Smart Buildings: How to Justify an Investment in Analytics Software
By combining fault detection and diagnostics, monitoring-based commissioning, and building analytics, facility managers can understand their digital data and, therefore, what really is happening in buildings.
Things break and people are uncomfortable: the two unconditional truths of managing a building. It’s hard to imagine a facility manager’s job otherwise. Unfortunately, the reality is that keeping a building running and occupants comfortable is an uphill battle. However, the tools used to fight it have become much more advanced in the past couple years. Indeed, new technology has completely changed the way facility managers are approaching these age-old challenges. But before examining that new technology, let’s dive into the root-cause of most issues in a building, when things break.
Identifying the root-cause of operational issues is difficult and time consuming. Quick example: Identify all the operational problems going on with air handling unit represented with the DDC points list below. For clarity, this is a VAV air-handling unit with a hot water preheat coil and chilled water-cooling coil, serving critical lab space.
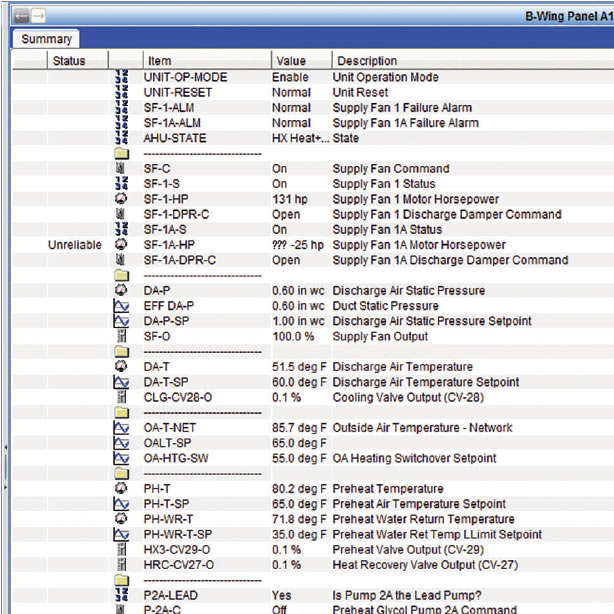
(This DDC points list shows that the chilled water valve is stuck open, causing the discharge air temperature to drop far below setpoint. Many problems go unrecognized because it is so difficult to find them.)
Answer: The chilled water valve is stuck open, causing the discharge air temperature to drop far below setpoint. The static pressure is below setpoint while the fan command is 100 percent. One fan is either off or possibly has failed, or the power meter is broken. The fan status current transducer may or may not be working, depending on the actual problem.
However, the most shocking part of this example is not that this air handling unit has a few issues. Walk into most facilities and you will find a few similar sights. This air handling unit had been running like this, certainly for days, potentially for weeks or months in a building with a 24-hour maintenance staff. But before you jump to judgement, let’s understand how these problems could get missed and remain uncorrected.
• There were no alarms on the building automation system. Take another look at the DDC points list. Air is being distributed to the space at 52 degrees. It may be at a lower pressure and temperature than what the equipment is trying to do, but not by enough to trigger any alarms.
• There were no occupant complaints. This air is being fed to VAV boxes with reheat coils. Even if the discharge air temperature is lower than expected, it is being reheated before it is sent to the space. The space remained comfortable.
• The total number of points in this facility is more than 100 times what is shown on the DDC points list. This problem may seem obvious when only this screen is given to you. What if 100 similar screens were presented at the same time with only one having an issue? Would you be able to find the problem? Would you spend the time to find the problem?
The problem with problems
This is the core conundrum of facility maintenance: “Is the problem even worth finding?” The time and effort it takes to identify these problems cannot be understated. But even when a problem is found, there is so much still unknown. How much is this problem actually costing (energy, occupant comfort)? Who has the time, knowledge and skills necessary to fix the problem? What are the costs to fix the problem and who is going to pay for it?
Due to the high level of effort involved in identifying these operational issues and their true costs, many are left undiagnosed. It is usually only when these problems (stuck valves, broken dampers, uncalibrated sensors) become a real problem that they show up on the staff’s radar. Only when an occupant calls to complain that their space is too cold, and a days’ worth of investigation takes place, does the staff finally realize the cooling valve on the AHU has been stuck open.
Analytics change the game
Manually identifying these types of operational issues, whether during regular inspections, or reviewing the BAS, takes too much time. But is there an alternative? For a long time, the answer has been no. But recent commercial advances in data analytics for building systems have changed the game.
While it may take a human a long time to analyze hundreds of screens to find a pattern (i.e., the broken valve in the first example) it only takes a computer a few seconds.
Fault detection and diagnostics (FDD), monitoring-based commissioning (MBCx), and building analytics are all terms that have been used to describe this simple concept: using digital data to find what matters, and to do so cheaper, faster, and more reliably than previously possible.
Facility managers are using commercially available analytics software programs to improve the process of identifying and solving complex problems. Every facility is unique, and analytics can be used in a variety of different ways. The sidebar below shows how analytics are often implemented to improve energy efficiency, occupant comfort, or reduce maintenance time. These examples probably ring a few bells, but they certainly do not come close to describing the full scope of what’s possible. So how would you identify a good project for a facility? Ask some questions first.
• What are the top things that go wrong related to the mechanical/electrical systems in the facility? If you could have someone constantly watching this equipment through the BAS, and waiting for these issues to happen, would you be able to find the issues and correct them faster?
• Are the control sequences that govern the operation of the mechanical equipment in your facility so complicated that it’s hard to tell if the equipment is working correctly or not?
• Does your building use more energy than other buildings with similar characteristics? If so, is there any clear cause for the above average energy use?
If the answer to any of these questions is “yes,” there may be an opportunity to identify ways to improve the buildings operation by automatically identifying opportunities with data analytics.
Related Topics: