Managers offer their insights on the benefits of technicians earning certifications and credentials
OTHER PARTS OF THIS ARTICLEPt. 1: This Page
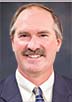
Lowell Hanson,
Associate Director for Facilities Maintenance, University of Michigan
|
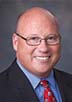
Brian Baxter,
Director of School Plant Services, Virginia Beach City (Va.) Public Schools
|
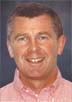
Andy Maddox, P.E.,
Director of Organizational Training, Strategic Planning and Elevator Maintenance, University of Alabama
|
Front-line maintenance and engineering technicians face constant challenges from aging facilities and advancing technology. To meet these challenges, many technicians pursue certifications, credentials and licenses.
These credentials cover a range of areas. Some are from manufacturers related to specific products or technologies. Others are required from government agencies related to safety or hazardous material issues. In this month's roundtable, managers who have successfully addressed these issues talk about their priorities, challenges and experiences helping technicians sort through the options.
How do you determine the most important certifications and credentials for different technicians?
BAXTER: We start with state certifications. We look at the job at hand. Is there a state certification that goes with it? For example, hazardous materials. Those are the easy ones. We've got to have state certifications — lead removal, asbestos, (hazardous waste operations and emergency response) training for possible mercury spills. Those are the state certifications that we start.
MADDOX: We're constantly researching new technologies and best management practices as they apply to the different trades. Obviously, we look at the certification and credentials that relate to their core functions. There are a lot of nice-to-have type certifications and credentials that we really don't have the time or the budget to pursue. We do look for anything that is new technology and best practices management and safety as they apply to our department.
HANSON: A primary interest in certifications is for code compliance and regulatory knowledge. Codes and regulations are a large part of what we are held accountable for as far as healthcare and life safety. Certifications on some types of equipment may be desirable, but often these types of certifications are purely technical. That being said, they are considered valuable to the extent staff can put into use the actual training.
How important are certifications to technicians?
HANSON: I believe most technicians view their certifications as important and a source of personal pride. Many would like to be paid over their peers for such a distinction or have a choice or preference for some type of assignment above their peers, all other items being equal. Employees who are passionate about their trade or craft generally want to have their expertise registered over others who are just getting through another eight-hour workday.
BAXTER: Most, I think, recognize the value. Certainly the newer ones coming in recognize it more than the ones that have been in the trades for 20 or 30 years and are more set in their ways and are having a hard time keeping up with technology.
MADDOX: The older employees that have been around for years tend to not feel like certifications are that important. But in general, it is important to employees because it requires some effort to achieve. It gives them a feeling of accomplishment, so it's important for their self-worth. And it's always a pleasure to recognize them for their accomplishments.
How important are
certifications,
credentials, and licenses in hiring decisions?
MADDOX: If we have a job opening and we're looking at a lot of applicants and resumes, it's very important to see what kinds of credentials they have. It's a good measuring stick to determine their level of expertise. Somebody that's got numerous certifications, credentials, licenses, it helps that person stand out. In terms of promotions, credentials are important, but people skills and leadership skills are more important as far as who gets recommended.
HANSON: Certifications can also be a screening factor for employee selection. When you have 15 to 100 candidates to choose from, possession of a desired certification can be the difference in making the short list for an interview.
BAXTER: We do look for them because then we feel we have a more qualified applicant. At the same time, we have to balance credentials with experience. If you have equal candidates of 20 years experience coming in and one has credentials and one does not, certainly I'm going to go with the one with credentials. If you have a person coming in with 20 years of experience versus a person with three years of experience and credentials, I'd probably lean toward the 20-year person with credentials.
What role do
certifications and credentials play in promotions?
HANSON: It really depends on the total package an employee is bringing forward regarding their training and abilities. Within our mechanic evaluation and certification for healthcare and commercial building maintenance coursework, we promote maintenance mechanics (MM) through the completion of certification levels, coupled with time in grade. So they need to work two years as a MM1 before consideration for promotion to a MM2, and likewise to the MM3 level.
BAXTER: The more they can do to advance themselves through continuing education, the bigger the edge they have. When you're in the field, you need one skill set. But to move up, you need a different skill set that you can translate down to the field. So when you get to the manager or supervisor level, the credentials make a big difference.
Do you offer
incentives
to technicians?
HANSON: The incentive for MMs is roughly a $5,500 annual pay increase if you consider wages and benefits. Many of our skilled trades employees — electricians, steamfitters, HVAC mechanics, elevator mechanics — have come through the ranks of custodial to maintenance mechanic and into the skilled trades. This is a huge incentive for employees to move up within the organization, and promoting internally addresses organizational morale and career longevity.
MADDOX: Not all of the shops do. But in our elevator shop, for example, it's a requirement to achieve their certified elevator technician credential. If they don't have it, we can hire them, and we give them the incentive to get it. We pay them. It's a two-year program with four different parts. Once you pass each one, you get a bump up in pay, and once you achieve the credential, there's a pay increase with that, also.
BAXTER: Our school division offers $350 for a journeyman's license if it's related to their fields, and they offer $1,000 for a master's license. And we'll offer continuing training here, or we'll send guys to training. The incentive there is they're not paying for it. We are.
Do you have
examples of the tangible benefits of technician certifications and credentials?
HANSON: If we use a contractor to remove asbestos, we have to give the state 10 days' notification. We avoid this 10-day delay by doing the work internally. That in itself could avoid a disaster of a failing pipe under pressure, as well as asbestos exposure to staff in an uncontrolled situation.
MADDOX: The elevator shop is one shop that really puts an emphasis on a credential, the certified elevator technician. It's such a rigorous program that we feel as though once you go through that program, the technician is much more knowledgeable about elevator systems and code requirements and troubleshooting. It really increases the value of that employee.
How do certifications and credentials
affect decisions on
technician training?
BAXTER: It provides a baseline for where they are and where we want them to go. If our equipment demands this type of knowledge, then certainly the credentials they have will tell us if we have to start at the very bottom or if we can start somewhere in the middle or if we can start at an advanced level. It's really about where the technical skills are and how far we want them to go. The further we can take them, the less I have to contract out.
HANSON: We believe the certifications form a baseline education to be built upon. Technical training is constantly evolving, so having a base established serves as a launching point for the next level. An example of this could be the (National Institute for Certification in Engineering Technologies) certification series or certainly elevator certification training. With the changes underway in these service fields, it is very important to constantly assess technical training.
How do you view
certifications from manufacturers
related to a certain technology?
MADDOX: That falls more into the must-have category. In the case of a particular software program, like HVAC or elevator controls, it's really a must to be able to work with that program and know how to work with it successfully.
BAXTER: It certainly expands their knowledge, but if it's a piece of equipment that one is asked to maintain, it's a must-have actually. If we buy a piece of equipment, then we want the training to go with it and the certificate that says you've had the training and can maintain it on your own.
Related Topics: