Measure Motor Shaft Voltage
For Predictive Maintenance, Fewer Repairs
By Adam Willwerth
Variable frequency drives (VFDs) can save 20-30% in energy costs. Because of this, they have been cited as a key technology for those wishing to make their commercial HVAC systems, automated assembly lines, and other processes more energy-efficient. But, whether used to control a motor’s speed or torque, a VFD induces currents that can damage bearings. The costly repair or replacement of a failed motor can wipe out any savings that a VFD yields and severely diminish the reliability of an entire system.
The Threat
For years, the true cause of VFD-induced bearing failure was often misdiagnosed. Eventually, repair shops and testing consultants proved that the high peak voltages, fast voltage rise times, non-sinusoidal shaft currents, and parasitic capacitance associated with typical pulse-width-modulated VFDs lead to the cumulative erosion of bearings. Without mitigation, voltages repeatedly build up on the motor shaft to a certain threshold, then discharge in short bursts along the path of least resistance, which all too often runs through the motor’s bearings.
The discharge rate tends to increase with carrier frequency, but continued discharges result in the pitting of the balls and race walls through electrical discharge machining (EDM). Concentrated pitting at regular intervals along the race wall can cause washboard-like ridges called fluting, a source of vibration and noise. By the time such damage can be heard, bearing failure is often imminent.
Confirming the Threat
To confirm the threat of bearing damage in order to head off motor failure and system downtime, Electro Static Technology (EST) has introduced the new AEGIS™ Shaft Voltage Test Kit. The kit contains a voltage probe, a special probe tip, an extension rod, and a portable oscilloscope — everything a maintenance person, consultant, or motor repair shop needs to measure the stray currents on a motor’s shaft. One kit can test every VFD-controlled motor in an entire plant, office building, or other facility. The AEGIS™ Shaft Voltage Test Kit is the result of collaboration between EST and Fluke Corporation. Its accuracy is due in part to the special tip containing conductive microfibers. EST makes the tip and extension rod, while Fluke makes the probe itself and a portable oscilloscope that displays the readings.
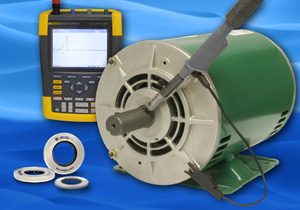 The AEGIS™ Shaft Voltage Test Kit measures induced voltages on motor shafts for predictive maintenance. | |
The probe is a handy tool for maintenance/testing personnel — anyone who needs to determine and convince others that shaft voltages either are or are not present at levels high enough to harm bearings.
If shaft voltages are found, a reliable method of bearing protection is required to make VFD-driven systems sustainable as well as energy-efficient. Ironically, some products designed to protect bearings from electrical damage require extensive maintenance themselves. Conventional spring-pressure grounding brushes, for example, are meant to provide a path to ground through contact with the motor shaft, but current through these brushes is easily interrupted by contamination. Because they corrode and become clogged with debris, the brushes require regular maintenance and wear out quickly. Certain carbon-block (graphite) brushes are susceptible to “hotspotting,” in which an arc briefly fuses the brush to the motor shaft. Additionally, carbon-block and metal grounding brushes do not work as well as grounding rings at high rpms.
Other bearing damage mitigation products, such as insulated or ceramic bearings, can shift damage to connected equipment. And, many so-called “inverter-duty” motors offer beefed-up winding insulation that does nothing to guard against bearing damage. If they are to be truly ready for use with VFDs, these motors still need bearing protection.
If the Test Kit confirms the presence of damaging shaft voltages, installing AEGIS™ Shaft Grounding Rings will provide long-term protection of bearings from electrical damage. | |
Disarming the Threat
The most effective bearing-protection device is a grounding ring that uses advanced electron transport technology to boost the electron transfer rate and safely redirect shaft currents from shaft to ground, bypassing the bearings entirely. Developed by EST, the AEGIS™ SGR Bearing Protection Ring can be installed by a motor manufacturer or retrofitted later.
In fact, the maintenance-free ring has already proven itself to be the most effective, reliable, and universally applicable solution to date. Available for any NEMA or IEC motor regardless of shaft size or horsepower, it has been successfully applied to HVAC systems, pumps, power generators, gas turbines, AC traction motors, brake motors, and a long list of other industrial and commercial applications.
Key to the AEGIS™ ring’s success are the patented conductive microfibers that are arranged along the entire inner circumference of the ring in two rows that completely surround the motor shaft. Secured in the ring’s patented FiberLock™ channel, these fibers can flex without breaking, and the deep protective channel keeps them away from dust, liquids, and other debris. Tests of the ring on multiple motors show surface wear of less than 0.001” per 10,000 hours of continuous operation and no fiber breakage after 2 million direction reversals.
As preventive maintenance for motors already in service, the ring can be easily installed on any NEMA or IEC motor regardless of shaft size, horsepower, or end-bell protrusion using conducive epoxy and/or a new Universal Mounting Kit. Once installed, the ring requires no maintenance and lasts for the life of the motor, regardless of rpm. Installed on a VFD-controlled motor, it qualifies as sustainable technology under the Federal Energy Management Program.
Savvy Specifying
All VFD-driven motors are vulnerable to electrical bearing damage, and many companies now take a pro-active approach to protecting them, specifying new motors that are already equipped with bearing protection rings. For retrofits, the AEGIS™ Shaft Voltage Test Kit makes it easier than ever to prove the need to any “doubters” who make decisions on mitigating measures.
By diverting bearing currents safely to ground, AEGIS™ SGR Bearing Protection Rings extend motor life and thus ensure the reliable, long-term operation of VFD-driven motor systems, locking in energy savings to make these systems sustainable and truly “green.” And the AEGIS™ Shaft Voltage Test Kit helps prove the need for these AEGIS™ rings.
Adam Willwerth is Marketing Manager for Electro Static Technology, 31 Winterbrook Road, Mechanic Falls, ME 04256-5724, TEL: (207) 998-5140, FAX: (207) 998-5143,
www.est-aegis.com.
Information courtesy of Electro Static Technology
|