view all Case Studies
Montpelier's District Energy System Has Been a Success with The Aid of SWEP BPHEs
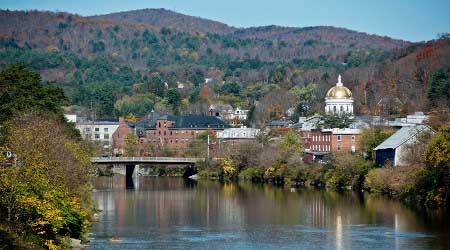
The $72 million renovation of the 55-year-old, 70,000-square-foot Daniel-Meyer Coliseum at Texas Christian University presented many issues related to HVAC, specifically the roof's load-bearing limitations.
May 17, 2017 -
Energy Efficiency
By Gregg Ellis
With slightly less than 8,000 residents, the city of Montpelier, VT, boasts the smallest population of any state capital in the United States. Despite that status, the city has always had big ideas when it comes to supplying municipal services for those residents. One of the most significant in recent years was the decision by community leaders to create and implement a District Energy system that would be used to heat and cool many businesses and governmental buildings in the city’s bustling downtown area.
In 2010, after the completion of a feasibility study conducted by Montpelier and the State of Vermont, the city was awarded an $8 million grant to construct a District Energy generation plant, known as a Combined Heat and Power (CHP) facility, in the downtown area, along with a network of underground pipelines that would distribute thermal energy for heating and cooling to the buildings that would be connected to the District Energy system.
What attracted Montpelier’s city leaders to the idea of District Energy was the fact that the need to use and maintain separate boilers, furnaces, chillers or air conditioners in each building would be eliminated. Additionally, after the hot water, steam or chilled water that is used to heat or cool each facility is extracted, the remaining water is transferred back to the CHP to be heated or cooled again. This results in a heating/cooling system that is 100 percent efficient, whereas buildings that have their own individual systems powered by fossil fuels are often much less than 80 percent efficient, leading to a lower return on investment and less manageable utility costs.
Finding the Perfect Fit
With a completion date set for 2013, and the first buildings to be serviced by the District Energy system including two churches, a school, an insurance company, the city’s police and fire stations, and the Washington County sheriff’s office and courthouse, the next step was outfitting the system. Critical components would be the heat exchangers that would be used to help gather any waste heat energy and aid in its transfer back to the CHP.
It was this requirement that caught the attention of Jake Goldberg, Executive Vice President/HVAC Division for Diversified Heat Transfer (DHT), Inc., Towaco, NJ. Since 1982, DHT has been an engineering and manufacturing company dedicated to the design and fabrication of heat-transfer equipment and systems.
“We found out that the State of Vermont was going to install a District Energy system in Montpelier, so we got in touch and started working with them,” explained Goldberg. “It was a new project, new plant, that wanted to deliver hot water to business and community buildings with intermediary heat exchangers that would transfer and utilize the heat in their buildings.”
With DHT a longtime distributor of brazed plate heat exchanger (BPHE) technologies from SWEP North America, Duluth, GA, Goldberg knew that SWEP BPHEs would be the perfect solution for Montpelier’s District Energy setup. SWEP BPHEs checked all the operational boxes because their method of construction allows media at different temperatures to come in close proximity as it is only separated by channel plates that enable heat from one media to be transferred to the other with very high efficiency.
Specifically, SWEP BPHEs optimize heat-exchanger performance through their compact size, high energy efficiency, leak-free operation, cost-effectiveness, self-cleaning capability and the ability to be customized to meet the needs of unique installations. In all, seven models – with capacities ranging from 39.6 gpm (150 L/min) to 684.6 gpm (2,598 L/min) – and 100 total SWEP BPHEs are used at various points in Montpelier’s District Energy system, and in around 50 different installation configurations.
“Working with our engineers, and our regional rep in New England, R.L. Stone, we were able to get them everything they needed at all times,” said Goldberg. “Every building had different requirements, from flow capacities to water temperatures to pressures, and SWEP’s wide variety of products made it easy to design everything they needed.”
In the nearly three years that Montpelier’s District Energy system has been online, its performance, and that of the SWEP BPHEs, has met or exceeded all expectations.
“It’s one of those clichés of no news is good news,” said Goldberg. “We have not had one issue with any of the 100 BPHEs we supplied, and as buildings are being added to the system, we are supplying them with SWEP BPHEs.”
Conclusion
Founded in 1787, Montpelier is also one of the oldest state capitals in the U.S., but that hasn’t prevented it from being one of the most forward-thinking. The creation of the city’s new District Energy system is just one of the latest examples of that, and it appears that it is a decision that will pay dividends well into the future.
“It’s a combination of our engineering and the high quality of the SWEP BPHE product line that has really helped us achieve everything that we wanted to achieve with this project,” concluded Goldberg.
Gregg Ellis is the Dealer Sales Manager for SWEP North America, Inc. He can be reached at (603) 400-0630 or gregg.ellis@swep.net. Founded in 1983 and acquired by the Dover Corporation in 1994, SWEP is a world-leading supplier of brazed plate heat exchangers (BPHEs) for use in the HVAC (District Energy, Residential Heating, Air Conditioning and Refrigeration) and Industrial (Energy, Process and Production, Temperature Control, and Marine and Transport) industries. Designed to make the most efficient use of energy, material and space, BPHE technology is quickly winning acceptance around the world in many of these markets, with SWEP at the forefront of its development. SWEP’s North American sales network is headquartered in Duluth, GA, USA, with the manufacturing center located in Tulsa, OK, USA. For more information, please visit swep.net.
Next
Read next on FacilitiesNet