Lloyd Aaron Photography
Joe Kloeker is the Ultimate Team Player
Joe Kloeker, Truliant Federal Credit Union’s director of facilities, loves sharing the spotlight with his staff
By Desiree Hanford, contributing writer
A then 21-year-old Joe Kloeker, the maintenance foreman at Eveready Battery Co./Union Carbide Corp., had a daunting task: give a colleague in the maintenance department, who had been with the company longer than Kloeker had been alive, his first job performance appraisal. The colleague hadn’t had one in his 25-plus years at the company, and Kloeker thought hard about what to say to a coworker who did his job exceedingly well.
“I mean he was tremendous,” says Kloeker, now 61 and the director of facilities at Truliant Federal Credit Union in Winston-Salem, North Carolina. “The only thing I could think of is, ‘My God, train everybody else. You do phenomenal work and whenever the hard jobs come up, you fix them and you get them running, but you're not passing that knowledge on to the guys that are younger than you.’”
Kloeker learned two lessons as maintenance foreman, his second job after graduating from Eastern Kentucky University with a B.S. in industrial technology. The first was the importance of supporting people and helping them be the best they could in their positions. The second was solidifying his interest in constantly wanting to make things — processes, the environment, his colleagues — better wherever he worked.
Both lessons have followed Kloeker throughout his career, from his 13 years in several roles at Weyerhaeuser Co. to positions with several other companies before landing at Ralph Lauren Corp. for just under a decade. Kloeker joined Truliant in January 2021.
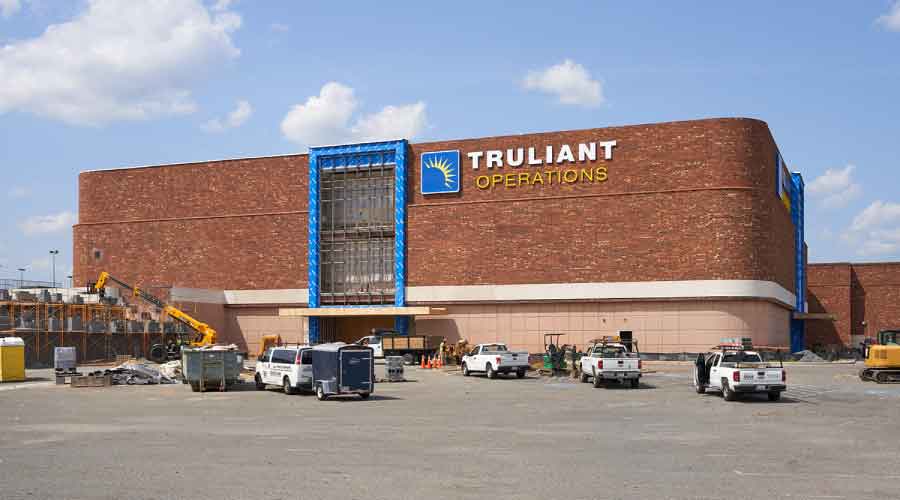
Ron McCracken, who was maintenance manager at Ralph Lauren who worked with Kloeker, saw firsthand Kloeker’s desire to help colleagues reach their full potential and not take credit for their work or ideas. The pair worked together for about four years, and McCracken worked for Kloeker for two years.
“It was such good teamwork,” says McCracken of working with Kloeker. “He’s humble and in no way overbearing or a micromanager. He’s always listening and learning. He’s respectful of everyone, and you can always count on him to make a good judgement call. He’s very happy to share the limelight.”
Supporting the staff and watching out for everyone on the team — the colleagues whom Kloeker describes as the ones that really get the work done — is important because no one knows a job better than the people who do it daily, whether it’s the same routine over and over or a technician who is constantly tackling different challenges, Kloeker says. Over time, those workers do their routines and address enough situations that they determine ways to do their jobs easier, faster and smarter, he says.
An all-in approach
Too many times, supervisors don’t give workers enough credit for their knowledge, and that’s not right, Kloeker says. The people doing the work and coming up with ideas to make things better — no matter their titles — should get the credit, he says. If the idea makes the company better, everyone benefits, he adds.
“I'm very participatory, so I always want everybody involved in the decision,” Kloeker says. “Most of the ideas come from people that do the work every day. I just like to be the tool to empower them or get it done. And if their idea is a good idea, you know it doesn’t have to be my idea. Let’s get it done.”
For Kloeker, having an all-in approach fits with his interest in constantly wanting to make things better. Earning his degree in industrial technology meant learning theory in the classroom and then getting a more hands-on experience in the metal shop, melting metal and looking at molecular structure.
“We’d go build something in the machine shop, and I’ve always been very hands-on and maintenance oriented in that respect,” Kloeker says.
It was at Eveready Battery Co./Union Carbide that Kloeker started moving toward facilities management via the company’s maintenance program, becoming operations manager after two years as maintenance foreman.
“I just like making things better, and I like fixing things and improving not just physical things but programs and processes,” Kloeker says. “I’ve always been kind of a process improvement guy. At Weyerhaeuser they used to say, ‘What are we changing now? Here he comes again.’”
McCracken described Kloeker as approaching his work with a very structured mindset.
“He’s knowledgeable about most every subject for buildings, facilities and equipment and what it takes to keep them running,” McCracken says of their time working together at Ralph Lauren.
Kloeker was the process improvement manager/environmental health and safety/facility manager at Grass America Inc., and facility and maintenance manager/manufacturing engineering at ABB before being named director of facilities at Ralph Lauren in January 2011. The opportunity to have a bigger impact — from being involved with day-to-day responsibilities to the overall long-term strategy — spurred Kloeker’s interest in being a facility manager.
“You've kind of got both hands in the future and maintaining what you have, and you’re making sure the past is cleaned up properly,” Kloeker says.
Continuous improvement opportunities
Even after nearly 40 years in the industry, Kloeker’s interest in the facilities field hasn’t waned. Technology, he says, is constantly changing, and people are learning more about the environment and technology and how the latter can help the former. Buildings are getting older, so there are always things to improve and make better, Kloeker says, noting that improvements that were cutting edge 20 years ago are no longer such great improvements.
“It’s such a varied field,” Kloeker says. “It’s not just fixing the building, but it’s making it livable for the inhabitants — the right humidity, the right temperature, the right air quality. Are the janitors doing what they need to do in cleaning up? It's the whole gamut of how big an envelope it is. I'm a jack of all trades, master of none, so I know the right people to go to when I need a specialist. I've always liked being kind of that hub that connects all the dots in the right way.”
Being a good facilities director means constantly learning and assessing what’s right for a given situation, Kloeker says. That means getting all the stakeholders involved and asking questions: What do the stakeholders want? What is the goal? What direction does upper management want to go? Are you going out on a limb if you go in a certain direction?
Kloeker says he tries to look at a situation from every angle, determining who is going to be impacted, who is going to be helped and what it’s going to cost.
“I guess the trick to implementing new things is to look at the bigger picture,” he says. “You don't do things because they're a pet project but because they are the right thing to do.”
Kloeker oversees about 458,000 square feet of space in three states for Truliant. His typical day is a mix of day-to-day responsibilities and project work. Truliant is growing at a healthy pace, Kloeker says, so part of what he focuses on is maintaining existing facilities at a high-quality level both for members and employees.
That means Kloeker taps into just about everything, including air-conditioning, air quality, building modernization and new construction. He currently has three direct reports, as well as two technicians and four general services personnel. Truliant is growing, Kloeker says, so the company is adding staff so that it can support its growth. Kloeker is in the midst of hiring a fourth direct report, and Truliant will be hiring another general services person and at least one technician/building engineer.
Kloeker kept an eye on about 2.25 million square feet of multi-channel distribution, fulfillment and research and development facilities at Ralph Lauren. That experience was his first exposure to a large data center, which he occasionally provided a bit of support to when needed.
Arriving at Truliant from Ralph Lauren, where nearly 2,000 employees were furloughed because of the pandemic, Kloeker says he brought with him the knowledge about the total cost of ownership, including how investments in items such as a building management system can actually save a company money.
Pandemic’s impact
The pandemic brought more than a change in jobs for Kloeker, including a bigger focus on disinfection cleaning. Instead of only making sure something is clean, it’s now making sure that things are disinfected and sterilized as needed, Kloeker says. There is a greater use of biocide cleaners that kill germs, viruses and bacteria on a broader scale.
“You always worried about the bathrooms and the break rooms and cafeterias and that sort of thing, but to have folks walk around cleaning door handles and doorknobs was all done to keep them clean, not to keep people from getting sick,” Kloeker says, adding that changed with the pandemic.
The number of people working remotely or part time is another change brought about by the pandemic, and so staff members aren’t in a building constantly like they were previously, Kloeker says. This means it’s a bit of a hit-and-miss on the number of people around the facility on a given day. And while people might be working in the office three days a week and not five days, Kloeker says he can’t plan the janitorial needs to fewer days because people are scattered across the whole five days and not concentrated in just a few.
“You can't really balance or scale back any savings to your air conditioning or your landscaping because those three or four days are still Monday through Friday and so there's less volume, but everything is still occupied,” Kloeker says. “It's just a matter of like is it Monday, Tuesday, Thursday, or whatever the case may be, but it’s still five days of a normal work week. We have Saturdays, too, and at Ralph Lauren it was seven days a week. So, you still covered every seven days of the week. You just had less people in the building.”
Trust but verify
The pandemic, however, didn’t change Kloeker’s approach to how he does this job. His default is to be on site, taking care of the facility and helping people. Some people can do the job remotely, Kloeker says, but he’s not one of them, and his colleagues can find him in the office five days a week. He feels he needs to be present, calling it a “trust but verify” approach and one that means he needs to see the work completed by a contractor, vendor or architect.
That’s not to say Kloeker doesn’t trust who works with him or for him. He does.
“I always trust that at the core, people want to do the right thing, they want to be good,” he says.
Still, Kloeker wants to see things for himself. People get busy, and they unintentionally miss things, he says. People who see the same things every day, day after day, have a harder time seeing when something isn’t normal, Kloeker says.
Alex Jenkins, who also worked with Kloeker at Ralph Lauren, said Kloeker took a methodical approach to his work, understanding the sequencing for projects and knowing what needed to get done first and what needed to be accomplished later.
“He always had a good sense of humor and was able to recognize a situation where you had to adjust things on the fly,” Jenkins says.
Kloeker says it’s nice hearing from former colleagues, even many years later, whom he helped with career training or career development. For example, some former coworkers have reached out thanking him for encouraging them to get certified in certain areas which, in some cases, saved their jobs.
“I think (the former colleagues) would say I'm good to work with, good to work for,” Kloeker says. “You know, that I cared about them and getting the right thing done.”
Desiree Hanford is a freelance writer based in Bartlett, Illinois.
Related Topics: