Facility Managers Can Boost BAS/EMS Performance With New Tools, Capabilities
A wave of innovation is sweeping through the building automation and energy management fields. For facility managers who understand the emerging options, those changes mean new opportunities to improve performance.
Technical improvements in reporting and dashboards, strong middleware and software platforms, better graphical user interfaces (GUIs), detailed analytics and fault detection, and real-time demand response capabilities are some of the tangible newer developments that are being deployed in BAS/EMS applications. These capabilities are sometimes being offered within BAS/EMS applications themselves, and sometimes they are separate applications from companies that don't make BAS/EMS.
Economic Factors
Three economic forces are moving more buildings into modern BAS/EMS operations, says Jack Althoff, owner of ProJex, Inc.
First, tenant comfort is significantly improved, because building management can monitor building components more thoroughly.
"With today's technology, you really can see everything you need to see at a high level to ensure your building's occupants are comfortable," says Althoff.
The second force is control of utility costs. Facility managers can react quickly to address usage anomalies. "So if tenants add a new lighting system that causes their usage to jump by 1,000 kilowatts, you know immediately," says Althoff. "You have time to see if you can do something to correct the matter or possibly adjust the contract with them for the additional usage."
The third motivator is manpower savings. Alarms and sensors keep building operators aware of what's happening via the BAS/EMS network, before staff are dispatched.
Soft diagnostics, built into today's controls, identify potential glitches before they become problems. Sometimes the diagnostics can correct the problem directly. But even when the controller cannot fix the problem, it can note early warning signs. "For example, the controls will note the water pressure is dropping before the basement is flooded," says Althoff.
Improved Diagnostics
One good example of a new technology being deployed is the ability to predict when something is going wrong, before systems stop working altogether. "The BAS operator can't just keep his or her eye on the chiller and big air handling units anymore," says Robert G. Knight, senior associate with Environmental Systems Design. "Now, the facility manager's got fountain pumps and pool chemical controllers and kitchen grease precipitators, all revealing their every inner parameter to the network. So analytics are really becoming necessary to filter through that noise and help direct the operator's attention to the problem."
One software application for HVAC systems uses fault-detection diagnostics (FDD), developed by the National Institute of Standards and Technology (NIST). The software evaluates equipment relationships, such as the chiller's connection to the air handler and the air handler's reliance on variable air volume devices. Using predictive analytics rules, the software analyzes and identifies where HVAC is not running optimally and alerts the BAS/EMS front end station.
"Some of this software really takes on not only DDCs but also systems normally considered outside BAS/EMS monitoring," says Jim Sinopoli, managing principal, Smart Buildings. "These systems are handling exterior shading, interior blinds and even seismic monitoring."
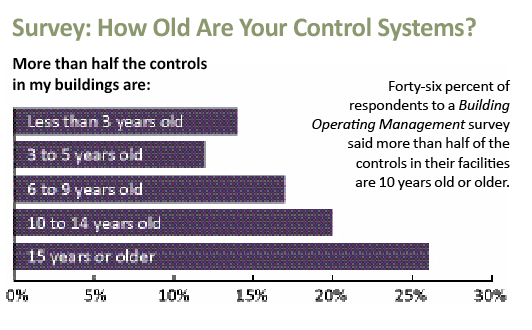
Related Topics: