Northwestern Mutual
Scott Wollenzien Leads $500M Northwestern Mutual Renovation
Northwestern Mutual’s Scott Wollenzien oversaw construction of the company’s signature facility in 2017. Now he’s back for more.
By Dan Hounsell, Senior Editor
Once-in-a-lifetime moments are usually just that — singular, memorable events that do not come around again. For Scott Wollenzien, once in a lifetime apparently was not enough.
Wollenzien is senior director of facility construction and operations for Northwestern Mutual, a financial services provider headquartered in Milwaukee with two other corporate campuses. In his role, Wollenzien oversaw the design and management of the company’s Tower and Commons construction project, a 32-story, 1.1-million-square foot development that opened in August 2017 and reshaped the city’s skyline.
Now, Wollenzien is taking on another big-ticket, high-profile project. He will oversee the company’s recently announced North Office Building modernization, a $500 million renovation and upgrade designed to visually complement the Tower and Commons building.
“I've been fortunate to have many unique experiences with some of the construction projects, including the fact that I thought the Tower and Commons was a once-in-a-lifetime type of project,” Wollenzien says. “I'm fortunate to say that I have now a second once-in-a-lifetime project working on the new North Office Building modernization project.”
High-level teamwork
Wollenzien’s role in the construction of Northwestern Mutual’s 32-story Tower and Commons planning and construction from 2013 to 2017 involved a range of design and project management duties.
“I was the owner's rep working alongside of our general contractors and architects," he says. “This allowed me to work not only closely with them but also the general contractor, as well as many of the other trades representing Northwestern Mutual and the decisions that were needed to make that happen.”
Working closely with so many parties involved in the project taught Wollenzien that such complex projects have the best chance to succeed when those parties work together efficiently.
"When you have the right team assembled with the right expertise on it, you can accomplish almost anything,” he says. “It takes a whole team and expertise in a variety of different disciplines to build a world-class facility like ours.”
The teamwork approach does not end with the construction.
“Once the building is built, it takes a team of experts to help keep it maintained and running efficiently and successfully every day,” he says. “We're fortunate not only to start with the expertise that we had on hand. We've been able to grow the expertise in house so that many of our team members helped maintain the facility.”
The 1.1 million square foot Tower and Commons is almost double the size of the previous building, which had 600,000 square feet, Wollenzien says. The structure requires an expanded set of skills to maintain and operate. The impact has been especially important on building automation technicians, who must stay up to date on advances in system technology.
"As time goes on and as systems evolve, it takes more of a combination of people or a hybrid type role that bridges the gap between HVAC and technology or electrical and technology,” Wollenzien says.
To address the evolving skills required to maintain and operate the new building, Wollenzien developed a five-step training program that includes classroom training, functional testing, system tuning and balancing, commissioning each system individually and a blackout test when the whole building is commissioned.
“Unlike most projects where training the technicians, mechanics and electrical staff is one of the last things to do in closing out the project and is only done once, our program allows the team to see the systems in action at least five times,” he says.
Challenges and solutions
Wollenzien’s toughest challenge overseeing the Tower and Commons project did not involve the construction itself. Instead, it involved taking down the previous structure.
"We had to be careful when we took down the existing building because it was a circa 1977 building connected to the rest of the campus," he says. “When we disconnect this wire at this point, what else are we going to be affecting? Some of those systems control the data center, and we certainly didn't want to adversely affect it.”
The challenge required tapping into technicians' skills and experiences maintaining the previous building, using a methodical approach to its deconstruction and again ensuring the workers functioned as a team.
"We were taking our time and really diving into understanding what was feeding what in terms of electrical, what was feeding what in terms of plumbing, and making sure that every step we took was very well coordinated with our internal subject matter experts (and) making sure that we didn't adversely affect something else,” he says. “The coordination of disconnecting and then reconnecting were two very important milestones.”
The project also required that designers and architects work with an energy consultant to consider the impact of the facility and its glass facade on energy efficiency, as well as on the surrounding buildings and community.
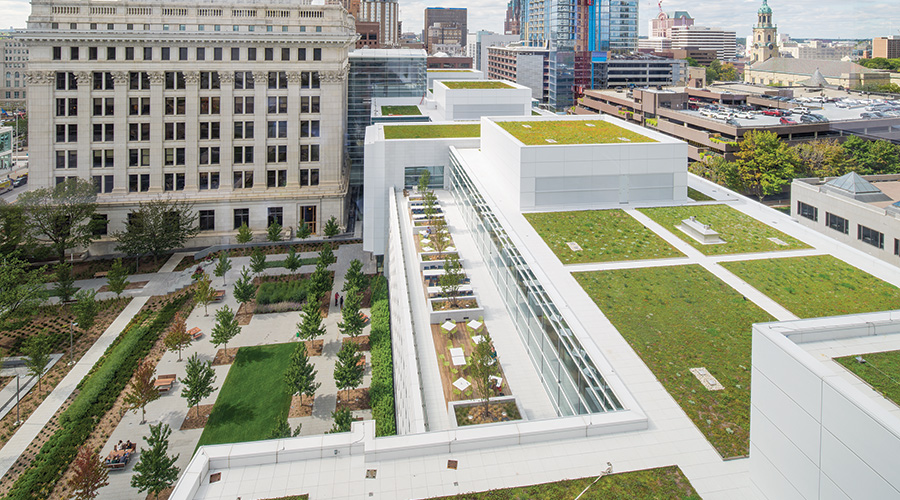
"The research included 100-year weather patterns, wind patterns and seasonal patterns to inform the development of a predictive energy model,” Wollenzien says. “For example, the model helped us design the proper curtain wall for our facility so that it reflects just enough light in the summer to help us run very efficiently and in the winter, it absorbs enough of the sun’s rays to help with heating.”
As a result, the facility is showing a 20 percent greater energy efficiency than engineers originally estimated.
“That speaks to the experts we had working on the job designing the facility, but it also speaks to the fact that time was taken up front to make sure we understood how the glass curtain wall was going to perform both for all four seasons — how storms are going to affect the building in terms of wind, how the sun's energy and the glare would be refocused not only for our employees inside the building, but for people outside the building and driving by the building,” Wollenzien says.
A second chance
The upcoming North Office Building modernization project includes a full-building renovation that is designed to visually complement the Tower and Commons building. It also marks an expanded role for Wollenzien compared to his role in the previous project.
“What is the most fun is that I'm using what I learned in the Tower and Commons project and helping provide key insights and experience to the project team on the new North Office Building modernization.
“It is a little bit different this time around. I'm one of the project sponsors, where I was more of a project manager and owners rep last time, with accountability for helping make sure the project stays on scope, schedule and budget.”
The updated role also calls for Wollenzien to keep in closer touch with Northwestern Mutual’s top executives — a critical responsibility given that organizations now pay more attention than ever to their facilities’ impact on energy efficiency, sustainability, resilience and connection to organizations’ mission and goals.
"I also help make sure that the executive leadership stays current on where the project is in current state and engaging them at the right times with decisions that need to be either escalated or decided, as well as to get their input and point of view on whatever it is that needs to be decided at the time,” he says. “There are thousands and thousands of decisions that happen on any one project like this, so it's important to have that synergy between what's happening on the site and what leadership understands.”
Career considerations
The Tower and Commons construction project and the North Office Building modernization have enabled Wollenzien to use the full range of skills and experiences he has developed during his career with Northwestern Mutual, acareer of accomplishments that earned him a 2024 Facility Champion Award from FacilitiesNet. He joined the company in 2002 as a corporate sourcing consultant, but he does not view his career in facilities management as starting on a particular date.
"It occurs over a period of time,” he says. “It's not a point in time that you can say, all right, I graduated from school, and now I'm a facility manager. There's a lot more to it than that. For somebody new getting into facilities management, there's a lot of knowledge that has to be built up over time, and you learn by doing. You learn by understanding what other people's experiences have been. You learn by networking, and it's a culmination of all those practices over a period of time.”
As Wollenzien described in ensuring the strength of the team involved in planning and executing the construction of the Tower and Commons, successful facilities managers demonstrate the ability to build effective teams.
“My toughest challenges have been not only putting people in the right places but helping build a succession plan,” he says. “The challenge comes in finding the expertise that you need when you need it.
“There have been a lot of retirements and people leaving the profession taking a lot of legacy knowledge with them. How do you replace that legacy knowledge easily and efficiently? How do you pass that on to the next person in line? How do you go to the street and hire it out? That doesn't happen overnight."
The myriad challenges related to staffing facilities departments include the profession-wide problem with locating, hiring and retaining entry-level technicians to replace a generation of older technicians who are leaving the profession.
“It's very difficult to find that knowledge and expertise on the street, so we ended up building our own,” Wollenzien says. “I've known for a long time, based on my experience of over 25 years in the in the business, that we would continue to see challenges and finding good talent and skill traits.”
He partnered with Northwestern Mutual’s human resources department, Wisconsin’s Department of Workforce Development and the Milwaukee Area Technical College to develop an apprenticeship program.
“You get a series of college classes that you have to participate in and be able to accomplish, and you have hands-on time,” he says. “Depending upon the skilled trade that we're talking about, that could be as many as 8,000 hours of hands-on time.”
In the last 13 years, the program has graduated more than 11 certified journey workers in key trades, including electrical, HVAC, building automation and painting. The program also is reaching into local high schools to identify and recruit students and introduce them to the opportunities and possibilities available in the skilled trades.
“In recent years, we expanded this program to include a youth apprenticeship program, which seeks out juniors and seniors in high school,” he says. “It helps get not only get their interest in the trades. We also have them start learning and putting in up to 900 hours against our 8,000-hour quota that they need in order to graduate and be certified from the program.
“They spend two weeks in each of those specific areas — HVAC, electrical, building automation, aircraft mechanic, painting, carpentry, locksmithing — to really help them understand what a career could be in the skilled trades.”
The apprenticeship program fits well into a career that Wollenzien says has increasingly come to incorporate building strong relationships and fostering teamwork.
“As I have grown into the profession, I’ve learned to appreciate the network of friends and partners I have developed in the industry,” Wollenzien says. “In the beginning, I tried to do a lot of things independently and struggled occasionally with outcomes that weren’t quite right.
“If I had leaned into my network, I would have probably avoided some of the pitfalls and would have accomplished a number of projects easier, faster, and at a lower overall cost. Your network is an important resource, don’t be afraid to use it.”
Dan Hounsell is senior editor for the facilities market. He has more than 30 years of experience writing about facilities maintenance, engineering and management.
Related Topics: