view all Case Studies
Healthy Savings: New York Presbyterian Hospital Improves Energy Performance
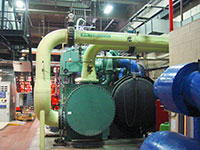
New York Presbyterian Hospital (NYPH) has two major campuses in New York City: NYPH-Cornell (downtown) and NYPH-Columbia (uptown). Together they comprise more than 8 million square feet of research and hospital space, and include an extensive grid of legacy utility plants.
May 23, 2011 -
Energy Efficiency
New York Presbyterian Hospital (NYPH) has two major campuses in New York City: NYPH-Cornell (downtown) and NYPH-Columbia (uptown). Together they comprise more than 8 million square feet of research and hospital space, and include an extensive grid of legacy utility plants. These provide steam, chilled water and electricity, and also allow adjacent users like Cornell Medical School to purchase excess capacity.
NYPH wanted to get a better handle on the metering and billing of its energy services. The hospital also wanted to improve the energy efficiency and cost-effectiveness of its existing facilities, focusing on chilled water generation efficiency. NYPH turned to utiliVisor, an energy advisory firm, to provide a web-based monitoring system and operations center energy analysts.
There were significant challenges. Some of the buildings are more than 100 years old and equipment included a variety of chillers with both steam turbine and electric drivelines as well as dual compressor centrifugal chillers with 4,500-ton capacities. Steam was being generated from both a boiler plant and a cogeneration system.
When looking for ways to be most cost-effective, the chilled water plants emerged as likely candidates. At the time, the generation of chilled water was costing the hospital in excess of $20 million per year. All existing equipment was tested for accuracy, and data from the various systems was pulled together in one platform and pushed to the web. Once all of the accurate data collection was completed, an analysis was done to understand how all the system components were working and determine the most efficient method of operating the plant.
Cost savings at NYPH were achieved in steps. By analyzing chiller operation at various loads and with different fuels, it was possible to establish an operating matrix that selects the most efficient/cost effective chillers to run as the hospital’s cooling load increases. Optimizing the cooling towers’ sequencing enhanced the performance of the entire system, balancing the amount of energy consumed at the different pieces of equipment and allowing chilled water to be generated at the best efficiency and lowest cost.
Other savings came from identifying measurement inaccuracies, calibrating temperature sensors, and highlighting inefficiencies in specific chiller performance, particularly heat exchanger performance. Excess pumping energy was eliminated. Lower condenser water temps were implemented for specific chillers. Flow through the plant and chillers was corrected to meet the design tonnages.
In addition to the optimization, the existing metering system was evaluated to ensure billing accuracy. On the downtown campus, new submetering will enable NYPH to verify its billing accuracy for each period of time according to the rate structure and company/utility provider agreement. The system will generate audits of all utility bills and perform exception reporting to compare any variations with previous months.
On an ongoing basis, the interface with utiliVisor enables continuous remote monitoring of the plants; monthly cost reports are submitted to NYPH engineers suggesting on-going system improvements.
For an initial capital investment of approximately $825,000 and a yearly monitoring cost of $85,000, NYPH has realized savings in excess of $1.75 million within the first six months of the project being implemented. And the efficiencies the program has created will allow the hospital to better handle the load requirements for future expansions.
Next
Read next on FacilitiesNet