Managers discuss their challenges when buying sustainable products
By Dave Lubach, Associate Editor
OTHER PARTS OF THIS ARTICLEPt. 1: This Page
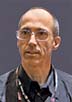
Patrick Crowley,
Deputy Director, Facilities and Engineering Division, San Jose International Airport
|
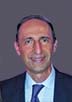
Shidan Adlparvar,
Facilities Maintenance Administrator, City of Santa Monica, Calif.
|
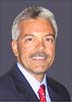
Craig Borkman,
Project Manager, Virginia Beach City (Va.) Public Schools
|
Green purchasing programs, or environmentally preferable purchasing (EPP), are becoming commonplace among maintenance and engineering departments, as managers aim to specify products that minimize institutional and commercial facilities' impact on the environment.
In this roundtable discussion, managers explore their EPP strategies and share their challenges and success stories.
How has your role in green purchasing evolved?
CROWLEY: My early involvement with green purchasing was during the energy crisis in California leading up to the deregulation of the industry. These early years involved the company establishing goals for purchasing green power. This has changed over the past 10 years to a more comprehensive evaluation of procurement involving sustainable or environmentally sound procurement inclusive of all products and materials utilized for operation.
ADLPARVAR: I have been involved directly with green building design and energy-efficiency upgrades and indirectly involved in purchase of green products. Whenever possible and when solicited, our division has provided technical and financial assistance to ensure that the most energy efficient products are designed, procured and installed. Examples include administering the design of efficient HVAC equipment, converting office lighting and street lights to LED lamps, becoming more conservative with the use of water in the city facilities by using more efficient products, and overseeing maintenance of solar panels in seven of our facilities.
BORKMAN: I am always seeking more energy-efficient and environmentally friendly products that will provide a greater return on our investment. This includes the amount of time necessary for preventive maintenance and total lifecycle costs. Our team gathers this information, runs it by the various trade personnel to gain their buy-in, and works with our storeroom to make the purchases. Sometimes we opt to pilot a new product in a defined area. At agreed upon intervals, we monitor, re-evaluate and ensure products are performing as designed.
How have your department's practices and priorities changed over the years?
ADLPARVAR: In the past several years, we have been working closely with our utility companies in identifying energy-efficiency projects and utilizing programs such as savings by design and on-bill financing. We have also joined in alliance with the energy coalition and used technical support and consultants in carrying out energy audits in several of our city's facilities. With regards to water conversation, we have changed out most of our fixtures with more efficient fixtures, such as low-flush valves and some waterless urinals. Three of our facilities utilize recycled water for irrigation purposes and to supply the toilets and urinals. Last year, we set a goal that 86 percent of our paint purchases shall be zero or low in volatile organic compounds (VOC), and we achieved it.
CROWLEY: Initially green procurement was centered on energy purchasing, but our current policies include procuring services on energy, as well as products throughout the organization. The range of products requires reviewing the following impacts: reducing toxicity levels or off-gassing; conserving natural resources, materials, and energy; and maximizing products that can be recycled and include higher recycled content.
BORKMAN: We're moving toward LEDs. Through performance-based contracting, we've replaced all of our T12 bulbs and have moved to T8s. But with the technical advances in the LEDs, we're searching for utilization of LEDs. That's going to be the next forefront, and the addition of occupancy sensors in a majority of spaces through renovation efforts. But in every new school we are building, it's a requirement to have occupancy sensors.
Has your organization realized any unexpected benefits from green purchasing?
ADLPARVAR: Over the years, more (paint and coating) manufacturers are offering various products with zero or low VOCs. In most cases, the newer products have a longer lasting life span with better color retention.
CROWLEY: The expectations of the community are a large factor in achieving the goals established for the EPP policy. Although it is difficult to directly correlate to the EPP policy, the company has seen a reduction in sick days used and complaints regarding indoor air quality. Also, the company has received industry awards for procurement policies and the investment in sustainable practices.
What changes have you seen in products to meet green purchasing needs?
CROWLEY: There is a wider selection of products from an increased range of services. Also, the quality of products continues to increase as additional research discovers improvements to existing product lines.
ADLPARVAR: Generally, many more products are available for a wider range of applications at lower costs. For example, the cost of solar panels has been coming down while their efficiency has been going up. However, not all products have performed well or have met their manufacturers' claims.
BORKMAN: I'd venture to say that any vendor that is offering a product is doing their due diligence to ensure that they are sustainable, that they are having a minimal effect on the environment, and that will continue to be exhibited.
What building systems and components in your facilities have been most affected by green purchasing?
ADLPARVAR: Lighting systems, HVAC systems, plumbing systems, solar systems, paint and carpet tiles have positively been affected in our facilities. In some cases, though, we have experienced that the installation of low-flow toilets have caused stoppages in our sewer lines due to the age and condition of the lines.
CROWLEY: There are three main areas that have been embraced by the purchasing of green products. The first is technology, which is industry-wide in addressing cradle-to-grave procurements. Also the custodial services industry has evolved to embrace a wide selection of green products that are less toxic to the employees and building infrastructure, as well as customers. Finally, the filters used to address indoor air quality are sustainable and include the same cradle-to-grave process as the technology segment.
BORKMAN: We're gaining value in re-lamping. In the summer, we go to a four-day workweek where we are saving energy from cooling the building for three days, as opposed to five. We have building automation control and set parameters. Our custodial department has undergone training with the custodial staff. It used to be they turned on every single light in the building and would go room to room and shut the lights off. Now they work as a team and work through wings and only turn the lights on as they get to that wing.
What is your department's next step in specifying sustainable products?
ADLPARVAR: We will continue to work with our Office of Sustainability and the Environment to assist us in evaluating the sustainability of available goods and services, such as reviewing chemical products. We will also look for creative financing options and capital-improvement funding to expedite green projects and purchases. For water conservation, we will install low-flow fixtures in our older facilities and monitor for water leaks.
CROWLEY: The next steps include water and landscaping concerns, especially with the severe drought conditions for over a decade in California.
Related Topics: