How Gundersen Health System Achieved Energy Independence
Corey Zarecki has used his process improvement expertise to save energy, deploy renewable energy projects, and drive out waste from Gundersen Health System's facilities.
The cogen project had a huge problem: There was too much sulfur in the biogas. Corey Zarecki, director of engineering and operations for the Envision program at Gundersen Health System, had initiated the project and dove right in to fix it. Zarecki is a chemical engineer by training and a problem-solver by nature. If necessity is the mother of invention, then aversion to failure is its father. Zarecki was sure he could come up with a solution and put the project back on track.
The cogeneration system was part of a partnership with a nearby brewery — the engine would produce electricity from the brewery’s waste process and the brewery would use the heat in its anaerobic digester. But the brewery’s waste process was producing biogas with an unacceptable level of sulfur, threatening to deep-six the economics of the project. “Internal combustion engines don’t like sulfur,” explains Alan Eber, Gundersen’s director of facilities.
So Zarecki researched, experimented, designed, piloted, and eventually patented a chemical process to reduce the amount of sulfur in the biogas. Clean energy project back on track.
“What looks awesome at the start of a project may not look awesome in practice,” says Zarecki, subtly downplaying the hurdles he had to jump through to get this project to work. By creating a solution, Zarecki resurrected the project. It’s a story emblematic of Zarecki’s drive and creativity, say his colleagues. “He abhors failure,” says Eber. And these qualities of being inventive (literally) and refusing to fail are the main reasons for Zarecki’s success in energy efficiency and renewable energy at Gundersen.
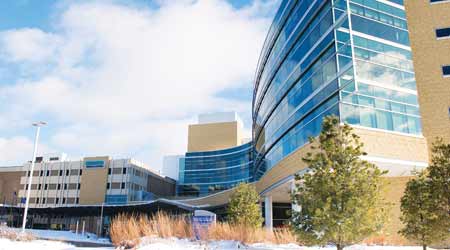
(Gundersen Health System is the first health system in the United States to be fully energy independent. The system’s headquarters campus in La Crosse, Wis., contributes to that goal with a geothermal system and a biomass boiler with a back pressure steam turbine. Photo: Gundersen Health System)
Gundersen Health System is a non-profit healthcare system center in La Crosse, Wis. Zarecki has been and continues to be instrumental to Gundersen’s goal of reducing healthcare costs and achieving energy independence. His strength is identifying and rooting out energy waste and creating a series of ever-more-creative renewable energy projects. Zarecki came to Gundersen in 2008 as a process improvement expert — a Six Sigma Lean Master Black Belt. His boss, Jeff Rich, the executive director of the Envision program, had come to Gundersen in 2006 with a similar background. Envision is both the name of Gundersen’s overarching sustainability initiative and also the organization within Gundersen at which Zarecki and Rich work on sustainability. Rich had been charged with identifying ways to lower the cost of healthcare for the whole health system. Energy was a good place to start. Gundersen spent $5.3 million on energy in 2008, and that number was rapidly increasing.
“The energy bill had been going up about $350,000 per year,” says Rich. “So the question was ‘What can we do about this?’ I hired Corey, who was supposed to be working in supply chain process improvement. The idea was to have him work on energy for six months and then go back. But for the last decade we’ve been working on energy and sustainability.”
How do two process improvement engineers tackle energy efficiency? “The heart of Lean Six Sigma is eliminating variation and eliminating waste,” says Rich. “And the heart of sustainability is eliminating waste, so the tools fit perfectly.”
Says Zarecki: “There are engineers out there way smarter and way better than me on energy audits. But I have always worked on projects where there was uncertainty and I didn’t know at the beginning how I’d hit the goal. But I knew the methods to get there through Six Sigma.”
Setting the goal came first, and one of the things Zarecki applied from Six Sigma was to make the goal substantial — the absolute best performance possible. Why not go all the way to energy independence? The main reason they’d identified this goal was, first, financial: To help lower overall healthcare costs. But also, there was a human health component to the goal: As a healthcare system, they needed to contribute to human health, not be a detriment to it. And in the upper Midwest, where a lot of electricity was generated with fossil fuels, Rich and Zarecki knew they needed to dramatically change Gundersen’s energy profile to move away from dirty electricity. Efficiency was the first step.
“When we started, and compared ourselves to everyone else, we were far from the best,” says Zarecki. They began gathering data and realized six buildings — large medical facilities — constituted about 85 percent of the system’s entire energy spend. So, naturally, they worked on those first.
Zarecki developed what he calls a “cause and effect matrix” — basically a way to prioritize projects based on their cost, benefit, payback, speed to implementation, and likelihood of success. “That helped us figure out what we wanted to work on, and it helps us get approval because you know what you want to do and you have the data to back it up,” he says. From there, it was an iterative process of getting approval, doing the project, measuring the results, getting approval for a slightly bigger and more expensive project, and so on. The projects covered just about every facility energy-using process possible.
“We did dozens and dozens of projects ranging from chiller projects to just scheduling off exhaust fans,” says Zarecki. “Though identifying projects and setting the matrix is a huge amount of time, it’s so important to do that upfront work because then the rest comes easier. Typically, people create these project lists and just hope they happen at some point. Instead, we quantified the benefits as accurately as possible.”
Zarecki mentions one of the dangers of getting outside energy audits as a starting point: “Someone comes in and does an audit, makes a big binder of projects, and then it collects dust. We actually had those binders. I am not that person. I hate that. I like execution, improvements, and getting things done.”
Related Topics: