Good Data Needed To Take Full Advantage Of Facilities Management Technology
Having accessible data is key to taking full advantage of what technology can offer, says Craig Cherry, operations manager, State of Oklahoma, DCS/Facilities Management Division. Cherry's team has recently replaced a number of chillers. One requirement of the new chillers is that they have to have the ability to interface with the building automation system. By doing so, they provide in-depth information that helps inform decisions on how the systems should be run. But it's not just a focus on taking advantage of everything HVAC can offer, Cherry says.
"We're really trying to use technology whenever we can to help us work smarter, and improve our operations and how well we respond to what's going on. And we're doing that across the board — equipment, fire alarm systems, whatever. If we can use that technology to help us with how we're doing our jobs, that's what we're concentrating on," he says.
Areas Of Concern
If technology systems offer more information, that, again, helps when it comes to making the case for a capital investment or budget flexibility. In addition to that, it can help save time — and therefore money — when a piece of technology can report its data as opposed to someone having to go record it.
There are a couple areas of concern. Cherry points out that his department is requiring manufacturers and suppliers to provide specific information on what data can be provided, how it can be collected, and how to determine what is necessary information and what can be ignored. A chiller might have hundreds of potential information points, so that's a lot of possible data to sift through.
"When we do an interface with it, we can see just a ridiculous amount of information," he says. "But what does that information really mean? And what are the correct parameters that this should be operating at, at different times?
"There's a fine line on getting too much information. We want to make sure we don't overload ourselves with information that doesn't matter."
Another potential concern is that making a big investment in technology can only go so far. The technology has to be used correctly and operated properly to see a benefit. And no facility manager wants to be the one to have to explain why the fancy new technology isn't living up to expectations.
"I had an engineer one time tell me that the worst-operating building he had ever seen had an Energy Star score of 1 — and the building was only two years old," Herrin says. "So having the latest and greatest systems in place doesn't mean anything if it's not set up and operated properly."
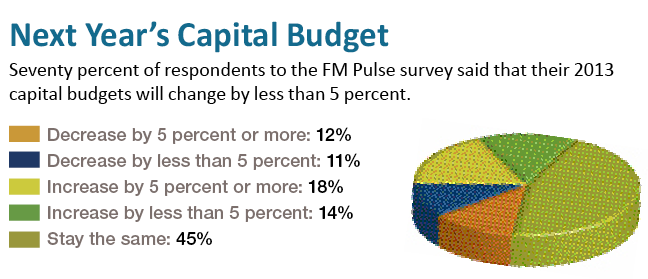
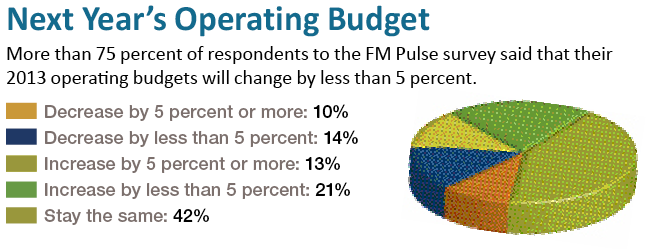

Related Topics: