Energy Upgrades Roundtable: Managers Discuss Energy Efficiency Challenges
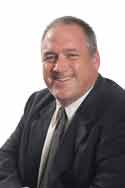 |
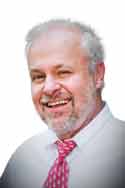 |
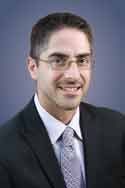 |
Chris Walinski,
Building Operations Manager
Munich Reinsurance America, Princeton, N.J. |
Greg Harubin,
Director of Facilities Management,
Day Kimball Healthcare,
Putnam, Conn. |
Tom Lanzilotta,
Campus Energy Manager,
Stony Brook (N.Y.) University |
Between sustainability considerations and bottom-line pressures, maintenance and engineering managers are under the gun to improve the energy efficiency of key facility systems. But finding energy waste is just the first step. Planning, performing and ensuring the long-term performance of energy-efficiency upgrades all present tough challenges that managers must overcome.
What steps does your organization take to identify energy-efficiency upgrades with the greatest potential?
Walinski: We invest in energy auditing, benchmarking and enhanced metering to ensure the company makes informed decisions and can validate results for its energy program. The audits and metering highlight areas that should be addressed, and the facilities team tries to use every available resource — attending trade shows and conferences, industry publications, continued education, reaching out to peers, and networking — to identify possible solutions.
Harubin: We rely on engineering data analysis. We look at simple payback primarily for our decision-making. We accept offers from energy-service companies for performance engineering surveys —anything we can get that gives us another look and more data. We also seek projects that potentially replace capital equipment that we already have issues with, and we look for projects that have greater potential for getting utility incentives.
Lanzilotta: We use a collaborative approach to identify energy-efficiency upgrades, which involves obtaining input from technicians, building occupants and the university community. We currently are in the midst of a university-wide energy audit, and from this audit an energy master plan will be developed. As the audit has progressed, we receive preliminary reports, and from these we bundle various projects looking for the quickest (return on investment). We then consider project complexities and duration and how they may impact building occupants.
What is your role in that process?
Walinski: In my role as building operations manager, I am part of the team that brings new ideas to the table. I also oversee the process of the multiple ideas being concurrently reviewed and discussed. Finally, as the manager of the process, once the team decides what upgrades would have the biggest impact or offer the best value, I present the findings to management to procure funding.
Harubin: I guide the process and select the final measures to be packaged and presented for funding to the utilities or the grant entities. There’s a portion of every project that must be paid by the hospital, so I present it to our board of directors.
What is the role of your department in planning and performing energy upgrades?
Lanzilotta: Our campus planning, design and construction, and facilities and services departments work together to determine the best equipment for the project, both functionally (and) aesthetically, and what is best for the environment. We also decide whether a project can be done with in-house staff and management or if the use of outside contractors would be more productive.
Harubin: We participate in that final design. We’re basically driving the bus. We’re integral in the final plans and scheduling. We also run the 24/7 operation, so we’re integral in all the shutdowns and ultimately the final acceptance of the project.
Walinski: Maintenance and engineering make up the team that identifies and cultivates the potential upgrade ideas. Once approved, the team either institutes or manages the institution of the upgrades. One of the other important roles the team plays is in educating the campus employees to the changes occurring to promote the continued growth of the sustainability culture and reaching out to and engaging with employees through focus groups and surveys to ensure the team is looking at potential upgrades in a comprehensive and holistic manner.
Please describe a recent upgrade that has been the most beneficial to the organization.
Lanzilotta: We are at the tail end of completing a campus-wide energy reduction project that involved retrofitting over 55,000 fixtures with long-life, energy-efficient lamps and ballasts, installing over 5,000 lighting controls, and adding variable-frequency drives to control the speed at which electric motors operate. This project helps contribute to Stony Brook’s goal of reducing energy by 20 percent by 2020, improves lighting levels and building controls, reduces maintenance costs, and helps bridge the gap to new technology.
Harubin: The one that jumps off the page is a $400,000 digital control upgrade that we just completed. It was a big piece of the pie for us as far as obsolete controls. The thing that’s interesting about it is that it only had a 7.24-year payback, so we bundled it with quicker-payback projects and got the whole bundle of projects into the three-year payback range. We qualified for a 50 percent incentive from our public utility.
Walinski: Because our projects have so many different combined benefits, it is difficult to choose the one most beneficial, but some of the most beneficial improvements included:
• a building automation upgrade because it had the added benefit of enhanced metering and reporting, which has been critical to the success of many of our subsequent projects
• any of the large-motor variable-frequency-drive projects
• the campus lighting upgrades because they improved the lighting’s ergonomic benefits while reducing operating and maintenance costs, improved sustainability and efficiency, and offered excellent ROI.
• the upgrade of lighting controls by improving efficiency at every level — private rooms, public areas, and workstations. It had the added benefit of giving employees ample lighting when needed but (also reduced) energy use whenever those levels were not needed.
Did unexpected challenges arise during the project?
Walinski: The original biggest challenge was ensuring the team had enough qualified data to support its calculations. Since then, different projects have offered different challenges. Whether a project required more communication to or education of the campus employees, or more research and follow-through to find maximum rebates and ensure they were collected to improve ROI, many of the projects had nuances arise that required the team to shift priorities or schedules.
Lanzilotta: Gaining access to spaces and acceptance of lighting sensors was probably the biggest challenge. To address access and acceptance, we had Q&A-type meetings with building managers as a group and introduced the contractor representatives for face-to-face interactions. We also periodically sent out project updates to the building managers and asked for their feedback.
Harubin: The challenge was the fine-tuning at the end of the job. We’d have two chillers running instead of one, and the controls engineer is scratching his head. (It’s challenging) when you’re integrating packages from older chillers with digital packages with newer controls and trying to get two different manufacturers’ systems to work together.
What steps do you take to emphasize the importance of post-installation monitoring and maintenance during the planning process?
Harubin: Unlike some other maintenance departments that have another group in their organization that manages construction, we’re pretty familiar with construction. We select the engineers and the architects, and we manage the construction process. We’re the owner’s representatives for all that stuff. We’re at the hub. So we’re pretty familiar with what we want as far as deliverables at the end of the job. We require that we get all the maintenance and inspection and testing, the recommended PMs — everything we need to put the maintenance program together.
Lanzilotta: Post-installation measurement and verification are an important step to prove that the project was as efficient as proposed. We accomplished this by using our submetered energy baselines and compared them to consumption after the completion of the project. We also took individual readings of the energy consumed at the fixture before and after the retrofit. This macro/micro approach ensures that estimated savings are realized. To ensure savings are maintained going forward, all old lamps and ballasts were purged from stock (as well as from) hiding spots in closets and mechanical rooms. We would like to avoid old technology from being installed back in the fixture in the event of a failure.
Walinski: The company emphasizes metering at every stage of each project. It is how the team justifies the projects it proposes, how progress is tracked to ensure projects are trending to meet targets, and how upgrades are validated after completion. The campus already employs enhanced metering in every major mechanical and electrical system and additional metering is installed as part of upgrades when appropriate. The team relies so heavily on data collection that emphasis on its importance is not required amongst the team members. For post-installation monitoring and maintenance, part of the ROI for every project is the reduced future operational expenses. Upgrades are monitored and maintained to ensure continued optimal performance and expense control.
What lessons has the organization learned related to maintenance and engineering about upgrade planning and performance?
Walinski: Tracking and documenting lower operational costs for past projects is critical to earning funding for future projects. Savings associated with upgrades are tracked and referenced to show how perpetual and cumulative savings reduce the company’s expenses and to validate the projects’ originally proposed ROI and internal return on investment. Using proper measurement and verification and having data available from the continued tracking of performance and savings are critical elements to the team’s ability to secure funding and prove value.
Harubin: My recommendation is to question the engineering, especially from people who benefit from the project going in. Do everything you can. Look at similar projects that were done. Does the project really return the savings that it shows on paper? What you’ll find is that a utility will agree to something and they trust, to some degree, the engineering, but it won’t come true in the field.
What is your organization’s next planned energy-efficiency upgrade?
Harubin: I’m looking at another couple hundred thousand dollars for replacement of existing digital controls. That will get me a lot closer than I was a couple of years ago to where I need to be. But I have to bundle that one because those don’t have paybacks under four years. So I’m bundling it with steam-valve and trap replacements, which has a payback of four months. The savings is half a million dollars over 15 years. I was amazed by the loss from steam traps and valves.
Lanzilotta: We are working on a project that will upgrade our exterior lighting to LED technology with an advanced wireless management system. The system will monitor fixture performance and operating conditions and execute commands based on inputs, such as schedules and daylight levels. In the event of a failure, our maintenance department will be notified in real-time (as to) the pole number and location. The payback is longer than we’d like, but the reduced operational and maintenance costs in conjunction with safety enhancements make it a desirable project.
Walinski: The next major project being researched for the company is to potentially add natural gas pre-heats to improve the ability to maintain comfortable temperatures in winter, reduce operational expenses, and reduce indirect energy use.
Related Topics: