Fault Detection and Diagnostics: How To Find Energy-Wasting Problems
Here's what an FDD system is and is not, what it can and cannot do, and how it can save you time and money.
In an effort to save energy, reduce maintenance costs, and leverage investments in existing building management system, more and more facility managers are beginning to research — and deploy — fault detection and diagnostics (FDD) software platforms in their facilities.
At a high level, FDD platforms consist of three major components: a way of acquiring data, a set of algorithms for processing it, and a means of displaying the results. If that sounds similar to a building automation system, don’t be surprised: Most FDD systems are designed as add-ons to an existing building management system, though some standalone platforms do exist. The difference is that, while modern BAS collect and store vast volumes of data, creating actionable results from that data is a time-consuming and difficult task. As anyone who has spent hours poring over building trend charts trying to figure out why they always get a particular alarm at 2 a.m. can tell you, this is a task worth automating. But to really save time and money, FDD systems must accurately identify real problems and provide an easily digestible idea of how to resolve it, if not an outright diagnosis. Getting it right is no easy task.
The 411 on FDD
As with many cutting-edge software products, however, not everyone means the same thing when they talk about FDD. Generalizations are difficult, as even a single vendor’s FDD product is often infinitely configurable. Like most building controls technology, FDD software originated in the industrial space. Such systems were initially conceived as a way to combine large volumes of equipment-level data and operator experience to keep critical equipment in peak condition. Decades later, the proliferation of cheap sensors and control hardware, cloud-based storage, and standardized communication protocols has opened up the possibility of implementing FDD in facilities of all types. But it is still a fledgling technology, and no two software platforms are identical.
At worst, FDD software may be nothing more than a fancy way to create alarms and trend plots, albeit with much more functionality than is built into most BAS. Trending features can include plotting multiple time series of overlapped data, which may help determine the causes and effects of a problem by plotting one BAS point as a function of another, or plotting a mathematical expression based on multiple BMS points. An operator may, for example, create an expression for the temperature differential (delta T) of a condenser water loop, and plot it against outdoor temperature. The temperature at which it crossed the X-axis would be a good candidate for the setpoint at which the cooling tower is enabled, and outliers from the generally linear trend could be investigated, possibly leading to the identification of equipment that’s cooling when it shouldn’t be.
More complex alarms based on logical combinations of points or math expressions may also be defined. Some even allow statistical methods, such as alarming when a point is outside one or two standard deviations from its historical value. Though priority-based alarm notification is now a common feature of many BAS, FDD systems also offer the capability of grouping alarms and taking different actions based on severity — e.g., a space that’s off its setpoint might just trigger an email, but a chiller failure could result in a call to staff or a service contractor. While advanced alarming and trending are core capabilities of a FDD platform, they may not by themselves deliver much more value than the underlying BAS. FDD with only those features may not be worth the additional investment.
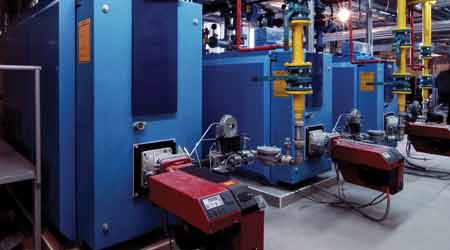
(Fault detection and diagnostics platforms can be a boon both to complex building water and air systems and to simple equipment that doesn’t
receive much attention.)
Best of breed
True FDD systems attempt to detect and diagnose equipment failures by applying a sophisticated rule-base — what a computer scientist would call an “expert system.” Such a rule-base contains both general knowledge (“there should be little to no flow in a chilled water loop if the chilled water pump is off”) and knowledge specific to the facility in which it is deployed (“the chilled water loop delta T should never be greater than 12 degrees F or less than 4 degrees F”). From this embodied knowledge the system can make sophisticated deductions. Some FDD platforms come with this rule-base predefined and uneditable. Others allow users to modify or add to it, though often with a steep learning curve.
Consider, for example, a typical commercial office variable air volume system with a single VAV air handler and a number of different zones on multiple floors. Such a system might have 50 or more VAV boxes. A FDD might have a rule that “at least one VAV box damper should always be greater than or equal to 95 percent open during occupied hours.” If the FDD also “knew” that the air handler was configured to reset the supply air static pressure setpoint, it would conclude that there was a problem with the system — perhaps the supply fan was in manual mode or the setpoint had been overridden. Some FDD software goes as far as estimating the energy costs of uncorrected faults, tracking the number of kilowatt-hours wasted and helping facility managers prioritize the problems that are being identified.
These types of diagnostics can be a boon to simple equipment that doesn’t receive much attention, as well as for complex air and water systems. FDD might detect that a domestic water booster pump motor had gone from starting six times per hour to 20 times per hour, and discern that the cause was likely a failed discharge pressure switch or pressure tank diaphragm. If the pump skid were located in a little-traveled corner of the basement (as is often the case), that fault could go undetected for months — significantly shortening the life of the pump motor.
Related Topics: