a spot where they can’t get information or it logs them out. So having good wireless coverage is something to consider. We were lucky to have a wireless network, but we definitely were able to find some of the gaps in the coverage.
HARGRAVES: During the implementation of the software, we tried to limit the effect on our people. We cut off our old system and immediately started with the new system, and over the course of a month or two, it just became standard practice. A lot of addressing the challenges came down to training and working with our people to make them feel more comfortable with the new process. I think very quickly people say the benefits of the new system. They became more accepting and knew this is what we needed to do. A lot of it came down to attitude and making sure we weren’t changing for the sake of change. We changed because we needed to become more efficient. This is best practice in our industry, and we needed to evolve as a department.
What benefits has your department and organization realized from mobile technology?
ORNDORFF: We’ve scanned all of our building drawings and all of our O&M manuals and stored them on a network drive. So a technician with a tablet in their hands has access to all of those documents. We aren’t too far from completing the integration of all of our building automation systems into one front end. That will give the technician quick access to the system and control the piece of equipment he’s working on right there in his hand. It also has given them access to online purchasing, with the purchases being recorded directly to the work order. We’ve had cases where they’ve used it to go online to search for a Youtube video of how to repair or diagnose something.
HARGRAVES: We were expecting about a 20 percent increase in efficiency, and have realized that at least. Given the old system where people would fill things out manually, people now can look at the work orders for a building while they’re in the field, so they can work on multiple work orders while they’re there. There also is a whole lot less transit time when you’re using this type of technology. People can pull up the work orders they need while they’re there. They’re not limited by the printed work orders in the folder they’re carrying around with them.
What are your short-and long-term plans for mobile technology use among your staff?
HARDY: We have an ad hoc system where we send out technicians with tablets to take pictures and make notes, and we store that information using an electronic file structure. So we’re looking to add features to our work management system where that information ties seamlessly back to other things that have been done related to that building. That’s the next step in my area.
ORNDORFF: We’ve had technicians use Facetime on the devices. We haven’t seen real big usage so far. If you’ve got somebody working across the county, that can be a 45-minute drive, depending on traffic. If you can use Facetime to have a face-to-face conversation via the network, you save that travel time.
HARGRAVES: Mobile technology has allowed us to become a lot more efficient, so we’re looking at ways we can improve or capitalize on that process. We’re going to use technology to attack our problems in the future. The data-driven process that we’ve established here — managing our work using the (key performance indicators) — has become huge for us. We’re using technology overall in our department in a much more robust way, and it has made us a much more robust department. The mobilization is a key piece of that approach.
Related Topics: