Allsteel
New Systems Furniture Helps Law Firm Burnish the Look of its Space
Having occupied the same space since 1986, Minneapolis law firm Meagher & Geer decided it was time to upgrade its space, which had expanded from a floor-and-a-half to two floors.
“There have been a lot of changes, especially with the way technology affects workspaces,” says Dave Steinhauser, executive director of the firm.
The goal of the upgrade was to update the firm’s image, give everyone access to daylight and open up the reception area. Steinhauser wanted a custom look, with lots of wood and an aesthetic appropriate for a law firm.
Equally important was simplifying the project by using one specification to outfit every office. Steinhauser visited several law offices and considered custom millwork before settling on the Align system from Allsteel.
The choice gave the law firm the flexibility and specification ease of systems furniture, along with the richness of wood they wanted and some important customization they required. “It combined the strength and advantages of steel with the look and appeal of wood,” says Steinhauser. “It offered clean lines and flexibility. ”
To give the firm a way to store the firm’s large red rope files so they would be both neat and accessible, the manufacturer increased the depth of the overhead cabinets and created a unique closed unit between administrative assistant stations.
After almost a year in the space, staff feedback on the new offices and seating has been highly positive. “If we had purchased custom-built furniture, I can only imagine the problems we would have experienced, so I am glad we changed direction,” Steinhauser says.
|
|
APC
Hospital Grows Data Centers Using Modular Power, Cooling
Sisters of Mercy Health System is the ninth—largest Catholic health care system in the U.S. Managing services in multiple locations calls for a dedicated IT team, a group that becomes even more critical as the organization becomes more IT-dependant.
Traditionally, IT had limited uses. But now the hospital uses IT to support processes such as digital imaging, prescription ordering and electronic medical records. The data center has become a key component to improving care delivery, patient safety and reducing costs. With the extra IT demand, Mercy wanted to implement an enterprise solution that would integrate and standardize its data center environments spread across several states and provide high availability and an N+1 fault-tolerant system, monitored 24x7.
One challenge was the management of increased power consumption and the requirement for increased cooling. The hospital needed to locate and implement an integrated hardware and software infrastructure solution that was both modular and flexible. At one of their primary data center locations for example, the hospital had exceeded its UPS capacity even though continued growth required more conditioned power. The hospital chose APC’s InfraStruXure on-demand architecture to provide additional UPS capacity and the ability to utilize available building power.
The company’s modular and flexible approach provided options to circumvent both UPS and floor height limitations, while the cooling architecture provided the hospital with five tons of predictable focused cooling per device. This also allowed the InRow cooling units where they were needed, says Bill Hodges, director of data center operations, Sisters of Mercy Health System.
“The alternative was to integrate multiple different vendor solutions without the guarantee of a seamless integrated solution,” says Hodges.
|
|
Armstrong
Pre-engineered Ceiling System Creates Clean Look, Improves Speech Privacy
Known for its renovations of older structures, Clemmons Architecture of St. Petersburg, Fla., decided to practice what it preached by relocating its offices to a building that dated to 1926.
While making the move, the firm also wanted to improve both the aesthetics of the space and speech privacy. After initially considering an open plenum look in the new space, the firm decided against it after removing the existing ceiling.
“As a result of both the fire safety and aesthetic issues, we decided a suspended ceiling would be the best choice,” says Greg Glenn, project manager.
Instead of a traditional 2-by-2-foot or 2-by-4-foot ceiling system, however, the firm chose a TechZone ceiling system from Armstrong. This pre-engineered acoustical ceiling organizes light fixtures, air diffusers and sprinkler heads in a narrow 6-inch-wide linear “zone” that coordinates visually with large-scale ceiling panels. The result is a ceiling that is clean, contemporary and uncluttered.
Employees have responded favorably to the new ceiling, and the firm now recommends it to customers, Glenn says.
“Our old offices had a lot of hard surfaces, including a drywall ceiling, so there was not much accoustical privacy,” he says. “The new ceiling makes a big difference, both in terms of privacy and the overall noise level. Compared to our old offices, there is far less distraction now.”
|
|
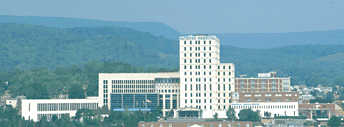
ASCO Power
Transfer Switches Help Hospital Improve Control, Shed Peak Demand
Altoona Hospital in Pennsylvania wanted more precise control of its emergency power system so it could participate in a utility load curtailment program and reduce its utility bills.
Adding ASCO power transfer switches and power control systems to manage the doubling of on-site generator capacity enabled the hospital to shed load from the utility source during periods of peak demand.
To make the upgrade work, the hospital refurbished its two engine generators and installed two new ones. All four are rated at 900 kw capacity. Three satisfy the hospital’s entire load, including chillers, and the fourth serves as back up.
The upgraded system includes 28 ASCO low voltage and medium voltage power transfer switches and a power control system. The system enables the 346-bed hospital to respond within two hours when the utility requires it to shed load from the utility grid during peak load demand.
When the hospital needs to shed demand, staff start the generators and transfer the load from the chillers seamlessly using the closed transition transfer switches.
“There’s no break in power,” says Jim De Stefano, the hospital’s director of construction and design services. “People don’t even see it.”
The transfers are “invisible” because closed transition transfer switches eliminate momentary power interruptions by connecting with one power source before breaking with another. That also means patients don’t see transfers conducted during the hospital’s monthly testing procedures.
|
|
Automated Logic
New Control System Saves University $350,000 Annually
When Cornell University undertook a campuswide energy conservation initiative, the university’s Biotechnology Building was a natural target for an upgrade.
Built in 1986, the 150,000-square-foot, energy-intensive facility was still operating with its original pneumatic controls in occupied spaces and first generation DDC controls on the central system.
Cornell chose Automated Logic’s WebCTRL system based on prior experience with the system in other campus buildings. A total of 90 labs were outfitted with Phoenix Controls VAV fume hood sash position controls and venturi-style VAV boxes, digital room controllers, reheat valve transducers, room occupancy sensors and user-adjustable networked thermostats. Another 100 non-fume hood labs were retrofitted with box-mounted Automated Logic controls, room occupancy sensors, thermostats and reheat controls.
“Our control strategy was to minimize air change rate in the room to what was necessary to keep it comfortable and provide a safe working environment,” says Lanny Joyce, manager, engineering, planning and energy management.
The work has paid off. Reduced ventilation rates, combined with a program to educate occupants about energy savings and lab safety, have reduced annual energy costs by nearly $350,000.
“When we put the project together, we made estimates of our energy savings,” says Alan Hebert, project manager. “Our prediction at the time was about 30 percent annually. We’re very close to the 27 percent to 28 percent range, and we’ll probably exceed the 30 percent savings we had estimated.”
|
|
BASF Polyurethane Foam Enterprises
SPF Roof Simplifies New Roof Installation, Stands Up to Hurricane Rita
The idea of replacing the roof at the Bayne-Jones Army Community Hospital project at Fort Polk, La., posed some daunting challenges. Tearing off the old 125,000-square-foot built-up roof would disrupt patients and staff. Damaged and unusable solar collection units would have to be removed and the spaces they left filled in. And the Army made it clear it wanted an affordable, long-lasting roofing system.
The roof project was part of a massive renovation at the 65-year-old Army base. When it came time to replace the roof, the hospital selected a spray-applied polyurethane foam (SPF) roofing system, in part based on a partnership between the Army and Arizona State University’s Performance Based Studies Research Group (PBSRG), a non-profit program that aims to improve quality in the construction industry by helping owners select best-value contractors rather than the traditional lowest-cost bid.
The specially-engineered Elastospray Alpha SPF roofing system from BASF Polyurethane Foam Enterprises was chosen for the roof, based on a recommendation from the research group. Applying an inch and a half of polyurethane foam and Neogard Urethane Coating allowed the facility to keep functioning normally without major disruption. SPF is installed directly onto the existing substrate in most cases and conforms to any shape smoothly and seamlessly.
The Army base sees its share of severe weather. So far, the roof has held up admirably. A survey of the roof in the aftermath of Hurricane Rita found no leaks and no wind damage.
|
|
Butler
Metal Serves as an Efficient Envelope for Retail Store Operator
When owner Keith Harshbarger planned to build a new Ace Hardware store in Gridley, Calif., to replace his 100-year-old facility, California’s volatile energy costs were a major concern.
Harshbarger investigated several construction options before settling on a metal building from Butler Manufacturing Company.
The choice helped preserve profitability for Harshbarger by giving him the most energy-efficient building and shortening the construction schedule.
Butler supplied the complete structural system for the store with a fully integrated standing seam metal roof system. The roof assembly achieved an R-30 insulation rating using a method that infills the cavities between the primary structural members and applies double layers of fiberglass blanket insulation in runs perpendicular to each other above the framing. Thermal spacer blocks between the structural members and the seamed roof panels preserve uniformity in the insulation barrier.
The walls used the Koreteck® panelized building system. The 6-inch panels not only delivered thermal efficiency — R-24.8 — but were also installed in half the time of conventional methods, protected against the mold risk of cavity walls, and provided noise reduction and insect damage resistance.
Koreteck® is comprised of a 20-gauge steel core encapsulated in a monolith of PerformGuard™ expanded polystyrene insulation, providing a complete noncavity substrate ready to accept interior and exterior finishes.
“This building has lived up to my expectations,” Harshbarger says. “As for my utility bills, the air conditioners last summer seldom ran until 3 p.m.”
|
|
CertainTeed
Repeated Hurricane Damage Leads Louisiana School to Select Modified Bitumen Roof
When Hurricane Rita swept through Louisiana and destroyed the roof on Lawtell Elementary School, located in rural St. Landry Parish, the school lost its third roof in five years from a hurricane.
Deciding that it was time to invest in a roof that would outperform its predecessors, the school board selected CertainTeed to provide a modified bitumen roof.
The FRP-C-U2 two-ply modified roofing system consists of a double layer of roof insulation, with the company’s Ultra Poly SMS base sheet and Flintlastic Premium FR-P cap sheet — both thicker than the average bitumen membrane.
The system uses polyester base mats coated with modified asphalt, which the contractor felt would help meet International Building Code standards for the Gulf of Mexico hurricane coastline. The code states that roofs in the hurricane-prone Gulf Coast region must be able to withstand winds in excess of 100 miles per hour.
The design is also expected to hold up against the potential downward thrust generated by helicopter blades, which can put severe stress on the small temperature fissures in roof membranes and sometimes lift the membranes off the roof.
In addition, the cold-applied asphalt application method reduced the possibility of fires, injuries and other hazards that could otherwise have posed a danger had an open-flame torch or hot asphalt system been used at the elementary school.
Finished in July 2006, the roof has performed well so far, school officials say.
“When you lose a roof three times in five years, it’s time to look for an alternative,” says Claud Moody, Jr., assistant superintendent of operations for St. Landry Parish School district. “We have a lot of faith in this roof.”
|
|
Delta Controls
Consolidated Security System Simplifies Access for Tenants, Improves Control
To call the existing security measures at One Portland Square complicated would have been an understatement. Occupants who wanted to enter the 10-story, 200,000-square-foot building or a sister building had to deal with an outdated access control system for the perimeter doors, a stand-alone keypad-activated access control device in the stairs between floors and elevators, and manual keypad access for ground-level stairwells.
Employees had to carry an access card as well as memorize two different codes that changed frequently. Property managers knew they could do better. In upgrading the building’s security system, the goal was to replace the three older systems with one sophisticated, integrated system that allowed employees to use one card to gain access to all areas.
A state-of-the-art BACnet access control system from Delta Controls improved both scalability and user-friendliness. With the new system, the property management company no longer has to change codes with every employee change or track down stairwell keys from tenants and vendors. One access card now gives tenants full access to both buildings without requiring them to memorize different codes.
Control has improved as well. Property managers can isolate floors more readily and tailor access per employee by floor, by building, by time of day, or by day of the year. Finally, each employee card is programmed so that, during unoccupied times, tenants can gain access through the perimeter doors and elevators but are restricted only to floors that they are authorized to access.
“We now have more control of our security system and a significantly higher level of comfort in knowing that public access to our buildings is limited to those with specific authorization,” says Patricia Weimer, senior vice president of BCIA Portland Management Company.
|
|
Firestone
Repairs, Upgrades Extend Roof Life, Improve Efficiency at Convention Center
Located in the heart of downtown, the Albuquerque Convention Center has hosted major concerts and conventions for more than 15 years. The building’s EPDM roof system had performed well even after the original five-year warranty had expired. But some leaks had occurred on the 215,919-square-foot east roof section as a resultof lack of preventive maintenance.
Officials decided that repairing the existing system was the most cost-effective option. Firestone technical representatives inspected the roof and determined that with some minor repairs and upgrades, they could issue a new five-year Red Shield warranty.
Repairs included stripping the seams as needed, reinstalling the base tie-ins, replacing damaged sections of the roof with new 60-mil RubberGard EPDM and 2-inch ISO 95 insulation, repairing walls and curbs, repairing or reinstalling flashing, installing new walkways, wrapping six foot walls with EPDM and installing the manufacturer’s pre-finished metal coping.
The manufacturer’s AcryliTop was applied to the convention center’s roof membrane. It provides energy savings and protection on dark rooftops where temperatures can reach more than 180 degrees Fahrenheit.
The new roof will provide long-term energy savings to the city of Albuquerque. Additionally, repairing the roof rather than tearing it off saved labor and the cost of hauling more than 140,000 pounds of waste into the city’s landfill. It also eliminated thousands of dollars that would have been needed for diesel fuel and disposal fees. The savings amounted to nearly $1 million.
|
|
GAF
Upscale Hotel Calls for Comprehensive Roofing Solution
The Intercontinental Hotel and Conference Center in Atlanta, Ga., is divided into four separate buildings — a 22-story tower for guest rooms, a two-story retail building and two hotel ballrooms. The building’s upscale nature, combined with the fact that the guest tower would overlook the smaller buildings, called for a unique roofing design for each building.
The 12,000-square-foot ballroom complex is the largest in Atlanta. In designing the ballrooms, particular attention was paid to the aesthetic value of the ballrooms’ barrel vault roofs because of their high visibility from the guestroom tower. GAF Materials Corporation was chosen to supply the different roof systems required for the buildings.
A tan EverGuard TPO (60 mil) was chosen for the ballroom complex. The tan TPO is attractive from above, while the smooth roof surface has no penetrations for long-term durability.
The two-story retail building houses shops, a cafe and the hotel kitchen. With equipment on the roof, including air conditioning and kitchen vents, a built-up roof was chosen to provide the durability and watertightness. A four-ply built-up roof system was installed, and a ballasted roof with crushed gravel made it aesthetically pleasing when viewed from the guest-room tower.
Finally, a modified bitumen system was used on the guest tower to provide additional protection for the high-traffic areas that service various mechanical and window-washing equipment on the roof. The building height called for a modified bitumen cap sheet instead of a ballasted roof.
The hotel was also able to secure a 20-year Diamond Pledge warranty, which provides for coverage of all three roof systems under one warranty, and also covers material defects and workmanship errors.
|
|
Johnson Controls
New Jersey Health System Retrofits Facilities to Save Energy, Operational Costs
Despite a reputation as Northwestern New Jersey’s premier community health system, Saint Clare’s Health System entered the 21st Century in dire need of upgrades to operating systems and equipment.
“We realized that we had some of the oldest facilities in the state and that critical upgrades needed to be made,” says David Lundquist, chief operating officer.
With painful deficits in the 1990s, Saint Clare’s faced tough choices. It needed to upgrade facilities at minimal expense while setting the stage for long-term cost savings. Saint Clare’s chose Johnson Controls to help upgrade its facilities.
Saint Claire’s added the company’s Metasys building management system at all four of its hospitals. The system monitors thousands of climate zones using a complex network of sensors. It automatically regulates heating, cooling and air handling to maintain optimal comfort within every zone. It also regulates lighting, equipment cycle times and other systems based on occupancy and usage.
Other improvements included upgrades to central heating and cooling plants, new air handling systems, variable frequency drives, steam traps, energy efficiency lighting retrofits, vending misers and water conservation measures.
Saint Clare’s also worked with the company’s consultants to trim operational budgets, put in place key performance indicators and adopt facility improvement measures.
It also entered into a facilities services agreement that includes a performance contract guaranteeing energy and operational savings of $17 million over 15 years. The performance contact guarantees annual energy savings of $601,119. In year one, actual savings amounted to $1,084,867. Saint Clare’s also slashed greenhouse gas emissions by 4,931 tons.
“Our partnership has helped us create a safe and proactive health care environment in our hospitals,” says Lundquist.
|
|
MBCI Metal Roofing
School’s Metal Roof, Walls Win Over Community
When California’s Tulare City School District decided to construct the new Heritage Elementary School on an old dairy farm, administrators foresaw a school that would need to strongly represent the agricultural community.
Administrators, teachers, parents and the community were brought together to discuss the possibility of a school designed to reflect the agricultural history of the area while providing a modern educational environment. Reminiscent of barns, silos, sheds and windmill structures prevalent in the area, the design and materials are meant to integrate with the surrounding community.
The project consists of 24 classrooms, six kindergarten classrooms, a multipurpose building, an administration and media center building, and a windmill tower. Each classroom building consists of two units of four classrooms with the teacher’s workroom, counseling office, restrooms and other support facilities located between classroom units.
The project utilized 85,000 square feet of LokSeam SSR panel from MBCI Metal Roofing and 88,000 square feet of PBC panels on the walls and soffits. The 24-gauge Galvalume LokSeam panels were coated with Signature 300 Series paint (PVDF) in rustic red. The company’s PBC panels were Galvalume Plus. Twenty gauge material was used on the wall and 24-gauge on the soffit.
The use of metal roofing and galvanized corrugated metal siding provides a practical low maintenance exterior for the school. Residents have responded favorably to the design, which provides a stimulating educational environment, encourages social interaction, and has brought identity and pride to the community.
|
|
Meridian Systems
New Project Management System Saves Health Care System $4 million Annually
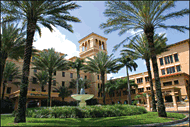
As the largest non-profit health care organization in the Miami-Dade region, Baptist Health South Florida (BHSF) has a thriving construction program. With six major hospitals and a variety of outpatient clinics, it’s not unusual for the system to be handling dozens of construction projects simultaneously, from a $50,000 floor renovation to a new hospital.
For years, project management consisted of paper-based processes, including Excel spreadsheets, Word documents and the manual routing of paper for approvals. It was a system that led to confusion and construction delays.
“Our manual system made communication difficult because it relied heavily on the construction management staff supplying up-to-date information and that didn’t always happen,” says Petter Melau, business technology consultant within BHSF’s IT group.
After significant research, BHSF purchased Proliance software, a solution from Meridian Systems that combines project and portfolio management, facilities management, business process management and business analytics.
ROI calculations played an important role in the selection, Melau says. While calculating the anticipated ROI of its software, BHSF discovered that lost opportunities associated with manual project management was costing the organization millions annually.
BHSF found that the new system compressed planning, design and approval schedules, standardized workflows, reduced cycle time, and improved efficiency
“The new software will save us close to $4 million a year in construction management costs,” says Melau. “That’s a pretty compelling ROI.”
|
|
Mitsubishi Electric
Hospital’s HVAC Upgrade Improves Patient Comfort
When the Rush Health Systems complex in Meridian, Miss., needed to expand over the years, the most common approach was to add onto the central four-pipe chilled water and boiler system.
“Over the past years, however, we have had increasing patient dissatisfaction with the temperature and comfort factor in our patient rooms,” says Fred Rogers, vice president, chief resource officer and facility manager.
In 2005, the facility, which includes a six-story professional office building, a five-story ambulatory surgery building and a two-story data center, embarked on a two-phase, multi-million dollar renovation of the third floor women services center, spanning four wings of the hospital.
Phase II included a new labor and delivery center and HVAC upgrades. Rogers needed a system to satisfy patients’ varying temperature preferences. He selected City Multi VRFZ (Variable Refrigerant Flow Zoning) technology from Mitsubishi Electric HVAC.
The system delivers personalized, zoned comfort to each room in the renovated women services center. It also automatically adjusts the compressor motor speed to react dynamically to outdoor temperatures.
Rogers plans to use the systems in the final two phases of this major renovation, which includes the C-section surgery suites, waiting rooms, doctor’s lounges and two wings housing 46 more patient rooms.
“The two-pipe system is going to save us money, and add capacity to the central system, and the variable frequency drive will provide much needed energy efficiency,” says Rogers. “However, the greatest pleasure is that the system is taking the load off the old chillers, which are huge energy hogs.”
|
|
Notifier
Fire Upgrade Uses Directional Sound to Reduce Evacuation Times
For nearly 80 years, The Seeing Eye in Morristown, N.J., has matched specially bred and trained seeing eye dogs with blind men and women from across North America.
Bud Liptak, director of facilities, faced a unique challenge when contemplating an upgrade to the school: finding an alternative to using traditional exit signs and egress markings.
While fire alarm systems today use audible and visual appliances to notify building occupants of an emergency, they cannot direct occupants to the nearest exit. But because persons with visual impairment — The Seeing Eye School’s primary clientele — are unable to follow exit markings or signage, traditional exit markings are rendered ineffective.
Liptak chose Notifier’s Onyx ExitPoint, which supplements visual exit markings with interactive auditory guidance to reduce evacuation times up to 75 percent.
The system uses varying tones and intensities to provide directional cues that don’t conflict with traditional devices such as horns and bells. It emits four different field-selectable sound pulse patterns to direct occupants to egress pathways and building exits.
“The system has been installed throughout our entire administration building, and has received nothing but favorable reviews from students, teachers, the administration and the local fire official,” says Liptak.
The system is currently in place on the main campus, but the ease of installation has led to plans to add it to one of the campus’s other buildings in downtown Morristown, according to Liptak.
|
|
Pella
Rain, Energy Concerns Create Window Design Challenge
The project team for the Burlington Apartments in the Pearl District in Portland, Ore. faced a challenge. The team needed a punch window system that could stand up to the Northwest’s rainy climate without water intrusion. And they needed to meet the developer’s energy efficiency requirements.
The team had initially considered an aluminum glazing system for the 10-story, 245,000-square-foot mixed-use building, in an effort to meet stringent AAMA 547 water infiltration testing, but it lacked the “Northwest Look.”
Pella’s natural wood interior and aluminum-clad exterior were selected to create upscale aesthetics and to ensure that the window system could pass the tough water infiltration test requirements. Also, having one window system for both the street-level storefront system and the apartment window units created a unified façade.
Because water intrusion was an enormous concern, the rainscreen system was designed so the brick cladding, exterior sealant, receptor and window form the rainscreen, while the integration of the weather-resistive barrier and interior seal serves as the air barrier. The air space between the two allows for pressure equalization. If water gets in at the head or jambs, it drops to the sill and exits via the subsill.
Another goal for the building was to meet the performance specifications for energy efficiency established in the Commercial Windows Initiative. One important measurement of a window’s performance is the U-factor. The U-factor represents a measure of heat loss through the entire window system, including the frame. The lower the number, the higher the insulating value of the glass.
The installed system has a U-factor of 0.35, (compared to .54 on the aluminum option) providing greater comfort and lower energy costs. The system also help reduce fading of storefront retail displays and interior furnishings.
|
|
Sika Sarnafil
Reflective Roof Exceeds California Title 24 Requirements, Earns Rebate
The Tiger Woods Foundation had two requirements for the Tiger Woods Learning Center in Anaheim, Calif. First and foremost, it had to be state-of-the-art. And so the learning center for students in grades 4 through 12 has 100 computer stations, a recording studio and a 1,200-square-foot multimedia center.
The other requirement? It had to be energy efficient, which means the learning center also has a white reflective EnergySmart roof from Sika Sarnafil. The single-ply system has a thermoplastic membrane, which is polyester-reinforced for high breaking and tearing strength. The white color reflects the sun’s rays, keeping the building cooler, which reduces air conditioning costs.
The potential to reduce energy costs, along with a good price to performance ratio, low maintenance costs and strong recommendations for the quality of the product led to the selection of the system. The membrane seams are hot-air welded, which means the membrane overlaps are fused together to form one continuous, monolithic membrane sheet.
Because the roof reduced energy consumption below California’s stringent Title 24, the utility offered a rebate to pay the cost of additional design features for the roof.
“The roof is not only energy efficient, but it also is as important a part of the building’s beauty as the meticulous landscape surrounding the site,” says Chris McGeady, project manager.
|
|
Schneider Electric
Power Monitoring System Helps College Save $2 million
With today’s larger university campuses operating almost as cities unto themselves, their energy and power needs have become more and more demanding. The need for reliability is paramount.
Part of the solution for San Diego State University (SDSU) is a cogeneration system that combines two combustion turbines capable of producing 5.2 megawatts each. Steam provides the campus’ heating and cooling, with the excess going into a generator to produce electricity.
But having the ability to generate power was only part of the puzzle. The campus also needed the ability to monitor and analyze energy use. SDSU chose Schneider Electric’s PowerLogic system for power management, power plant operation, billing information, event verification and troubleshooting.
Prior to the power monitoring system, SDSU was experiencing problems tied to the challenges of operating a campus application. Now, the facility department can monitor efficiency and troubleshoot problems quickly with direct access to real-time and historical data through a simple Internet connection, says Bill Lekas, who manages SDSU’s energy use.
The system also maintains the campus load. Lekas and his team are also able to monitor and control the frequency of the generated power, which can affect the performance of electronic devices, such as timing equipment. The power monitoring system is capable of monitoring all substations and 30 percent of the individual buildings on campus.
The system has reduced maintenance for SDSU and, combined with the cogen plant, saved $2 million last year compared to purchasing energy from the utility, Lekas says.
Because the school purchased priority technical support, it has access to the manufacturer’s PowerLogic University and local training. “And any improvements and enhancements to the products we purchased are installed automatically,” Lekas says.
|
|
SimplexGrinnell
Fire Protection Upgrade Protects Historic Luxury Resort Without Compromising Upscale Image
Upgrading the fire protection system at a five-star resort with 700 guest rooms in more than 30 buildings is no easy task. It’s particularly challenging when a tight deadline must be met while ensuring that the upgrade doesn’t interfere with historically significant building details.
When Terry McHale, director of facilities at The Broadmoor in Colorado Springs, Colo. needed to upgrade the fire protection system in 2001, he chose SimplexGrinnell, a business unit of Tyco Fire & Security.
The work had to be done during the six-month off-season. McHale worked with the company to establish a master plan for the upgrades and set priorities for the six-year project. Upgrades included installation of an early detection fire alarm system using fire alarm control panels as well as access control, video surveillance and intrusion detection systems in several buildings.
One phase involved a major renovation of the original six-story hotel. In the public areas, the company had to work around built-in plaster casting and friezes on the ceiling and artwork. McHale didn’t want unsightly devices, sprinkler heads or conduit destroying the artwork and architecture.
Other upgrades included a perimeter fence to funnel traffic through a main entrance, camera systems, proximity sensors, an upgraded command center that gives views from the more than 130 cameras across the entire property, and cabinetry that features ample equipment ventilation, flat panel screens and DVRs.
“Fine art, plaster casting and friezes on the ceiling all needed to be protected during construction,” says McHale. “The installers figured out a way to make it all work without disturbing the artwork. It came out just perfect.”
|
|
Sloan
Zero-water-consumption Urinals Win Over Custodial Staff
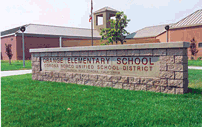
California school officials are no strangers to budgetary woes. So a rebate program from the local utility for installing zero-water-consumption urinals seemed like a natural opportunity for officials at the Corona-Norco Unified School District in Corona, Calif.
That’s not to say there weren’t skeptics. School custodians were concerned about how much time it would take to change the urinals’ cartridges, which filter sediment from urine before sending the remaining liquid down the drain.
To begin, the district, home to more than 45 schools near Los Angeles, started small — administrators decided to experiment with a few different brands before settling on Sloan.
“We first put the urinals in high-traffic areas in the gym and foyers because they get more use,” says Peter Normand, lead plumber, explaining that switching to the higher-use units would equate to greater savings.
Proper education about how to maintain the zero-water-consumption urinals, such as not dumping water down the fixtures, is important to their success, Normand says. Custodians should receive instructions on giving urinals a quick, daily wipe-down to keep them fresh and clean.
“Once custodians know how to use them, it saves them time,” says Normand.
When the first zero-water-consumption urinals were installed, the cartridges were changed regularly every few months. Now custodians simply watch the cartridges and replace them as needed, which helps extend the usage of cartridges installed in lesser-used restrooms.
“Cartridges last about three to four months near the gym and in other high-traffic restrooms and about six months in less-trafficked areas,” Normand says.
|
|
TAC
Building Management System Reduces Electric Bill, Keeps Vital Data Center Running
Headquartered near Dallas in Irving, Texas, Genpass Inc. is one of the fastest growing ATM and electronic fund transfer (EFT) processors in the country.
Making that growth possible is a 9,000-square-foot data center that lies at the heart of the company’s 79,000-square-foot corporate headquarters. The data center serves as the hub of all EFT transaction processing.
The computer systems in the data center must reside in a carefully controlled environment, because even the slightest changes in temperature or humidity can cause equipment failures that could bring down the network.
Genpass turned to TAC for an integrated building management system (BMS) solution. Operators use the BMS to monitor data center systems, including the HVAC units; power distribution units; the backup batteries, generator, and switch for the uninterruptible power supply system; the information distribution system, which drives the PCs and phones; and the leak detection system.
The system also provides general access permission for employees. Using the system, the facilities staff and security guards can monitor the doors, lock and unlock them as needed, and respond to door alarms.
“The system allows me to tie in multiple building functions and reduce my costs,” says Bill Lacava, vice president of enterprise networks for Genpass.
Since the installation of the Andover Continuum system, Genpass has reduced its monthly electrical bill by between $500 to $1,000 by being able to more closely monitor and adjust the environmental parameters in the data center.
“We are extremely happy with the functionality of the system,” says Lacava. “From adding card records to changing temperature set points, the system is easy to use, especially the Web interface.”
|
|
Tridium
Web-based Platform Slashes Hotel’s Energy Costs
With 643 rooms and suites, a variety of meeting facilities, a business center, state-of-the-art fitness center and multiple restaurants, Four Points by Sheraton Sydney is Australia’s largest contemporary hotel.
Staff wanted to reduce energy and operational costs, migrate to an open, Web-based enterprise platform, integrate all the building systems and improve guest comfort. Hotel management was also concerned about potential obsolesce of its legacy building controls systems and potentially being “locked-in” to one supplier. The hotel turned to Tridium to help design a hardware and software solution.
Specifically, the project called for an open platform with real-time, enterprise connectivity and an easy-to-use, Web IT portal with customized interfaces that integrated with the hotel’s existing building automation systems, Fidelio guest management system, lighting systems, paging systems and intelligent guest room control systems. A seamless interface was required for the maintenance management system and help desk. All systems had to interface with the company’s financial systems and Oracle database.
The Niagara Framework and Vykon Energy Suite were used to construct an open, Intranet Web portal that included application modules for controlling and managing all of the hotel’s lighting, guest management, help desk, security, maintenance energy, facility management and knowledge base systems.
After the installation, the hotel has cut its energy costs by more than 20 percent, improved workflow and resource management, improved control and management of the entire property, trimmed operational costs, reduced response time on maintenance issues and improved guest comfort, and is solving problems that are impacting revenue faster.
|
|