« Back to Facilities Management Building Automation Category Home
Why Building Automation Is Not as Smart as You Think
February 28, 2018
- Building Automation
By Connell McGill
Will automation through the Building Management System (BMS) lead to "smart" buildings and improved performance? It might seem logical to assume that's a valid assumption. It is true that a building with a properly programmed BMS will run more efficiently and have a healthier indoor environment than a building without any controls. However, the programming and adjustment of these systems still depend on persistent diligence of a human operator. But how many operators, quite frankly, enjoy learning about and tweaking their BMS? That's a rare quality in any human being.
The ability of equipment to be turned on, ramped up, or ramped down automatically based on specific set points allows for a response to conditions that no human could achieve at scale with manual operation. Obviously, there is tremendous value in a BMS, and it can be an invaluable tool to reduce costs.
On the other hand, the Department of Energy found that improperly configured building management systems result in 20 percent of building energy usage. For a system that costs around $2.30 per square foot to implement, the costs associated with non-optimal automation can negate any improvements in building performance.
What's Your Schedule?
Setting and executing equipment schedules are basic functions of a BMS, but mistakes are made surprisingly often.
If schedules were always wrong, it would be an easy problem to solve — simply get rid of schedules. The issue is that an operator does not know a schedule is off unless they check or unless a tenant complains, and each schedule may drift away from prescribed setpoints over time as seasons or occupancy patterns change.
This is the risk of completely depending on automation without a method to verify effectiveness. (The problem is not limited to the BMS; it is inherent to all software-based automation, as an article in The Atlantic recently noted.) Schedules may accidentally be changed when maintenance needs to be performed and schedules or set points are never changed back to original settings. Additionally, operators may sometimes be unnecessarily conservative to ensure that tenants remain comfortable, such as when setting wider temperature bands and extending startup and shutdown hours.
It would be surprising to find a real estate portfolio without any scheduling issues, despite the significant dollars wasted as a result. In the example below, changing the lighting schedule from nearly always on (represented by the grey line) to reflect real occupancy hours (represented by the blue line) saved one commercial building 57 percent of their lighting costs, or $24,000 a year.
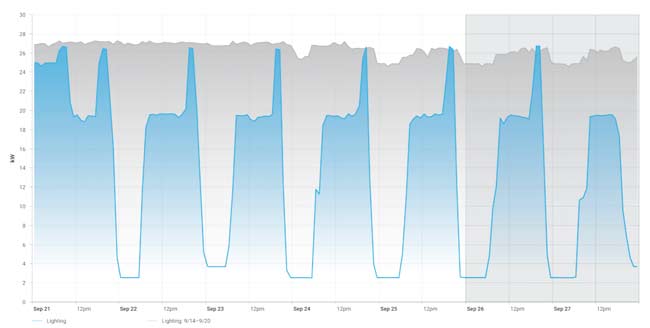
Clearly, in this case, automation did not guarantee efficient operations as an intelligent system should otherwise be able to achieve.
Making the Right Adjustments
BMS installation includes a process of tuning (commissioning) the system to the maximum efficiency for conditions at the time of installation. However, there is generally no mechanism to account for the changes that a building experiences over time. Tenants, building staff, climate, and maintenance needs all change over the lifetime of a building. So while optimization at installation is important (and difficult — just ask any building operator), ongoing optimization is equally, if not more, important.
A key problem lies in tracking the adjustments. If a setpoint is changed, there's usually no record of that change. Ideally, there would be a measure of equipment performance before a change, an exact record of that change, and a re-evaluation of the effects of that change in the future. In practice, this is rarely the case.
Another problem is the complexity of building operations and human limitations in being able to account for all environmental/human variables occurring at once. For example, hot/cold complaints from tenants may lead building operators to adjust the set points of HVAC equipment. However, air temperature is only one of the factors that affect occupants' perception of temperature. Humidity is at least as important, together with air movement, and the radiant heat balance. If the A/C is blasting, but internal humidity is high, people will feel like they are working in a refrigerator.
While the equipment needed to change humidity levels separate from cooling are expensive and almost never installed at the commercial level, it's an important aspect to consider. If setpoints are lowered or raised as a reaction, there may be higher costs without directly solving the problem.
Performance Drift
Even if a building is perfectly programmed, performance is going to drift away from optimal functionality by 10 to 30 percent over the life of the equipment. Tenants and operators tweak thermostats, leave equipment on, and make setpoint adjustments. These unnecessary switches and strains reduce the useful life of equipment. In addition, equipment degradation and other factors such as clogged filters are inevitable causes of performance drift. It would seem like this is an unavoidable outcome of equipment operations in buildings.
Most building management systems provide no mechanism to combat this drift. Even in the systems that provide fault detection and diagnostics (FDD), performance drift often goes undetected. Since the rules/alarms can't "learn" without human engineers programming the software manually, the building doesn't tend to get more efficient over time.
Another thing to consider is that many pieces of equipment show signs of degradation before absolute failure occurs. While some signs of a performance drop may be detected during preventive maintenance rounds, software is much more efficient at detecting the barely detectable. While the BMS may have the data, its software is focused on controlling specified setpoints, not on performance optimization.
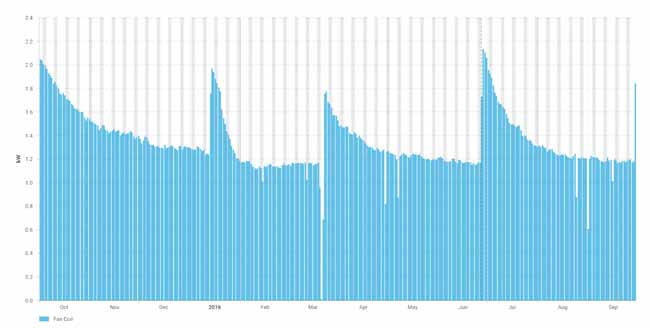
Don't Forget About the People
So far, we have covered some ways in which automation, while important, is not sufficient for optimal building performance. The overarching issue is that human involvement in the parameters through which automation is executed is susceptible to mistakes.
The performance of the BMS is only as good as the programmer in the field and their knowledge of the individual building. Even with an in-depth knowledge of how a building operates, it is difficult to manually program such complexity into a consistent sequence of rules, especially when the rules change. Because of changes in weather, occupancy, use, and configuration, the optimal settings for one day are likely to be different the next day.
Even experienced operators, who have so much skill and experience with a building that they can sense problems and their underlying root cause, often fail to optimize building automation systems. Manual, consistent optimization of a building is hard.
Other than programming and adjustments, the vast quantities of data produced by a typical BMS and the data mining necessary to verify effectiveness is a costly process. The engineering effort needed to glean insights from BMS controls is often antithetical to reducing operating costs.
The time necessary to get full buy-in, implement a series of logic, and mine the data ultimately leads to a long, expensive roll-out. This does not even factor in the management time necessary to acquire full buy-in to the system and train operators on the system components.
The alternative is contracting additional BMS optimization vendors for HVAC, water, and lighting. The focused nature of these solutions can cut into any cost reductions via equipment optimization.
What's the Alternative?
While highly complex, the behavior of building equipment is far from random. Building performance reacts to the weather and occupancy hours in predictable ways. These conditions, along with equipment runtime and the indoor environments, can become recognized and simplified with analytics.
The complication arises when these conditions are overlaid, ever-changing, and interactive with one another. As a result, there isn't a prescriptive solution that can be applied to every building. This is where recent advances in machine learning are stepping in to make buildings truly intelligent.
Machine learning can use dynamic pattern recognition to convert otherwise overwhelming amounts of data from thousands of data streams into specific, actionable insights. Coupled with more intuitive visualizations than BMSs are designed to provide, operators can gain real transparency into the effects of their daily decisions, fight performance degradation, and achieve peak performance.
By decentralizing data and human decision making, a significantly more robust building system can be implemented. This supplemental building monitoring system focused entirely on optimization ensures that the greatest costs of equipment — ongoing operating costs - are as low as possible for the equipment lifespan. Humans still have to perform functions that machines cannot. For the foreseeable future, it will be up to the on-site operator to implement the suggested adjustments and fix the malfunctions identified by machines.
As buildings become smarter and more complex (as if they weren't already complex), it is important that we don't just put a new paint job on a car that desperately needs a new engine. We should keep in mind that automation alone is not intelligence, it is simply a tool. The real intelligence lies in our ability to collect these diverse data sets, leverage machine learning to discover patterns that would otherwise be impossible to discover, and visualize the results in a way that humans can understand and act upon.
Connell McGill is the CEO and cofounder of Enertiv, which provides a submetering and IoT platform that maximizes tenant comfort and reduces maintenance and energy-related operating costs in commercial real estate portfolios.