As CMMS collect and store more maintenance data, managers discuss strategies for using them to increase productivity and efficiency
OTHER PARTS OF THIS ARTICLEPt. 1: This Page
|
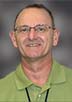
Michael Nausin,
CMMS project manager, Facilities & Engineering, Mineta San Jose International Airport
|
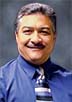
Frank Lucas,
Assistant Director of Work Management, Facilities Management & Planning, University of Nevada Las Vegas
|
|
Data is gold for maintenance and engineering departments in institutional and commercial facilities. Or at least it should be. But for too many managers, the process of gathering and analyzing data on maintenance activities and then acting on that data is overwhelming. Here, two managers who have helped their departments tap into the power of data share their experiences and insights.
When and why did your department begin paying attention to maintenance data?
LUCAS: We implemented a new CMMS (computerized maintenance management system) in 2002, and it was about 2004 when we got into the full swing with KPIs (key performance indicators). After two years with a CMMS is usually when you start to see some meaningful data collection. Since our department was in the middle of some major organizational and procedural changes, we wanted to measure the effectiveness of those changes and trend where we started to the present. We also wanted to start comparing our efforts to industry standards and to our peers to gauge how our performance measured up.
NAUSIN: In January 2007, the move to truly look at how work was being accomplished started airport department-wide (and) included adding a major terminal and remodeling the existing terminals and facilities simultaneously. The need to know what we had in the way of assets and how to maintain them was paramount because the airport's facilities division was using an application that truly was just a work-order system and nothing else.
Describe your department's strategy for effectively gathering and analyzing data.
NAUSIN: Once our understanding of (a new enterprise asset management system) started, we were able to start viewing what we wanted to see in the way of KPIs, which led to what type of data we needed and how to obtain and maintain said data. From this, we have been able to establish continuing training for staff (in order) to see shortfalls in a timely manner and address issues more efficiently today.
LUCAS: The effort to do accurate KPIs — or anything in a facilities department, for that matter — always has to start with a good data-collection process. It has to be accurate, and you have to categorize things correctly. We have procedural documents in place that guide these efforts. We perform data oversight reviews to ensure compliance and accuracy, and we involve everyone in the process at some level, which makes it a shared responsibility, and we monitor performance and take action where needed. We use this data in various reports. We also post our KPIs publicly. It keeps our employees engaged and aware of the business side of facilities management, and it has stimulated some great conversations when constituents from other departments, vendors and other visitors come into our area.
How did you identify essential KPIs for
your department?
LUCAS: You can literally KPI yourself to death, and everything gets lost in the jumble. We selected the ones that would give us the biggest bang for the buck and were easily understood by all because, again, we want technicians and other administrative employees looking at this stuff. We felt if we were achieving desired results within these measurements, we would have a good understanding of how we were trending across the entire operation. We didn't want to get caught up in managing to the numbers, which I think is a big mistake a number of organizations make. We look at work-order types to see where our labor hours are being spent. We'd like to see more hours being spent on PM (preventive maintenance) and fewer on repairs, obviously, but other factors come into play. Maybe you have an increase in man-hours doing modification and alteration work, which could cause repair hours to fall. You've really got to take a close look at that. We also like to monitor hours spent by payroll time type. This enables us to trend vacation hours, which allows us to better match our work schedules to when employees are expected to be on the job.
NAUSIN: In the beginning, I was developing and running reports that, in some cases, could be as long as 50-plus pages to disseminate the performance levels of either a particular shop or work group. From these various reports and working with the CMMS workgroup, we selected those areas that it would be easier for management, development, and deployment of KPIs, such as: PM performance in the previous 30 days; corrective maintenance in the previous 30 days; corrective maintenance labor work-order percentage; emergency work-order percentage; and PM work orders overdue. In all, we have developed and used 16 KPIs since 2010. The main KPIs that I monitor are for PM, first and foremost, and to ensure they are actually being accomplished, as well as to track the amount of labor hours being spent on PM work orders. (The reason we track) the labor hours is two-fold. Where can we compare and adjust the estimated time for the inspection on an annual basis? We also want to see if corrective maintenance is being done under the PM work order, which is not allowed. From here, we can associate breakdowns with PMs and determine the reliability of the equipment. For the past year, we have not added new KPIs, but there are a few that are on the planning board, like work-order completion compared to start vs. end date.
Can you give an example of tangible benefits resulting from the emphasis on data management?
NAUSIN: We have seen a huge swing in our preventive maintenance program. Almost eight years ago, literally there wasn't a PM program to speak of, and the numbers were 80 percent-plus corrective maintenance and less than 20 percent preventive maintenance. Today, through staff education, senior management backing, and attention to details, as of November 2014, preventive maintenance is at 72 percent, and corrective maintenance is at 28 percent.
LUCAS: During the recession, every department on campus was forced to take a budget cut of some kind, which was determined after a series of presentations. We were able to use the data from all of these KPIs and other metrics to prove what we do, identify the functions that impact the campus the most and, probably most importantly, identify what we wouldn't be able to do at the cut levels being considered. As a result, we ended up with a reduction in the cuts that we were forced to take.
What lessons have you learned related to data management and KPIs?
LUCAS: You can't prove how well you're doing or understand the effects of any changes you implement unless you monitor the results of your efforts in some manner. Financial managers, as we all know, understand numbers, and being able to show positive outcomes with the dollars you're given leads to more dollars when available. Being able to prove how wisely you spend those dollars earns trust and confidence. Reinvesting in facilities is a necessary evil of any institution, but it's an easier pill to swallow when you're able to show your constituents that you're doing so in a prudent and responsible manner. These days, with sustainability at the forefront of all facilities management decision making, using KPIs to effectively measure organizational performance becomes a real important piece of that process.
NAUSIN: By having a logical approach in place so that the data can be simplified in order to comprehend what the information is trying to say, this improves the understanding by everyone and allowed us to develop the application further and the incorporation of KPIs that have real meaning, instead of set parameters that relate to nothing. Having a KPI dashboard for managerial staff allows a quick view as to the progress of work orders, instead of the cumbersome review of multi-page reports trying to comprehend what the data is saying.
Related Topics: